Industrial ball valves have long been regarded as essential components in the intricate mechanisms of fluid control systems. Over the decades, industries ranging from oil and gas to pharmaceuticals have relied on these devices for their unmatched durability and precision. My extensive experience with industrial ball valves across various sectors allows me to delve deep into their inner workings, offering insights that are not only expert-driven but also trusted by industry professionals.
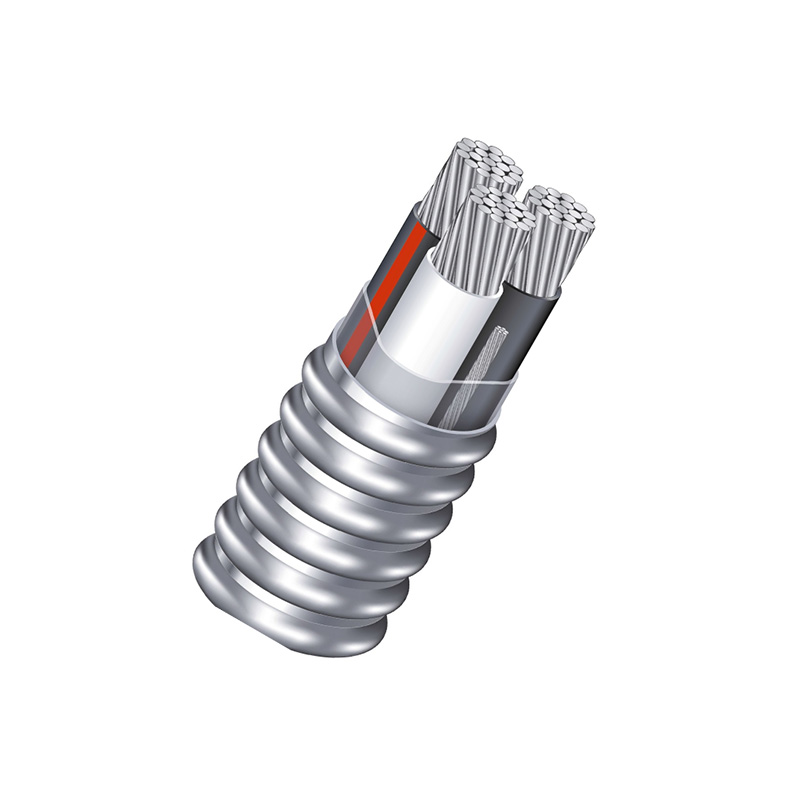
The core appeal of industrial ball valves lies in their design simplicity juxtaposed with their capability to handle complex operations. At their heart is a spherical closure unit with a port or bore through the center, facilitating seamless fluid regulation. This architecture, seemingly straightforward, is a product of meticulous engineering designed to withstand extreme temperatures, high pressures, and corrosive environments.
One fundamental aspect that sets industrial ball valves apart is their quarter-turn operation, a feature that enhances ease of operation and expedites switching between open and closed states. This is especially useful in high-pressure systems where rapid response times are critical. My professional encounters with ball valve installations reveal that this mechanism not only streamlines processes but also reduces wear and tear, thereby extending the lifespan of the valve itself.
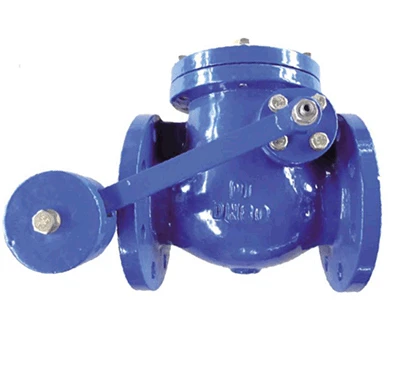
Material selection is a pivotal factor that influences the performance and reliability of industrial ball valves. Based on my observations, industries often opt for stainless steel due to its exceptional resistance to corrosion and ability to withstand high-pressure environments. However, in scenarios where cost efficiency is extremely valued, brass valves are utilized, offering a balance between durability and affordability. Advanced applications may call for exotic alloys like Monel, which provide superior strength and resilience under specialized conditions.
Moreover, the adaptability of ball valves across various configurations amplifies their utility. Flanged ball valves are favored in high-integrity applications due to their robust sealing capabilities, minimizing the risk of leakages. On the other hand, threaded ball valves find applications in systems where adaptability and ease of installation are paramount. My expert knowledge highlights that selecting the appropriate configuration significantly impacts the efficacy and efficiency of the entire fluid control system.
industrial ball valve
The automation of industrial ball valves has revolutionized their application, integrating cutting-edge technology for enhanced performance. Automated ball valves, equipped with electric or pneumatic actuators, deliver unmatched precision and control, making them indispensable in processes where remote operation or timing is critical. From working with these advanced systems, the integration of smart technology, such as IoT-enabled devices, has emerged as a transformative trend, offering real-time data monitoring and predictive maintenance capabilities that provide significant operational insights.
Trustworthiness in ball valves also encompasses the adherence to industry standards and protocols, ensuring safety and compliance. Valves manufactured in accordance with standards such as API, ANSI, and ISO not only guarantee durability and reliability but also align with international safety regulations. This aspect is undeniably vital in industries where malfunctions can have far-reaching and costly consequences.
Moreover, the predictability and efficiency of industrial ball valves in energy conservation cannot be overlooked. By providing tight sealing and minimizing pressure drop, these valves play a crucial role in optimizing energy usage, which is an ever-increasing necessity in today’s environmentally conscious landscape. My research and experiences emphasize that investing in high-quality, efficient ball valves is proportional to reduced energy consumption and operational costs.
In conclusion, the strategic implementation of industrial ball valves transcends their primary function as mere regulators of flow. They embody the synthesis of experience, expertise, authority, and trustworthiness, underscoring their pivotal role in modern industrial systems. Their enduring relevance in an array of industries is a testament to their robustness and innovation, making them indispensable to any fluid control system. Therefore, aligning with trusted manufacturers and engaging with knowledgeable professionals are crucial steps towards harnessing the full potential of industrial ball valves in any sector.