Rubber expansion joint flange types have become indispensable components within myriad industrial applications due to their unparalleled flexibility and resilience. These crucial components are especially relevant in industries that experience significant pressure and temperature variations. Knowing the intricacies of these joints not only enhances system efficiency but also maximizes their lifespan, thereby offering significant cost savings.
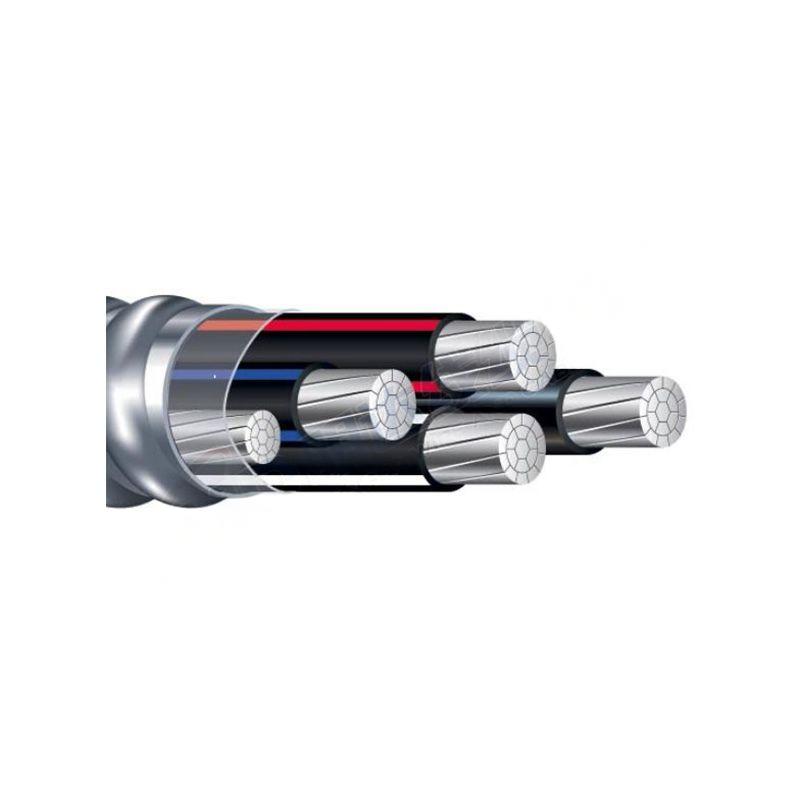
Rubber expansion joints, primarily the flange type, serve the vital purpose of absorbing sound, thermal energy, and movement. Their design consists of a rubber loop with metallic flanges at both ends, facilitating connection to various types of piping systems. These flanges boost the adaptability of the joint, making them suitable for handling fluids and gases under variable conditions.
An aspect that sets flange-type rubber expansion joints apart is their versatility. Applicable in sectors like HVAC, petrochemical, water treatment, and marine industries, these joints can sustain extreme conditions. A flange composed of materials such as carbon steel, stainless steel, or ductile iron is paramount in providing strength and stability to the joint, besides making it compatible with different end connections. This adaptability permits the joints to accommodate axial, lateral, and angular movements, thus serving as a deterrent to potential system fatigue or rupture.
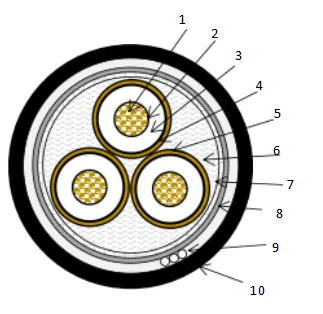
Selecting the right flange-type rubber expansion joint entails understanding various significant parameters. This includes considering the material of the rubber, which could range from Nitrile Butadiene Rubber (NBR) to Ethylene Propylene Diene Monomer (EPDM), each offering distinct advantages. For instance, EPDM is renowned for its resistance to weather, ozone, and chemicals, making it a go-to choice for HVAC systems. Conversely, NBR stands out for its excellent resistance to oil and fuel, thus finding utility in the petrochemical industry.
In tandem with material selection, understanding the operating environment is crucial. Variables such as pressure, temperature, and the type of fluid conveyed play roles in determining the ideal expansion joint. For instance, higher temperatures often necessitate the use of a joint with thermal stability, which is resistant to thermal stress and has a high expansion coefficient. Notably, adherence to international safety and quality standards such as the ANSI, ASTM, or DIN is non-negotiable, ensuring reliability and safety in application.
rubber expansion joint flange type
One must not overlook proper installation and maintenance practices when maximizing the utility of flange-type rubber expansion joints. A correctly installed joint not only ensures a seamless operation but also prolongs its service life. This involves securing the joint in a way that allows natural expansion and contraction without overstressing the rubber component. Regular inspections and maintenance checkups are advised to preemptively identify signs of wear and tear or material fatigue.
Being an industry expert offers insights into unforeseen complications that may arise, such as rapid pressure changes, which can cause water hammer effects—leading to joint failure. To mitigate such risks, systems should be equipped with proper pressure management apparatuses such as surge suppressors or automatic control valves.
For organizations focusing on sustainable practices, rubber expansion joints offer an environmentally friendly solution. The longevity and durability of these joints reduce waste and material consumption, aligning with broader ecological goals. Moreover, their ability to mitigate vibrations and noise aligns with creating more sustainable and worker-friendly industrial environments.
In essence, the flange-type rubber expansion joint epitomizes a blend of technical prowess and practical utility. Experts within industrial sectors anticipate a continued evolution of these joints, propelled by advancements in material science and engineering technologies. By fostering robust collaborations with manufacturers and leveraging cutting-edge research, industry leaders can ensure the continued reliability and performance of these essential components.
Rubber expansion joint flange types have cemented their status as cornerstones in industrial applications. A deep dive into their characteristics, benefits, and best practices for selection and maintenance substantiates their indispensable role across various industries. Understanding and leveraging the expertise surrounding these components ensure operational excellence and longevity in complex piping systems.