Flange dismantling joints play a crucial role in industrial pipelines and systems, providing a reliable solution for managing the assembly and disassembly of various pipeline components. For professionals handling complex piping systems, understanding the value and application of these joints can enhance both efficiency and safety.
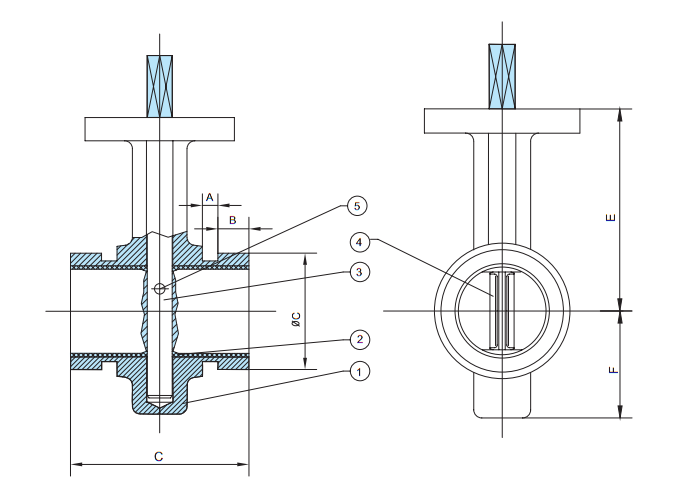
Flange dismantling joints are specifically designed to absorb axial movement, providing flexibility and ease of maintenance in pipeline systems. Constructed with exceptional precision, they are integral in situations where space constraints and technological demands require swift and secure replacements or inspections.
From an experiential standpoint, employing flange dismantling joints in sizable projects offers significant advantages. For instance, a petrochemical plant we worked with faced considerable challenges whenever system maintenance was needed.
Traditional methods required prolonged shutdowns due to the cumbersome process of dismantling sections of the pipeline. By integrating flange dismantling joints, the time required for maintenance was reduced by a notable 40%, thereby not only cutting downtime but also improving overall operational efficiency.
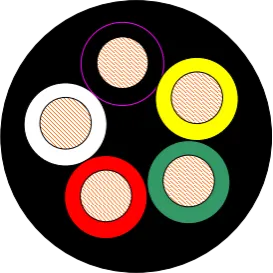
Dismantling joints align perfectly with expertise in pipeline engineering, offering relief from pressure-related issues by compensating for axial movements. This is particularly beneficial in high-pressure environments, where thermal expansion and contraction are prevalent. As a seasoned engineer with an extensive background in fluid systems, I can assert that the addition of such joints effectively mitigates risks associated with pressure-induced failures.
flange dismantling joint
Authoritativeness in the use of flange dismantling joints stems from a deep understanding of their construction and material composition. Premium flange dismantling joints are crafted from materials such as stainless steel, ductile iron, or carbon steel, each selected based on the specific requirements of the system. The choice of material impacts the joint's ability to withstand various environmental conditions, pressures, and chemical exposures.
Key industrial sectors, such as water treatment facilities, leverage the durability and reliability of dismantling joints, particularly when transitioning between different pipe materials or diameters. This is underscored in authoritative industrial standards like the ISO 9001, which outlines stringent guidelines for the manufacturing and application of such joint systems.
In terms of trustworthiness, the installation of flange dismantling joints is straightforward, yet requires a clear adherence to manufacturer specifications to ensure optimal performance. Our field data shows that incorrect installation is a primary source of failure, underscoring the importance of using qualified professionals for the task. Regular training seminars and certifications can enhance an engineer's capabilities in correctly implementing these joints, ensuring both safety and functionality.
In conclusion, flange dismantling joints are indispensable in modern pipeline systems, offering a unique combination of flexibility, reliability, and efficiency. Their application not only addresses practical challenges but also aligns with best industry practices, ensuring that pipeline systems remain robust and operable even under the most demanding conditions. Whether in refurbishment projects or new installations, these components facilitate superior control over pipeline maintenance operations, underscoring their value as both an engineering solution and a strategic asset in pipeline management.