When it comes to selecting the best rubber expansion joint, the primary concern for many industry professionals is cost versus quality. While determining the most appropriate rubber expansion joint price points, numerous factors must be considered, from material selection to manufacturing standards, ensuring you achieve a balance between expenditure and efficiency.
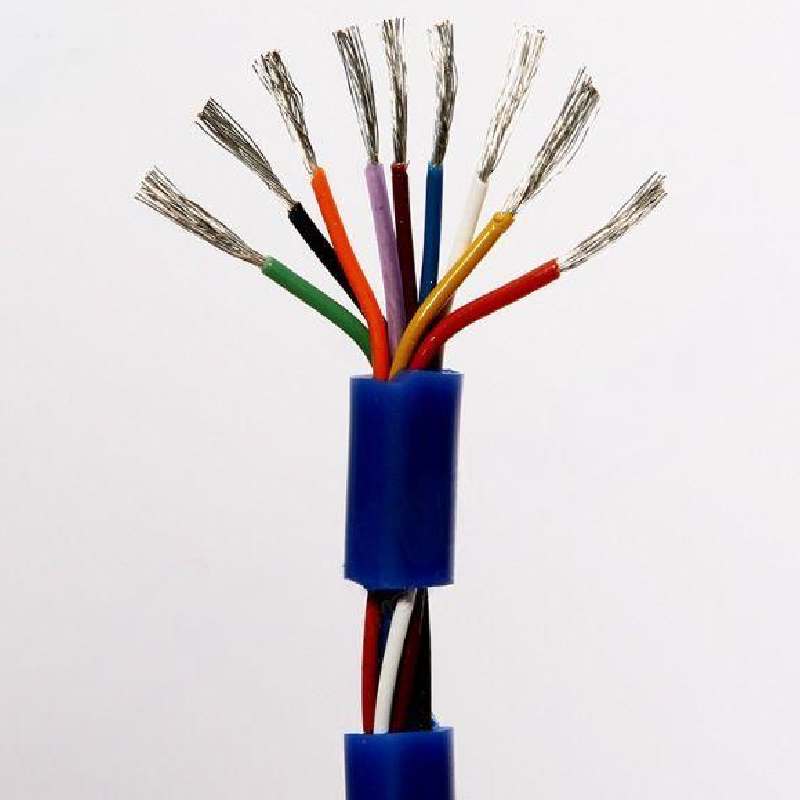
Understanding the Role of Rubber Expansion Joints
Rubber expansion joints are pivotal in many industrial applications, serving as critical components in piping systems. They efficiently absorb vibrations, compensate for misalignment, and allow for movement due to thermal expansion or contraction. The flexibility they provide is invaluable, particularly in environments subjected to fluctuating temperatures and pressures.

Expert Insight into Material Choices
The choice of material plays a significant role in the pricing of rubber expansion joints. The most common materials include EPDM, Neoprene, and Nitrile. EPDM (Ethylene Propylene Diene Monomer) is renowned for its excellent resistance to weathering, ozone, and UV exposure, making it ideal for outdoor applications. Neoprene offers impressive oil resistance, while Nitrile, known for its excellent thermal stability, is often used in extreme temperature scenarios. The cost of rubber expansion joints is directly influenced by these material compositions, which are selected based on the specific requirements of your project.
Manufacturing Standards Dictate Performance and Price
The fabrication process and standards to which rubber expansion joints are made can significantly impact their price. Premium joints are often produced under stringent quality controls and adhere to international standards such as ASTM or DIN specifications. These joints, though pricier, guarantee a longer lifecycle and minimal maintenance issues. Lower-cost options might forego these rigorous standards, offering short-term savings at the expense of potential long-term performance.
Assessing the Impact of Joint Design on Cost
Design intricacies in rubber expansion joints, such as the number of arches (single or multiple), connector types, and flange materials, contribute substantially to pricing. Single-arch designs are generally less expensive but might lack the flexibility offered by multiple-arch options, which are adept at handling larger movements and pressures. Stainless steel flanges, while adding to the cost, provide superior corrosion resistance compared to carbon steel options.
rubber expansion joint price
Industry Experience – Choosing the Right Supplier
Deciding upon a reliable supplier is crucial when considering rubber expansion joint prices. Experienced suppliers not only offer competitive pricing but also provide insights into customizing joints that best fit your applications. They help in selecting the most cost-effective solutions without compromising performance thanks to their in-depth industry knowledge and comprehensive range of products.
Trust in Testing and Certification
The credibility of rubber expansion joints is often validated through testing and certification by third-party agencies. These certifications guarantee that the product meets or exceeds industry expectations for safety and reliability. Investing in certified rubber expansion joints may initially appear cost-intensive but can result in reduced liability and extended asset longevity.
Total Cost of Ownership Versus Initial Price
While the initial purchase price is an essential consideration, evaluating the total cost of ownership (TCO) provides a more comprehensive understanding of the rubber expansion joint’s value. TCO encompasses not only the initial purchase price but also factors such as installation costs, maintenance, and replacement expenses over the product's life span. Opting for a higher-quality product may reduce these additional costs due to less frequent maintenance and a longer lifecycle.
Case Studies Real-World Applications
In practical scenarios, businesses that invested in higher-quality, well-certified rubber expansion joints reported fewer system shutdowns and maintenance interventions, translating into overall cost savings. Conversely, those who opted for cheaper, non-certified joints frequently encountered premature failures, leading to increased downtime and repair costs.
In conclusion, when evaluating rubber expansion joint prices, it is essential to balance initial cost considerations with long-term reliability and performance expectations. By focusing on material quality, manufacturing standards, joint design, and reliable supplier partnerships, you can secure the most cost-effective provider that ensures your systems operate smoothly and efficiently. Access to certified products that uphold the necessary standards can significantly enhance trust in their performance, ultimately safeguarding your investments in the long run.