Flanged swing check valves are an integral component in fluid handling systems across various industries. Renowned for their simplicity and reliability, these valves serve as guardians against reverse flow, ensuring the seamless operation of complex pipelines. In the world of valves, a comprehensive understanding of flanged swing check valves positions you to make informed decisions that enhance system efficiency and safety.
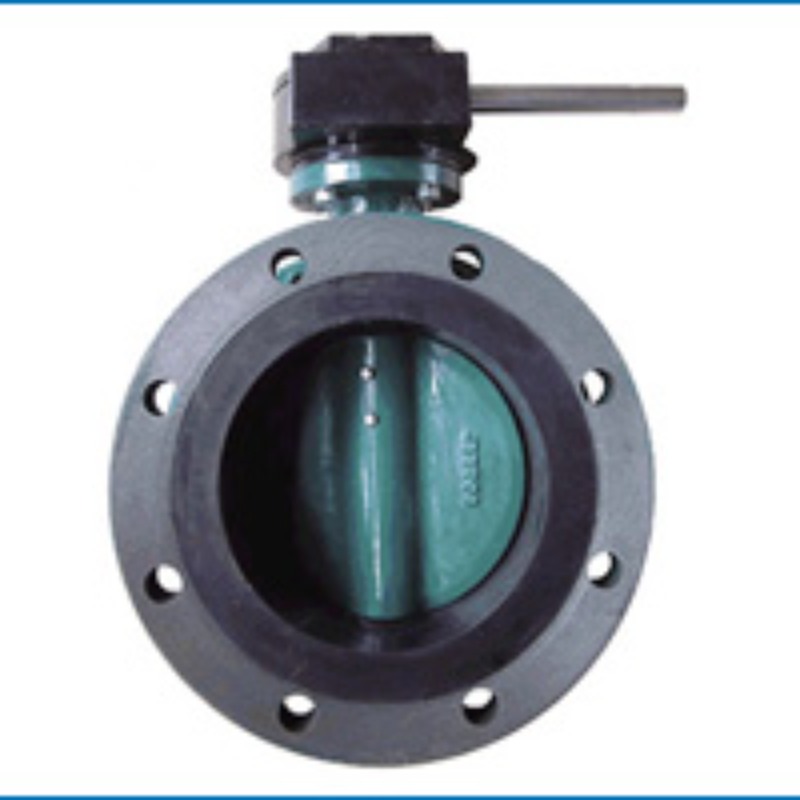
Flanged swing check valves operate by allowing fluid to flow in a singular direction while preventing backward flow. This unidirectional mechanism is vital for safeguarding pumps and compressors from potentially damaging reverse flows. These systems employ a hinged mechanism that swings open to permit flow and closes when the flow reverses, thanks to gravity or backpressure. This straightforward design makes them highly reliable and easy to maintain.
The expertise required in selecting the proper flanged swing check valve involves nuances tied to pressure ratings, body material, and application specifics. Their design allows for easy installation and efficient maintenance due to the accessible nature of flanged connections. Commonly constructed from robust materials like stainless steel, cast iron, and bronze, they provide substantial resistance to the wear and tear of continual operation. These materials are chosen not just for durability, but also for their compatibility with the media flowing through the system, whether it be water, oil, gas, or corrosive chemicals.
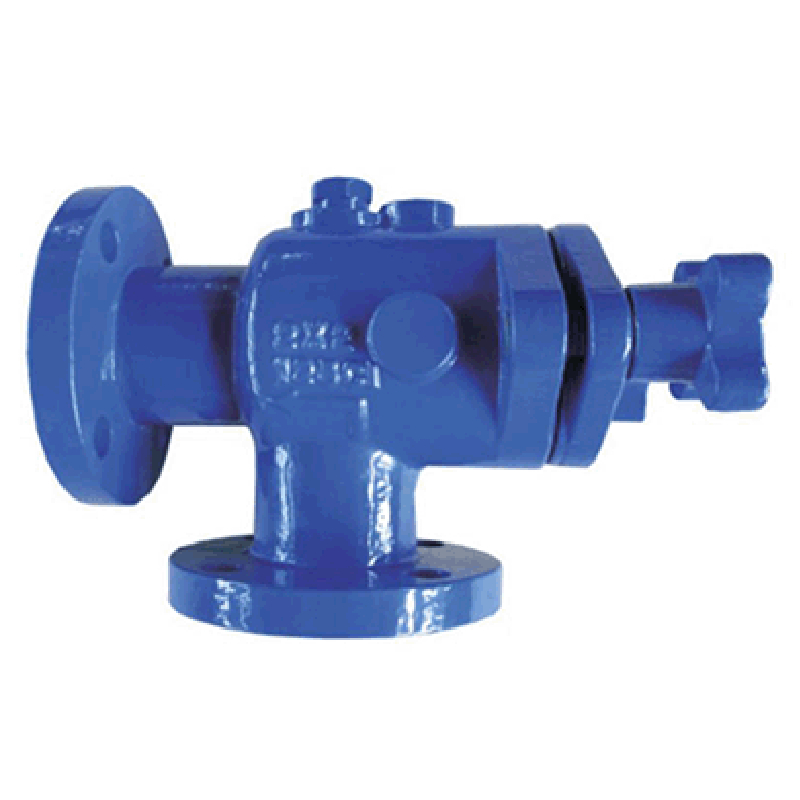
Authoritative analysis of recent industrial applications illustrates the versatility of flanged swing check valves. In water treatment plants, they ensure that treated water doesn't flow back into the untreated supply, which is crucial for maintaining public health. Similarly, in the oil and gas sector, they protect the integrity of pipelines by preventing backflow that could cause pressure surges and potential environmental hazards. These examples underscore their critical role in a wide range of operational contexts, where precision and reliability are paramount.
flanged swing check valve
Real-world experience underscores the importance of regular maintenance and the role of flanged swing check valves in system longevity. Operators often highlight the ease with which these valves can be inspected and serviced, requiring minimal downtime during routine maintenance. This advantage is critical in industries where prolonged shutdowns could lead to significant financial loss. Checking for debris build-up, ensuring the hinge mechanism operates smoothly, and verifying flange bolt integrity are all part of a routine maintenance schedule that can extend a valve’s operational life considerably.
The trustworthiness of flanged swing check valves is rooted not only in their functionality but also in their compliance with industry standards. Valves conforming to standards such as API 600 or ASME B16.34 assure users of consistent performance across varied operational pressures and temperatures. Compliance ensures that the manufacturing processes adhere to strict quality controls, thereby providing peace of mind regarding the product's reliability and durability.
End-users often cultivate relationships with trusted manufacturers who emphasize rigorous testing and product transparency. These manufacturers back their products with detailed documentation and support services, contributing to a high trust quotient among industry professionals. For businesses aiming to maintain sustainable operations, aligning with suppliers who value quality and customer satisfaction is a sound strategic move.
In conclusion, flanged swing check valves are essential for facilitating safe and efficient fluid dynamics in diverse industrial setups. Their reliability, supported by precise engineering and regular maintenance, not only protects vital infrastructure but also contributes to operational efficiency. By choosing high-quality products from reputable suppliers, industries can achieve and maintain high safety and performance standards, reinforcing the valves' longstanding reputation as dependable components in fluid management systems.