The significance of ductile valves in modern industrial applications cannot be overstated. Ductile valves are integral components in various industries due to their superior strength, flexibility,
and resistance properties. Over the years, these valves have evolved to meet the ever-increasing demands for efficiency and durability across different sectors.
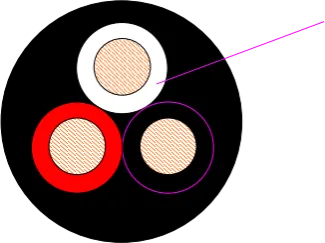
From an engineering perspective, ductile valves are crafted from ductile iron, an alloy known for its superior tensile strength and elasticity compared to traditional cast iron. This material makes the valves more resilient to pressure, corrosion, and temperature variations, which are common in industrial environments. This characteristic ensures operational reliability and longevity, reducing maintenance needs and downtime.
Industrial sectors such as oil and gas, water treatment, and chemical processing frequently rely on ductile valves for their operational needs. In the oil and gas industry, ductile valves withstand high pressures and corrosive environments, ensuring the seamless flow of liquids and gases across pipelines. Similarly, water treatment facilities benefit from their use due to the valves' ability to resist deterioration in the presence of chemicals and microorganisms.
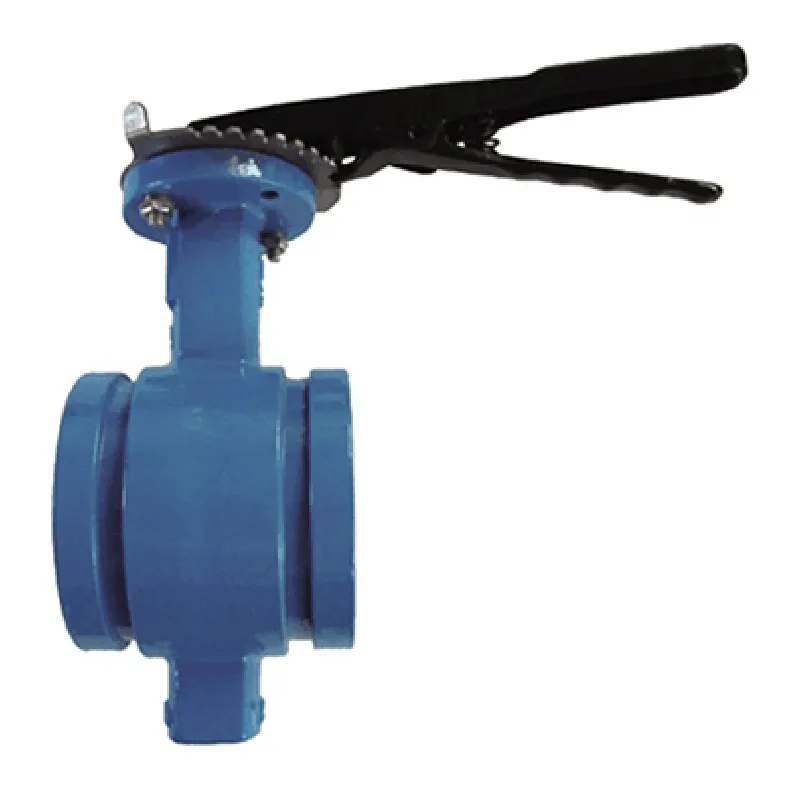
Experts in valve technology affirm that ductile valves offer a perfect blend of flexibility and strength, making them indispensable in scenarios that require durable and adaptable flow control solutions. The ease with which these valves can be installed and maintained further enhances their appeal among industrial operators who need robust yet cost-effective solutions.
Trust in ductile valves is anchored not only on their material properties but also on the technological advancements that have been made in their design and functionality. Modern ductile valves are equipped with sophisticated features like remote operation capabilities, pressure regulation, and automatic actuation. These features enable industries to integrate these valves into automated systems, enhancing process efficiency and safety.
ductile valve
Another critical aspect that underlines the trustworthiness of ductile valves is their compliance with international safety and quality standards. Manufacturers are committed to ensuring that these products meet stringent certification requirements, which provides additional assurance to industries regarding their operational safety and reliability.
A practical example of the efficacy of ductile valves can be observed in a global beverage company's facility where the implementation of these valves resulted in a significant reduction in water loss and maintenance costs over the course of a year. The facility's operations team reported a substantial improvement in their system's performance, attributing it to the robust design and reliability of ductile valves.
From an expert's viewpoint, investing in ductile valves offers industries a strategic advantage. While initial costs might be higher compared to other valve types, the long-term benefits in durability, reduced maintenance, and operational efficiency provide a compelling return on investment. Companies looking to enhance their process systems' efficiency must consider the total lifecycle costs, where ductile valves often emerge as the most sensible choice.
In conclusion, ductile valves exemplify the cutting-edge of material engineering and practical application in industrial settings. Their strength, adaptability, and technological advancements make them a cornerstone in flow control and management. Companies aiming for sustainable and efficient operations should consider ductile valves as a key component in their infrastructure, ensuring that they stay competitive in today's demanding industrial landscape.