Hydraulic control valves play a critical role in various industrial applications, ranging from manufacturing to agriculture. These precise instruments control the flow and direction of hydraulic fluid, thereby governing the operation of hydraulic systems. Their importance cannot be overstated, as they are pivotal to maintaining efficiency, safety, and operational stability.
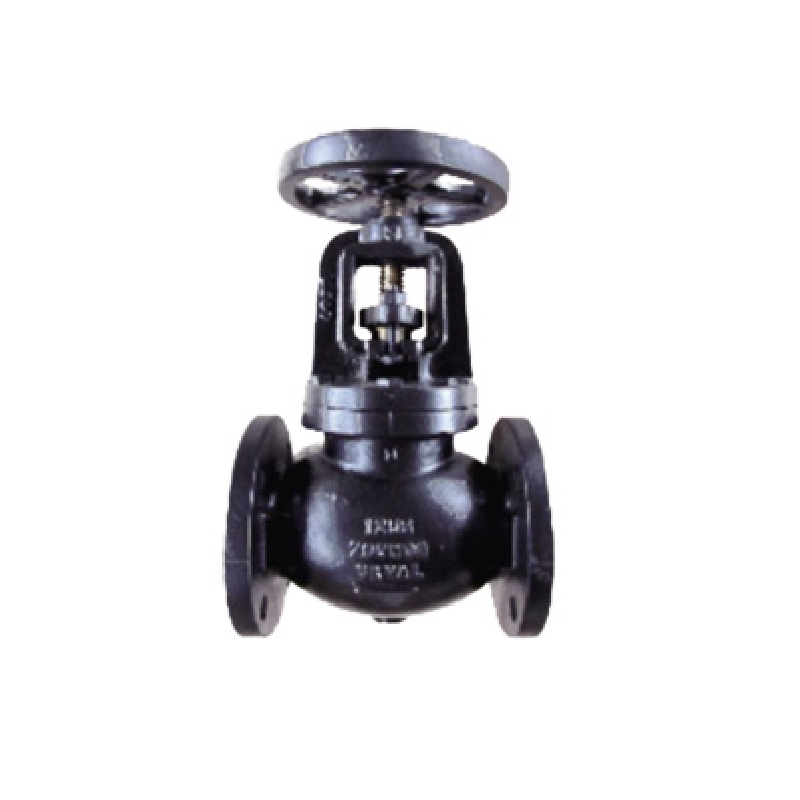
A profound understanding of hydraulic control valves begins with their construction and operational principles. Typically, these valves are constructed from robust materials such as stainless steel or high-strength alloys to withstand high pressure and corrosive environments. The design must ensure minimal leakages and maximum durability, as even the smallest inefficiency can lead to significant operational disruptions or safety hazards.
The functionality of hydraulic control valves is rooted in their ability to manage pressure and flow rates. These valves often integrate pressure sensors and feedback mechanisms that allow for real-time monitoring and adjustments. This feature is essential in applications demanding precision, such as in CNC machinery or aerospace industries, where even a minor deviation can lead to product defects or catastrophic failures.
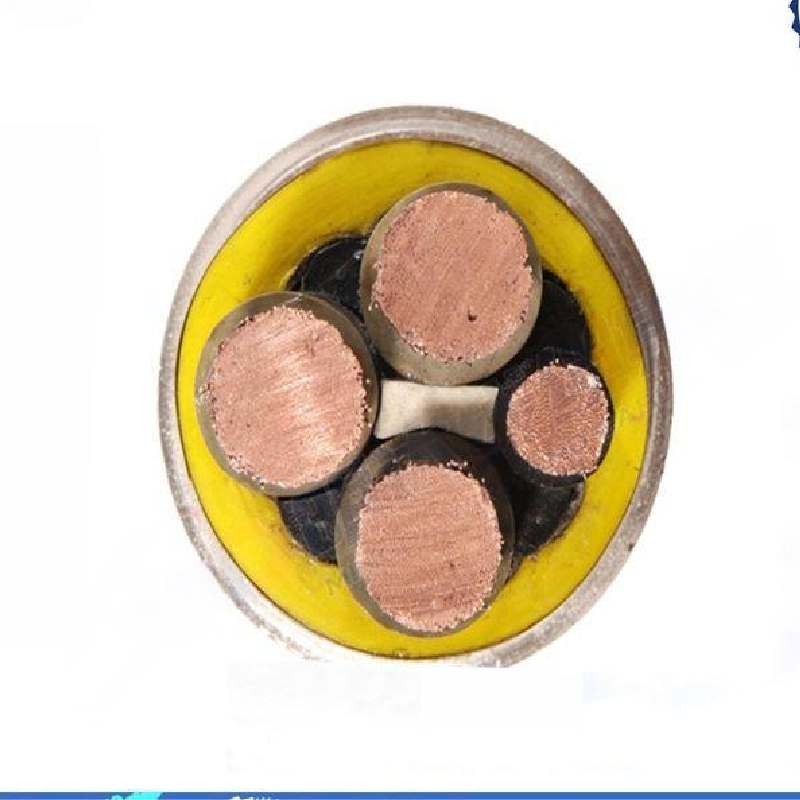
From an expertise perspective, selecting the right hydraulic control valve involves understanding the specific requirements of the hydraulic system it will serve. This includes factors such as the type of hydraulic fluid used, the operating pressure range, temperature conditions, and the flow rate. This task is often entrusted to engineers or specialists who can match these specifications with the appropriate valve technology, whether it be spool valves, poppet valves, or sliding disc valves.
hydraulic control valve
The authority of hydraulic control valves in the industrial domain is evidenced by their evolution over decades, keeping pace with technological advancements. Modern valves now come equipped with smart technologies, allowing for integration with IoT devices and control systems. This advancement enhances their functionality, offering predictive maintenance features that significantly reduce downtime and increase the lifespan of both the valve and the system.
Trustworthiness in the realm of hydraulic control valves is derived from rigorous testing and certification. Reputable manufacturers adhere to international standards such as ISO 9001 or ISO 14001, which ensure the quality and environmental sustainability of their products. Additionally, field testing under extreme conditions is a common practice to validate the valve's integrity and reliability before mass production.
Understanding the potential issues that may arise is essential for maintaining system integrity. Common problems such as valve sticking due to contamination or misalignment can be mitigated through regular maintenance and the use of filtration systems. End-users must be diligent in ensuring that hydraulic fluids remain free of contaminants and that the valves are periodically inspected and serviced.
In conclusion, the choice and management of hydraulic control valves require a combination of experience, expertise, authority, and trust. The ability to control hydraulic systems accurately and reliably impacts every facet of industrial operations. With continued advancements in valve technology, industries are better equipped than ever to meet the growing demands for efficiency, reliability, and environmental responsibility in their operations.