Flanged butterfly valves have carved a niche in the industrial world for their efficient functionality and robust performance. Their design and application provide versatile solutions across a range of industries, reflecting a blend of innovation, expertise, and reliability.
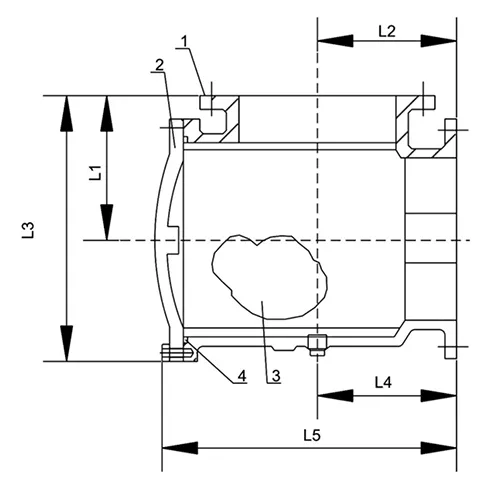
Flanged butterfly valves are integral components utilized primarily to regulate flow within a pipeline. Unlike gate, globe, or ball valves, butterfly valves offer a unique set of advantages that make them optimal for certain applications. They are particularly valued for their compact design and the ability to perform well in low-pressure conditions.
One of the standout features of flanged butterfly valves is their disc-shaped closing mechanism. This disc is mounted on a rotating shaft, allowing it to move from a fully open to a fully closed position, or any angle in between. This feature provides precise flow control and eliminates the turbulence that is often associated with other types of valves. The flanged design enhances the valve’s structural integrity, ensuring that it remains securely attached to the piping system while mitigating the risk of leaks and pressure loss.
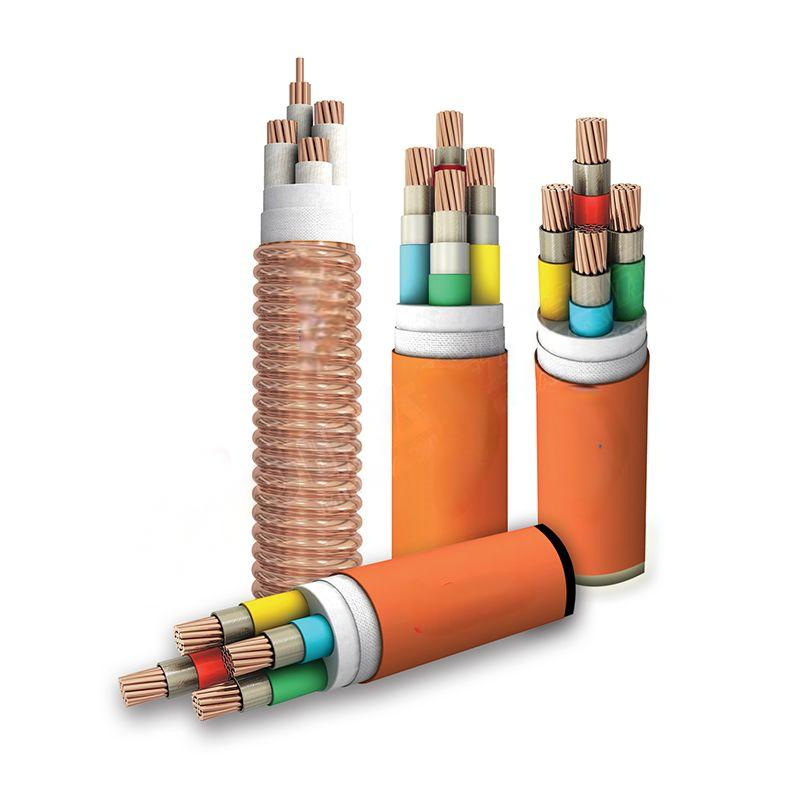
Industries such as water treatment, chemical processing, and oil and gas frequently rely on these valves due to their robust performance in handling large volumes of fluid. Chemical processing plants especially benefit from the corrosion-resistant materials used in the construction of these valves, which include stainless steel and high-performance polymers like PTFE. Such materials ensure that the valves can withstand harsh environments without compromising their functionality or longevity.
A real-world example of the efficiency offered by flanged butterfly valves can be seen in municipal water treatment facilities. These valves are employed due to their ability to handle varying pressures and volumes with ease. Their design allows for quick shut-off and precise control, crucial in maintaining the integrity of the water supply system. Furthermore, their ability to reduce energy consumption, due to the minimal friction loss, underscores their role in creating more sustainable operations.
flanged butterfly valve
Adding to their versatility, flanged butterfly valves cater to a range of actuation possibilities. They may be operated manually or through automatic actuators, including pneumatic or electric options. This adaptability is critical in modern industrial applications where automation is key to efficiency and safety. Facilities focusing on smart industry solutions often integrate these valves into their digital systems, enhancing monitoring and control capacities to optimize performance and preventive maintenance practices.
In terms of expertise, manufacturers offer a wide range of customization options. The selection includes differing sizes, materials, and pressure ratings, ensuring each valve is perfectly tailored to its specific application. Valve specialists can advise on optimal choices based on fluid type, operating conditions, and specific process requirements. This customization helps prolong the service life of the valve and reduces maintenance costs.
Notably, flanged butterfly valves align with contemporary industry standards for quality and environmental responsibility. They often meet stringent regulations and certifications that attest to their safety and eco-friendliness. Participating in eco-certification programs emphasizes a manufacturer's commitment to green production processes and product life cycles.
When discussing the authority and trustworthiness of flanged butterfly valves, reference is often made to long-standing brands known for their engineering excellence. Brands that have dominated the market for decades are valued for their reliable and expertly engineered products. Customers attest to the longevity and trouble-free operation of these valves, reiterating their status as a benchmark for new entrants in the field.
To conclude, the unique advantages of flanged butterfly valves position them as an unfavorable component in various settings. From their precise flow control and ease of operation to their durability and environmental compliance, they are a testament to the intersection of engineering prowess and practical application. As industry needs continue to evolve, these valves will undoubtedly remain a critical part of the infrastructure, adapting through innovation and continued focus on enhancing every aspect of their performance.