The industrial globe valve stands as a critical component within various industrial systems, ensuring reliable flow control and efficiency across numerous applications. These valves are specifically designed for precise throttling and regulation of flow in both liquid and gas systems, making them indispensable in industries such as oil and gas, chemical processing, and power generation.
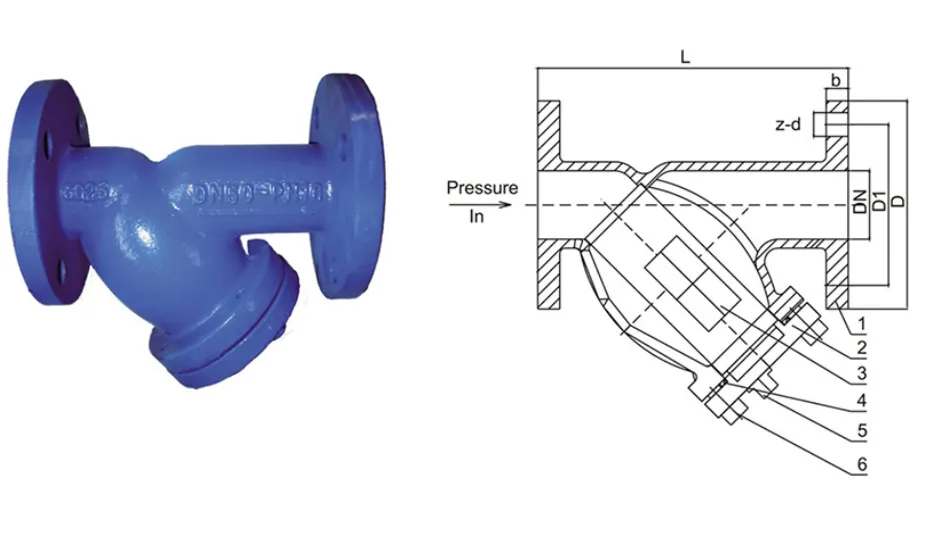
Globe valves are engineered with a spherical body and a movable disk-type element inside, which helps them achieve precise adjustments of flow. Unlike gate valves, which are mainly used for on/off control, globe valves are better suited for applications that require frequent operation and fine tuning. This feature is particularly valuable in industrial processes where fluid characteristics can vary and responsiveness is key.
In terms of expertise, selecting the right industrial globe valve requires a comprehensive understanding of the system requirements, including pressure, temperature, and flow considerations. Engineers must evaluate the materials used in valve construction, such as stainless steel, bronze, or cast iron, which determine the durability and corrosion resistance of the valve. This choice impacts the valve’s performance under different environmental conditions and its ability to withstand harsh chemicals, high temperatures, or significant pressure fluctuations.
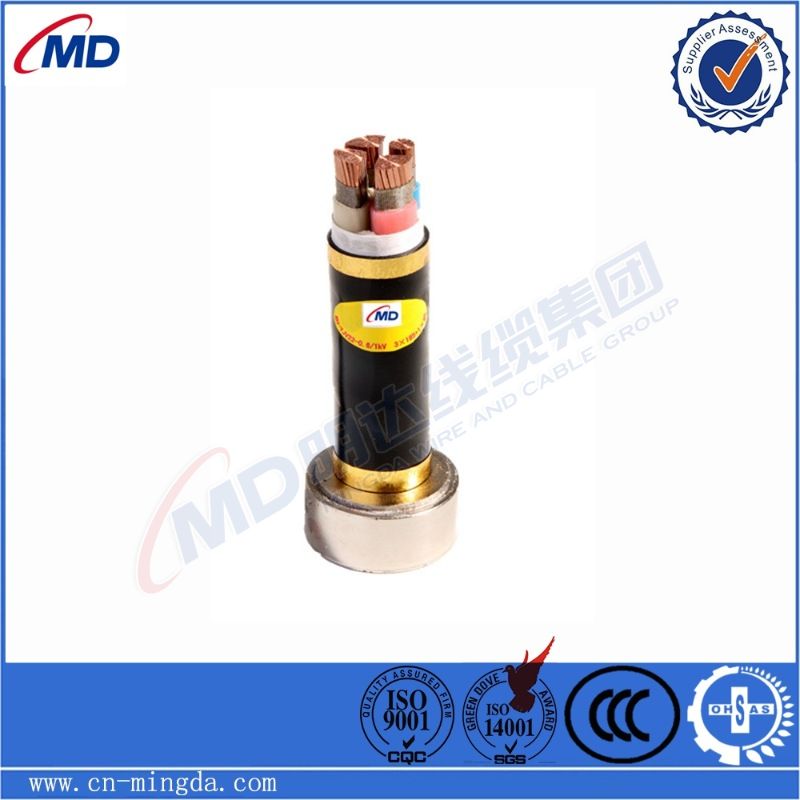
Authoritativeness in the realm of industrial globe valves comes from a deep knowledge of various design types, including Z-body, Y-body, and Angle-body configurations. Each design has unique features that make it suitable for specific applications. The Z-body, for instance, is known for its simplicity and reliability, ideal for general-purpose use. On the other hand, the Y-body and Angle-body designs are optimized for applications requiring straighter flow paths, thus minimizing pressure drop across the valve.
industrial globe valve
Experience also plays a vital role in ensuring the optimal performance of globe valves. Regular maintenance and proper installation are crucial to sustaining their efficiency and longevity. Practitioners recommend routine inspections to check for wear and tear, ensuring that the valve's seating surfaces remain intact and functional. Installing the valve in the correct orientation and adhering to manufacturer specifications during maintenance tasks also enhances reliability.
Trustworthiness stems not only from choosing a reputable manufacturer but also from understanding the certifications and standards that govern industrial globe valve production. Compliance with standards such as the American Society of Mechanical Engineers (ASME) or the International Organization for Standardization (ISO) ensures that the valves meet the stringent quality and safety standards required in industrial applications.
When addressing product categories,
it is essential to consider manual and automated globe valves. Manual valves provide simplicity and cost-effectiveness for systems where manual control is sufficient, while automated valves, equipped with electric, pneumatic, or hydraulic actuators, offer precision and ease of operation in complex or remote systems. Automated valves are particularly beneficial in large-scale operations where process control and efficiency are paramount.
In conclusion, industrial globe valves are integral to ensuring robust and controlled flow within various industries. Selecting the appropriate valve involves a detailed assessment of material composition, design type, and operational requirements. Expert knowledge, combined with regular maintenance and compliance with industry standards, fosters a trustworthy and efficient control system that upholds the integrity of industrial operations.