Rubber joints, essential in various industrial applications, provide flexibility and support to systems, safeguarding them from damage. These highly versatile components, typically utilized in piping systems, are designed to absorb noise and thermal movements, addressing crucial needs while maintaining system integrity.
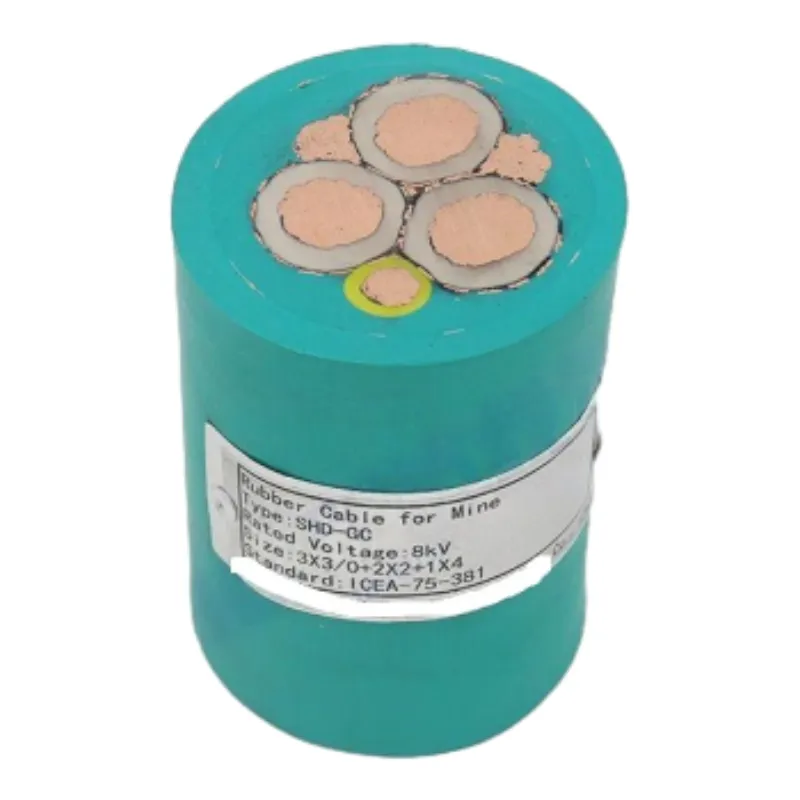
Delving into an intricate understanding, rubber joints primarily serve to alleviate the stresses exerted by vibration, pressure, and thermal fluctuations. Given their elasticity, they accommodate movement in three planes, serving as a resilient buffer. For industry experts, understanding material composition is crucial; these joints are typically made from natural or synthetic rubber, reinforced with metal, fiber, or nylon for enhanced durability.
The selection process for a suitable rubber joint is not merely a cursory task. It requires an evaluation of several critical factors, including temperature resilience, media compatibility, and pressure rating. Experts often stress the importance of a meticulous assessment to ensure optimal performance. Misalignment or inappropriate selection may lead to premature failure, potentially compromising the entire system. In oil and gas industries, where environments often reach high temperatures, EPDM (ethylene propylene diene monomer) rubber joints are preferred for their superior heat resistance. Conversely, for chemical plants dealing with aggressive substances, experts recommend Viton rubber due to its chemical inertness.
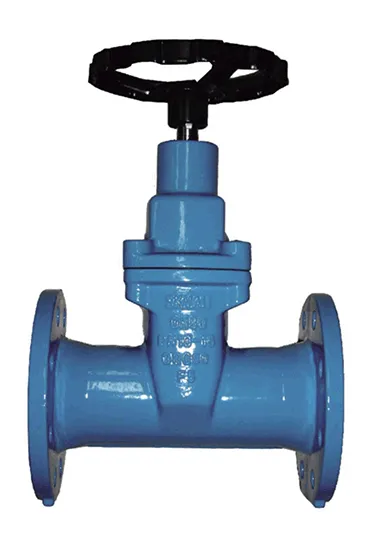
Applications are diverse, spanning HVAC systems, water treatment plants, and marine settings. In heating, ventilation, and air conditioning (HVAC) systems, where constant pressure and temperature shifts occur, rubber joints play an indispensable role in mitigating noise and movement. An experienced technician might describe the palpable difference in sound levels post-installation, emphasizing their efficacy in noise reduction.
Rubber joints in water treatment facilities demonstrate another facet of versatility. Highly corrosive environments and fluctuating pressures are a norm here; thus, reinforcing rings and flanges are often integrated into the design for added strength and security. An authority in this field might note how this strategic incorporation drastically enhances performance, minimizing wear and increasing lifespan.
rubber joint
In marine environments, where salty conditions accelerate corrosion, the dependency on rubber joints extends beyond mere functionality. Here, selecting materials that resist saltwater corrosion is imperative, often leading experts to utilize chloroprene rubber for its robust anti-corrosive properties. Industry authority often showcases case studies where the strategic choice resulted in minimal maintenance and longer operational life, underpinning the trustworthiness of such material decisions.
The expertise in deploying rubber joints extends to maintenance practices. Ensuring longevity involves regular inspection for wear and tear, particularly checking for bulges or leaks that might indicate emerging issues. A seasoned industry expert would stress on scheduled maintenance, asserting that proactive measures can significantly extend operational life, reduce downtime, and enhance safety.
For enhanced reliability, collaborations with recognized manufacturers are vital. Established entities often adhere to stringent quality standards, providing test certificates and material data sheets to boost client confidence. Procuring from credible sources ensures adherence to international standards like ISO 9001, which guarantees quality and safety.
In sum, the effective utilization of rubber joints is contingent upon a comprehensive understanding of their composition, application potential, and maintenance practices. These components are pivotal in various industrial milieus, offering solutions to complex engineering challenges. Engineers, by leveraging their expertise and adhering to authoritative standards, can ensure these joints serve as reliable components within their systems, enhancing overall efficiency and safety. The journey from selection to installation and maintenance is replete with nuanced decisions that underscore the profound trust in these resilient rubber components. This trust is built not just through experience but a relentless pursuit of excellence and safety, ensuring these joints continue to be indispensable across industries.