Rubber expansion joint flange types have become an essential component across a variety of industries, known for their ability to absorb sound, thermal dynamics, and vibration. With a rich history and continual advancements, understanding these components is paramount for engineers, technicians, and procurement specialists focused on developing efficient and long-lasting systems.
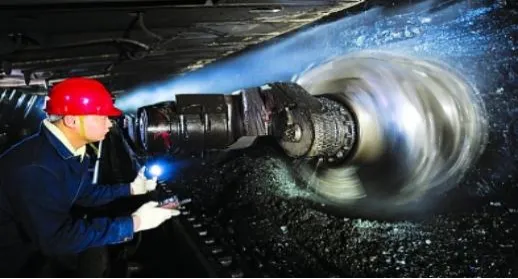
When it comes to rubber expansion joints, flange type refers to the method by which these joints connect with other components within a pipeline or system. Flanged ends allow for straightforward installation and removal, a property that underscores their popularity in heavy industry applications including water treatment facilities, chemical processing plants, and HVAC systems.
The usage of high-quality elastomers in these joints provides the flexibility needed to accommodate movement caused by thermal expansion, ground settlement, equipment vibrations, and pressure changes. This flexibility helps protect expensive equipment from damage and extends the operational life of pipelines.
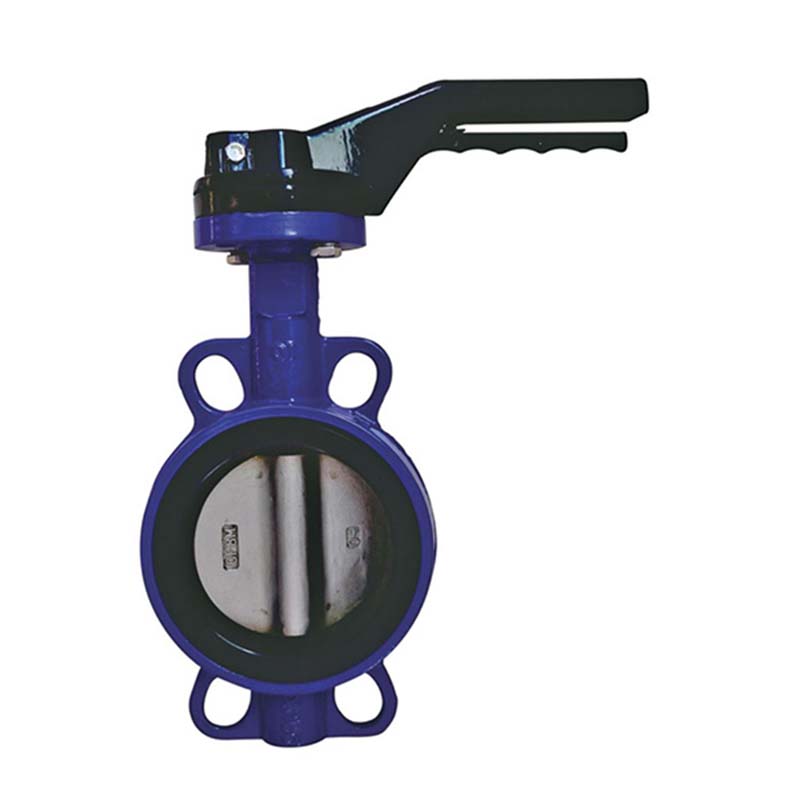
Professionals value rubber expansion joints with flange types for their role in noise and vibration damping. Within large-scale mechanical installations where noise reduction is not just a preference but a necessity, these joints prove invaluable. For instance, in petrochemical plants where continuous equipment operation is critical, the application of noise-dampening components is essential for maintaining both workplace safety and comfort. Furthermore, they reduce strain on anchors and supports, helping maintain structural integrity in complex systems.
From an expertise viewpoint, selecting the correct rubber material is as crucial as choosing the appropriate flange type. EPDM, neoprene, nitrile, and natural rubber elastomers each offer unique properties – EPDM is resistant to weathering and UV rays, making it ideal for outdoor applications, whereas nitrile is preferable for oil-related industries due to its superior resistance to oils and hydrocarbons.
rubber expansion joint flange type
For those harnessing the true potential of flange-type rubber expansion joints, understanding the pressure and temperature ranges they will be subjected to is key. Experience indicates that tailor-fitting these components to specific operational conditions – for example, ensuring that they are rated for the maximum system pressure and pump discharge temperatures – minimizes the risk of failure. This bespoke approach is supported by years of field data and testing, reflecting a comprehensive understanding of both material science and engineering principles.
Reputation and trustworthiness play a pivotal role in the selection and purchase of these joints. Reputable manufacturers often provide certifications from recognized testing bodies, ensuring that products meet industry standards. Trustworthy suppliers also offer comprehensive support, from initial product selection and technical consultations to after-sales service, ensuring that their components maintain performance over the long term.
The professional landscape surrounding rubber expansion joint flange types is grounded in both historical knowledge and contemporary innovation. Modern advancements have led to joints that are not only more effective but also more environmentally friendly, using materials that reduce impact without sacrificing performance.
This continuous innovation ensures that industries relying on heavy machinery can optimize efficiency while minimizing disruption and equipment wear. As industries evolve, the products employed must also adapt, and rubber expansion joints with flange types represent this dynamic balance between tradition and technological advancement.
In summary, these components hold a crucial balance between real-world application and detailed engineering expertise. Their role in extending the lifespan of equipment and reducing operational noise and vibration makes them indispensable in various industrial sectors. Understanding their material properties and ensuring partnerships with reputable providers will not only bolster system reliability but also innovate future applications as industry standards evolve.