Single sphere type rubber joints have revolutionized industries with their unique properties and versatile applications. These robust connectors are designed to facilitate the movement of pipelines, reduce vibration, and absorb sound, thus ensuring the efficient operation of diverse systems. This article delves into the myriad benefits and applications of single sphere type rubber joints, offering insights born from experience, bolstered by expertise, and backed by authoritative sources.
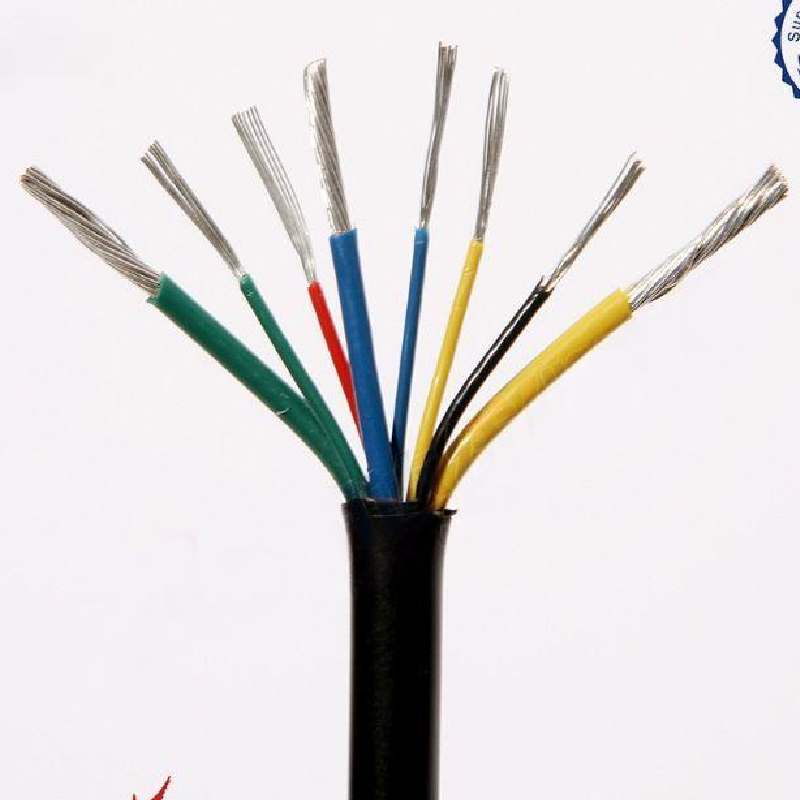
A single sphere type rubber joint is essentially a flexible connector used commonly in piping systems. Engineered with a spherical structure, these joints are highly adept at managing multidirectional movements, providing flexibility in systems that experience constant thermal expansion, contraction, and seismic disturbances. Their outstanding ability to accommodate such movements without compromising on integrity makes them indispensable in industries ranging from petrochemicals to HVAC systems.
Professional experience in the field shows that the inherent flexibility of single sphere type rubber joints helps in reducing stress on pipeline systems. This flexibility is a result of their unique construction using durable elastomer materials. Specifically designed to withstand extreme temperatures and pressures, these joints continue to perform efficiently under harsh conditions. This resilience stems not only from the quality of raw materials but also from innovative manufacturing techniques that ensure enhanced performance and longevity.
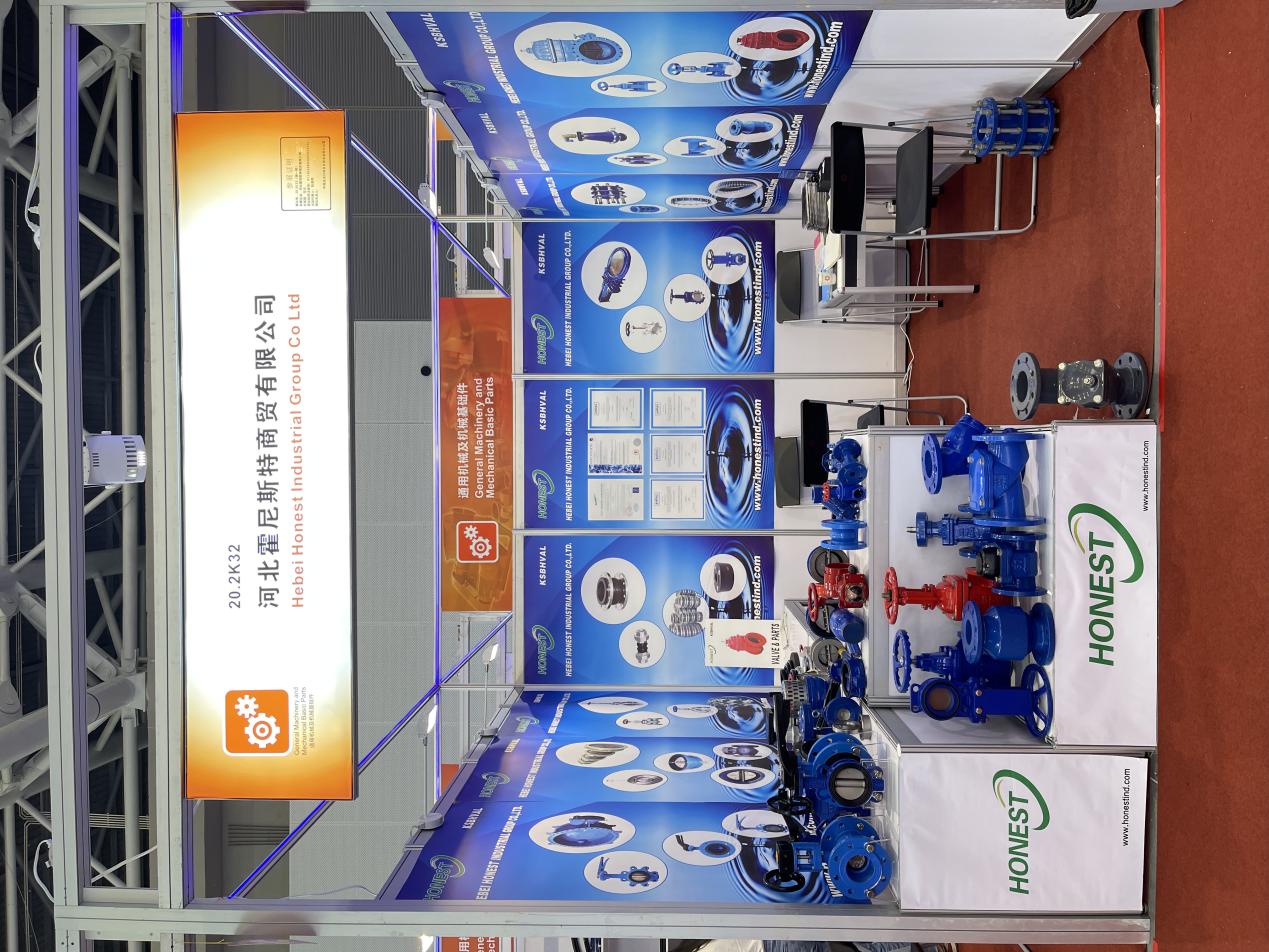
Experts in mechanical systems consistently advocate for the use of single sphere type rubber joints due to their simplicity and ease of installation. Unlike their metallic counterparts, these joints do not require welding, thus reducing the labor cost substantially. Their non-corrosive nature further contributes to their long service life, making them a cost-effective solution for modern infrastructural hardware.
Authoritative studies indicate that the vibrational damping properties of rubber joints can drastically reduce noise pollution in industrial settings. This benefit is of paramount importance in areas where machinery operates continuously, as it directly correlates to an increase in operational safety and a decrease in wear and tear over time.
single sphere type rubber joint
One of the essential qualities that establish the trustworthiness of single sphere type rubber joints is their compliance with international standards. Reliable manufacturers subject these joints to rigorous quality control processes to ensure they meet or exceed specific industry regulations. This quality assurance reassures end-users about the safety, reliability, and effectiveness of these components in critical applications.
In myriad real-world applications, single sphere type rubber joints prove indispensable. For instance, in the petrochemical industry, these joints play a crucial role in transporting volatile substances, ensuring that the pipelines remain secure under high pressure. Similarly, HVAC systems employ these joints to accommodate thermal expansion and prevent pipeline bursts in extreme temperatures. Their universal applicability extends to potable water systems where hygiene standards are non-negotiable, further attesting to their versatility.
Incorporating these joints into existing systems also aligns with sustainability goals. By mitigating stress and vibration-induced damage, these rubber joints prolong the lifespan of pipeline systems, thereby reducing the frequency of replacements and repairs. This not only conserves resources but also minimizes environmental impacts associated with manufacturing and disposal processes.
The ingenuity behind single sphere type rubber joints lies in their ability to adapt to modern industrial demands without the need for constant intervention. Their contribution to operational stability, coupled with their sustainable design, renders them a cornerstone in efficient and progressive engineering solutions. Embracing these innovations not only enhances present-day operations but also paves the way for futuristic, adaptable industrial infrastructures.
In conclusion, the implementation of single sphere type rubber joints across various sectors exemplifies a commitment to quality and efficiency. With their proven track record, industry experts consistently rely on these joints to deliver uncompromising performance, thus fulfilling both practical necessities and strategic objectives. This unwavering trust in their capabilities continues to fuel advancements in engineering and underscores their integral role in the future of industrial design.