The world of industrial components is vast, yet the air valve stands out as a cornerstone of innovation and efficiency in fluid control systems. Despite its unassuming presence, the air valve is critical for maintaining pressure and ensuring the optimal functioning of pipelines and hydraulic systems across various industries.
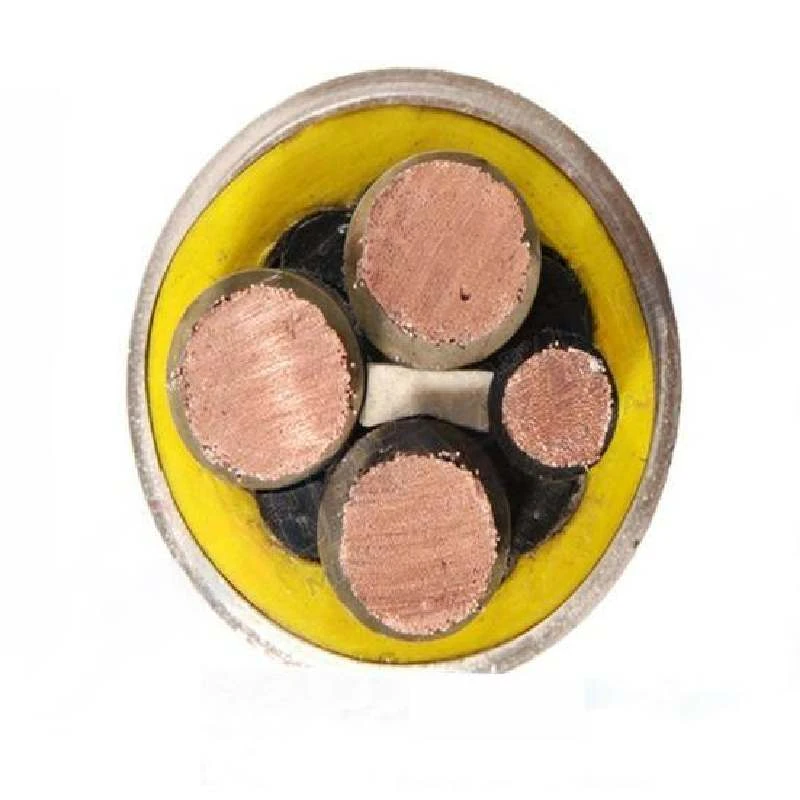
At its core, an air valve regulates air flow within a system, preventing issues like pressure buildup or air entrapment that can severely hinder performance. The advantages of using high-quality air valves extend beyond mere pressure control. They contribute to system longevity and operational stability, minimizing downtime and maintenance costs. With rigorous engineering and precision manufacturing, modern air valves are crafted to endure harsh environmental conditions, offering consistent performance even in the most demanding applications.
From industrial manufacturing to municipal water distribution, the deployment of robust air valves is a testament to the expertise investing into their designs. For instance, in the context of a complex municipal water system, the correct installation of air valves can prevent catastrophic scenarios, such as pipeline bursts, thereby emphasizing their role in safeguarding public infrastructure.
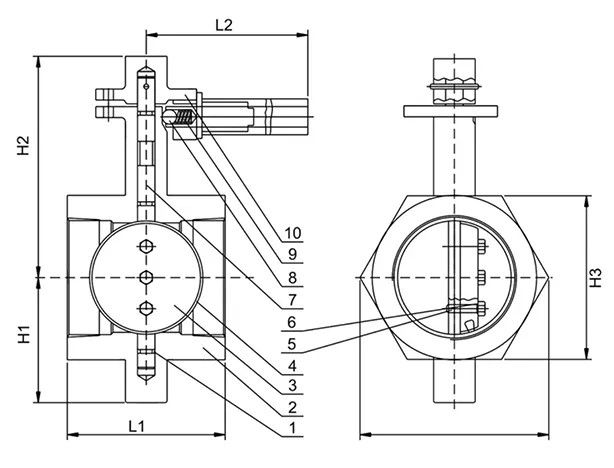
Furthermore, the expertise in the design of these valves is reflected in the variety available in the market. Different environments and pressures require specific types of air valves, such as automatic air release valves, vacuum breakers, and combination air valves. Each type serves a specialized function, ensuring that the system in which they are integrated operates smoothly and efficiently. Automatic air release valves, for example, are crucial in systems where air accumulation is a constant issue, as they automatically vent trapped air without manual intervention.
air valve
Choosing the right air valve extends beyond just addressing the immediate needs of a system. It requires an authoritative understanding of the system's comprehensive requirements, including flow dynamics, environmental considerations, and long-term operational goals.
Consulting with experts in fluid dynamics is critical. These professionals bring authoritative knowledge to the table, ensuring that the chosen components align with both current operational needs and future scalability considerations.
Trust in the reliability and performance of air valves is foundational. Trustworthiness is established through rigorous testing and adherence to international standards such as ISO and ASME. These standards ensure that air valves not only meet but often exceed industry expectations in terms of durability, efficiency, and safety. Manufacturers committed to quality control not only test their air valves for performance under varied conditions but also provide certifications that reinforce their trustworthiness in the eyes of engineers and operators alike.
In today's ever-evolving technological landscape, the incorporation of digital monitoring systems within air valves represents a leap forward. Smart air valves equipped with sensors and IoT capabilities present a paradigm shift, allowing real-time monitoring and predictive maintenance capabilities. This innovation not only enhances the efficiency of fluid control systems but also offers valuable data-driven insights that can be used to optimize operations and preempt issues before they escalate.
In conclusion, the air valve's role in industrial applications cannot be overstated. Its presence guarantees efficiency, safety, and reliability within fluid control systems, embodying a blend of practicality and advanced engineering. By investing in high-quality, smart solutions and collaborating with experts, industries can harness the full potential of air valves to drive operational excellence and sustainable growth. In the pursuit of efficiency and precision, air valves remain indispensable, continually adapting to meet the demands of modern industry and future innovations.