In the intricate landscape of fluid dynamics within industrial applications, the check valve emerges as a silent sentinel, ensuring unidirectional flow and preventing potentially hazardous backflow. As industries endeavor to optimize their operational efficiency, understanding the pivotal role and advanced functionalities of industrial check valves becomes essential.
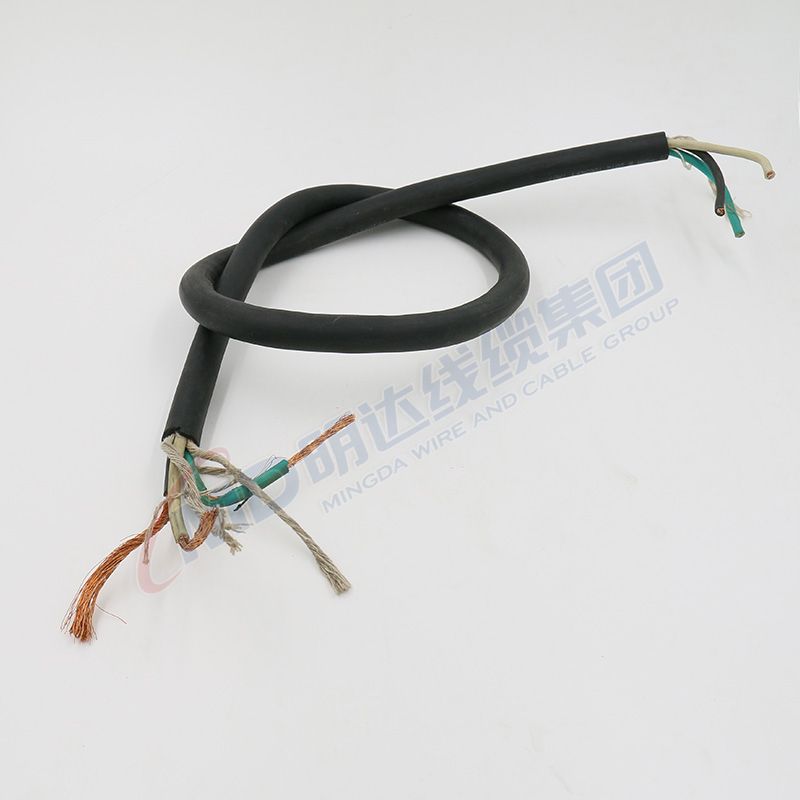
Industrial check valves, though simple in design, are engineered to deliver unparalleled reliability and performance across a multitude of settings. They can be found in sectors ranging from petrochemical and water treatment facilities to power generation plants. These valves are indispensable in systems where the reversal of flow could lead to significant equipment damage or process inefficiencies.
Experience in the field highlights the advantages of utilizing industrial check valves made from robust materials such as stainless steel or high-density polymers. These materials offer exceptional resistance to corrosive elements and extreme temperatures, crucial in maintaining the longevity and efficacy of the valve under strenuous conditions. Engineers and plant operators have discovered through field experience that investing in higher-grade materials, although initially more costly, results in long-term savings through reduced maintenance needs and extended operational life.
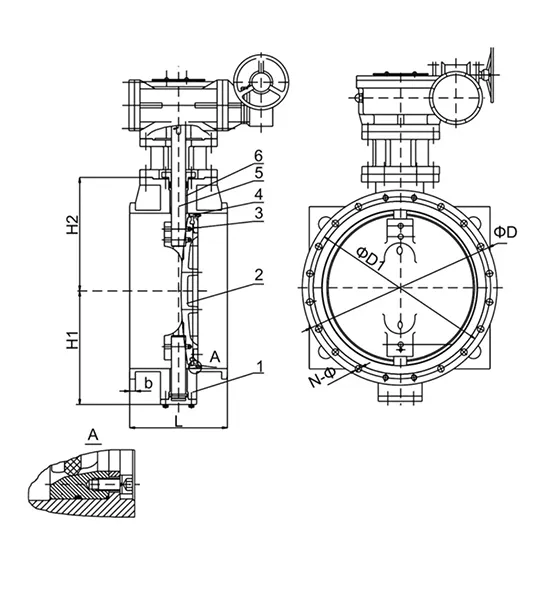
From a technical expertise perspective, the choice of check valve type also plays a critical role in optimizing system performance. Swing check valves, with their simple operational mechanism, are favored in larger diameter pipelines where low-pressure drops are vital. Conversely, axial flow check valves are selected for high-pressure applications due to their streamlined design, which minimizes turbulence and pressure loss. Experts recommend a comprehensive analysis of system requirements and flow characteristics to determine the most suitable valve type.
industrial check valve
An authoritative perspective on industrial check valves underscores the importance of leveraging advancements in valve technologies. Recent innovations include the integration of smart sensors that offer real-time monitoring of valve performance, enabling predictive maintenance and reducing downtime. Industry leaders advocate for these technological enhancements, emphasizing the cost-effectiveness of proactive maintenance strategies.
Trustworthiness in the realm of industrial check valves is inherently linked to compliance with international quality standards such as API 594 or ISO 9001. These certifications provide assurance that the products are manufactured under stringent quality controls, ensuring reliability and safety. Industrial entities are advised to partner with manufacturers who prioritize transparency and accountability, providing detailed documentation and support.
In sum, the strategic implementation of industrial check valves is integral to maintaining the integrity and efficiency of flow systems.
As industries progressively lean towards smarter, more sustainable operations, the role of the check valve is becoming increasingly sophisticated. By investing in superior materials, selecting the appropriate valve type, embracing technological advancements, and ensuring compliance with quality standards, businesses can harness the full potential of these vital components. The expertise gained from years of practical application solidifies the check valve's place as a cornerstone in the pursuit of industrial excellence.