Choosing the right components in industrial settings often defines operational efficiency and longevity. One such critical component is the wafer style butterfly valve. Known for its compact size and efficient sealing capabilities, understanding the nuances of this product can significantly impact any industry utilizing fluid control systems.
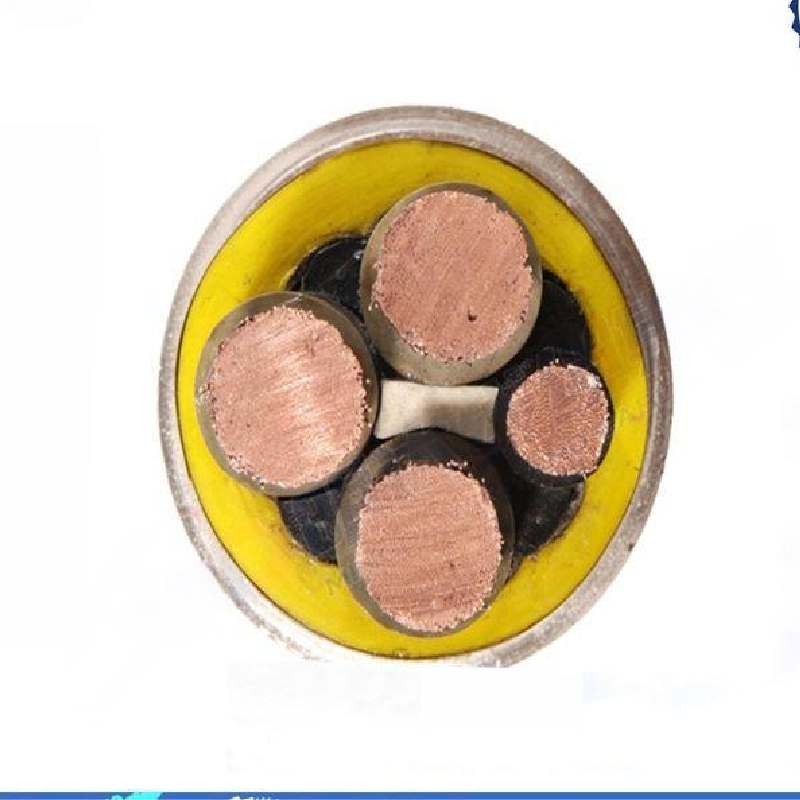
Wafer style butterfly valves have found widespread application in industries ranging from water treatment and chemical manufacturing to food processing and pharmaceuticals. The defining feature of this valve is its wafer design, which offers a streamlined method of installation between flanges, held in place by long bolts running from one flange to the other. This design facilitates not only easy installation but also convenient maintenance and replacement, proving to be a cost-effective solution over time.
In terms of expertise, the wafer style butterfly valve excels through its structural simplicity, which translates to fewer potential failure points and thus heightened reliability. Unlike its more complex counterparts like the ball valve, the butterfly valve utilizes a disc that rotates a quarter turn to open or close the valve. This simple operation allows for quick actuation which is ideal in scenarios where rapid valve response is critical. Furthermore, its design allows for control over large flows with minimal pressure drop, enhancing energy efficiency within the system.
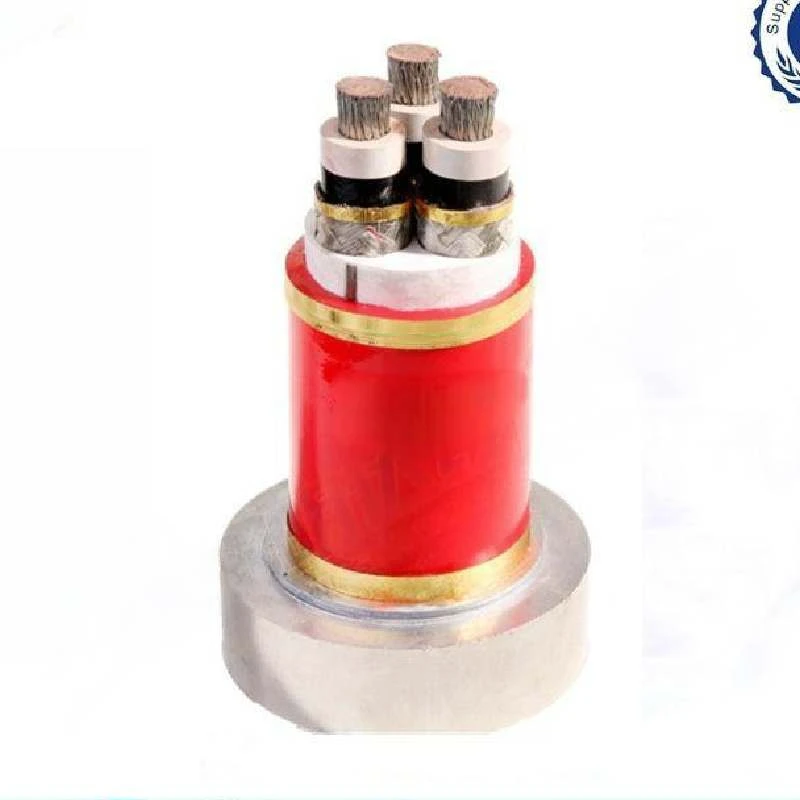
Authoritativeness stems from the engineering precision that goes into manufacturing wafer style butterfly valves. Industry leaders in valve manufacturing adhere to stringent quality standards such as ISO 9001 to ensure valves provide consistent performance under various temperature and pressure conditions. The use of diverse materials like stainless steel, ductile iron, and high-performance polymers further broadens the applicability of these valves, catering to industry-specific requirements, such as corrosion resistance in chemical plants or hygiene compliance in food production facilities.
wafer style butterfly valve
Credibility is reinforced through real-world performance and customer testimonials. Users often note the resilience of these valves in high-cycle environments, highlighting their robust construction and the reliability of their seal — typically composed of either PTFE, EPDM, or other elastomeric materials, depending on application needs. Frequent customer feedback emphasizes the practicality of the wafer style in scenarios of limited space, which is common in retrofitting older systems or in high-density installation layouts.
From experience, the strategic placement of wafer style butterfly valves in pipeline systems can considerably reduce initial setup costs and ongoing maintenance expenses. Their lightweight design contributes not just to reduced material and machining expenses, but also to lower shipping costs, which is a substantial factor for industries operating across borders. Over the decades, many companies have adopted wafer style butterfly valves for their enhanced efficiency, affirming their decision through sustained system performance and lowered operational costs.
In summary, the wafer style butterfly valve represents a convergence of innovation, efficiency, and reliability. Its widespread acceptance across various sectors is a testament to its design advantages and performance robustness. As industries continue to seek ways to optimize their fluid control systems, the wafer style butterfly valve remains an exemplary choice—balancing simplicity with advanced operational capabilities. When selecting a valve, one benefits greatly from considering not just the immediate applicability but also the long-term value that such a well-engineered component brings to an industrial setting.