The wafer type butterfly valve stands out as a critical component in the control and regulation of fluid flow within industrial piping systems. As industries worldwide continue to seek efficient, reliable, and cost-effective solutions, this particular type of valve has garnered significant attention due to its unique design and functional capabilities.
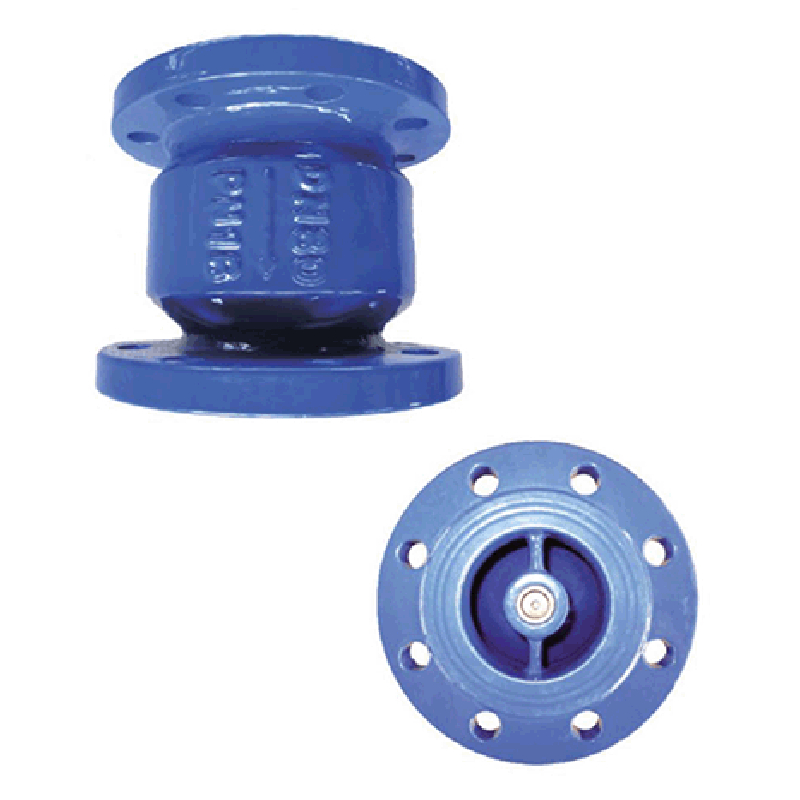
Expert insight into the wafer type butterfly valve reveals that its streamlined design is one of its primary advantages. Unlike other valve designs,
the wafer type does not require additional pipe flanges, reducing overall installation costs and saving space. This makes it particularly appealing in environments where space is at a premium, and efficient use of available area is crucial.
From an engineering perspective, the wafer type butterfly valve is engineered with precision. Its design allows for quick installation between two flanges in a piping system, ensuring minimal downtime during maintenance or replacements. The valve's disc is positioned in the center of the pipe and connected to an external actuator. Rotation of the actuator pivots the disc either parallel or perpendicular to the flow, offering precise control over the fluid passage. The simplicity of its mechanism translates into fewer components which, in turn, means a reduction in points of failure—an invaluable trait in maintaining system reliability.
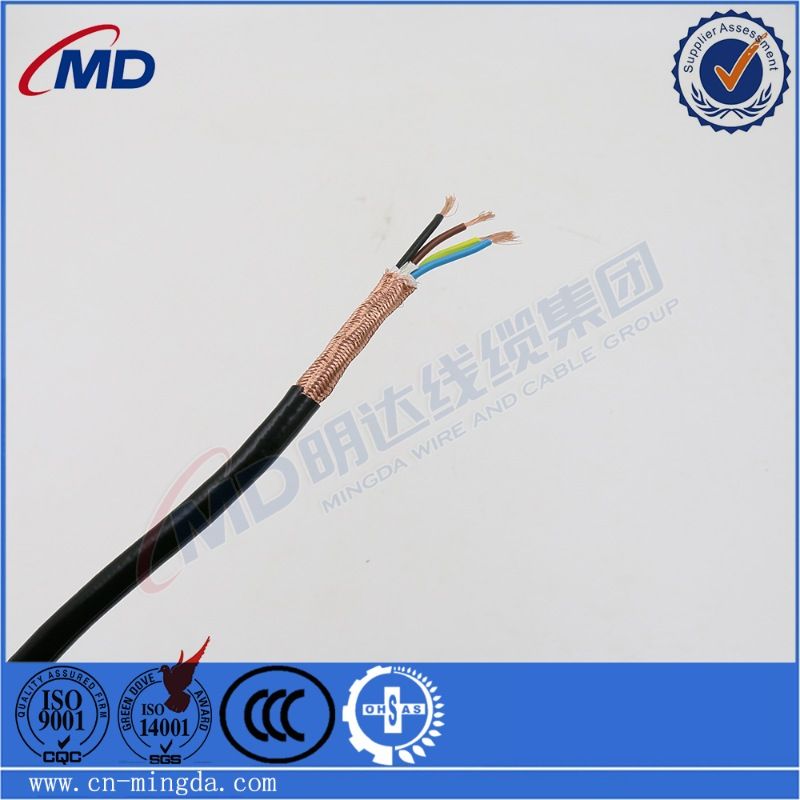
In terms of authority within the fluid control industry, wafer type butterfly valves are trusted by professionals across sectors such as chemical processing, water treatment, and oil and gas. The versatility of these valves means they are compatible with multiple types of media, including solids-laden fluids and high-viscosity liquids, further enhancing their adaptability and reliability across diverse applications.
Professional expertise asserts that selecting the right materials for wafer type butterfly valves is fundamental to their longevity and effectiveness. They are commonly available in a variety of materials, such as stainless steel, ductile iron, and PVC. These materials are chosen based on their ability to withstand different pressures, temperatures, and chemical compositions, ensuring that the valve performs consistently under specific conditions.
wafer type butterfly valve
One cannot ignore the valve's trustworthiness owing to its robust design and manufacturing standards. Leading manufacturers adhere to stringent quality controls and international standards, such as ISO and ASME, ensuring that these valves meet global performance benchmarks. Their enduring reputation is built upon consistently delivering valves that offer low torque requirements, minimal pressure drops, and high wear resistance.
Furthermore, maintenance-friendly features such as replaceable seat rings and self-cleaning capabilities contribute to their operational longevity. With proper care and routine inspections, wafer type butterfly valves can continue to perform effectively for many years.
Real-world experience also underscores the importance of proper installation and maintenance to maximize the lifespan and efficacy of wafer type butterfly valves. Users consistently stress the necessity of correct alignment during installation, which prevents disc damage and ensures optimal valve performance. Routine inspections and cleaning play a vital role in system functionality, preventing premature wear and potential failure.
In conclusion, the wafer type butterfly valve exemplifies a blend of engineering expertise, industry authority, and operational trustworthiness, making it a preferred choice for fluid control solutions. Its unique design offers numerous advantages that cater to the demands of modern industrial applications. As industries continue to innovate and evolve, the role of the wafer type butterfly valve is poised to expand, reinforcing its status as a cornerstone of efficient fluid management.