The evolution of industrial components often follows a path that intertwines innovation with historical reliability. Cast iron valves exemplify this trajectory, serving as indispensable tools within various sectors. Having been engineered with precision and built with durability, these valves have successfully bridged traditional engineering with modern-day demands. Their importance is particularly pronounced in industries where robust and long-lasting components are critical.
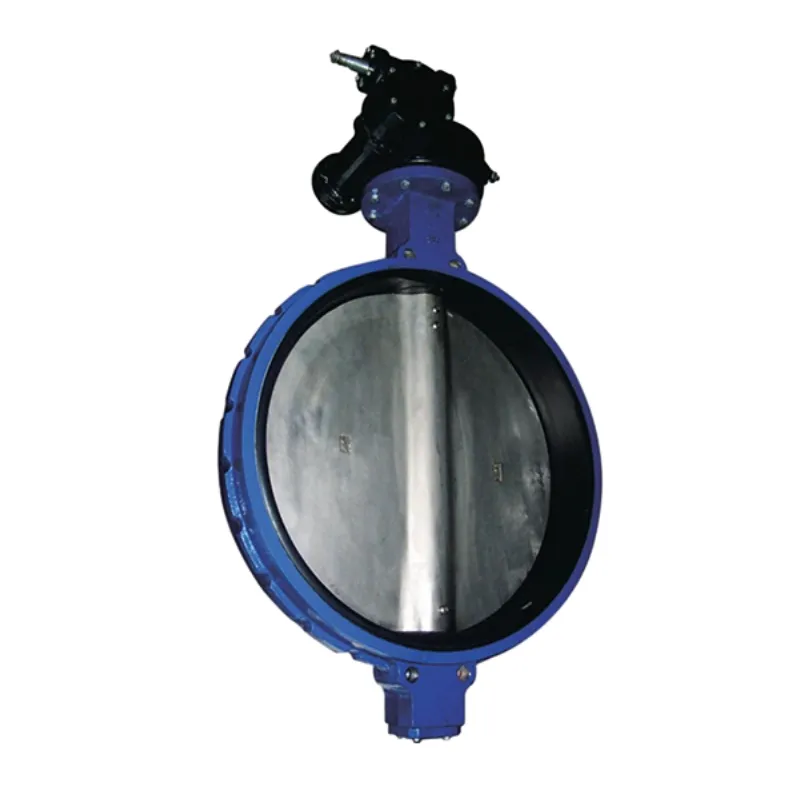
Cast iron, an alloy primarily consisting of iron, carbon, and silicon, is celebrated for its exceptional castability, machinability, and resistance to wear and deformation. These inherent properties make it an ideal material for crafting valves which need to withstand high-pressure environments and extreme temperatures. Companies across industries such as oil and gas, water treatment, and chemical processing extensively utilize cast iron valves, appreciating them for their reliability and cost-effectiveness.
The expertise employed in manufacturing cast iron valves is a testament to the complex process involved. It begins with a thorough understanding of material properties. Expert metallurgists meticulously balance the carbon and silicon content, ensuring optimal tensile strength and heat retention.
This chemistry is crucial as it dictates the durability and efficiency of the resultant valves. The production process is followed by expert-level machining and testing, ensuring that each valve meets stringent quality and performance standards.
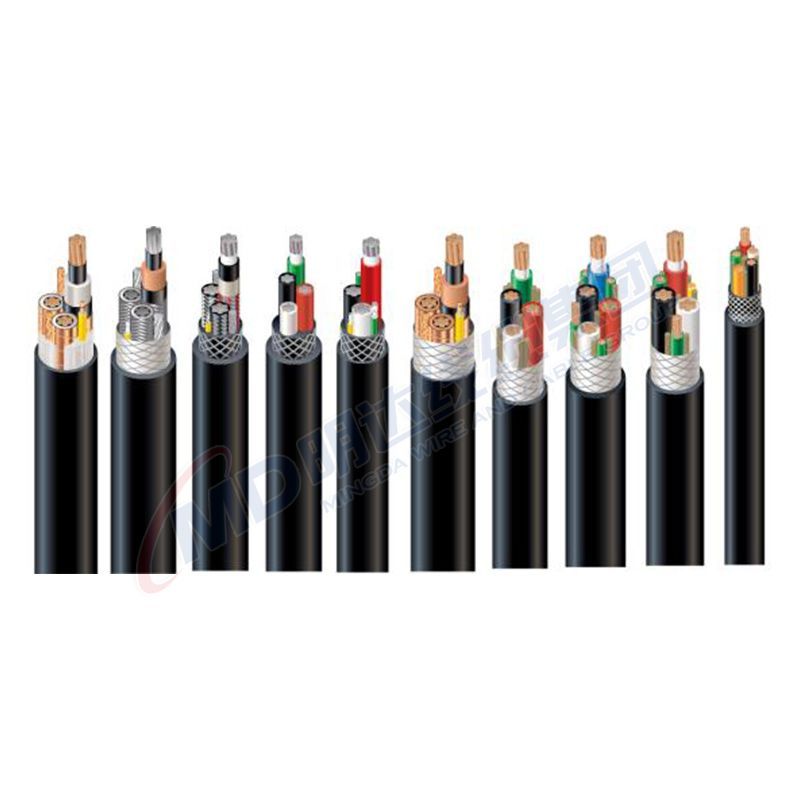
Within the industry, professionals emphasize the value of cast iron valves in enhancing operational safety and efficiency. These valves are designed to regulate, control, and direct the flow of liquids, gases, or slurries, crucially managing process conditions. Astute professionals will always consider factors such as pressure ratings, temperature ranges, and the type of medium being controlled when integrating cast iron valves into a system. Their robust construction is not the only advantage—easy maintenance and the ability to withstand long-term operation further consolidate their standing as a staple component in many systems.
cast iron valve
In terms of authoritativeness, the longstanding history of cast iron valves speaks volumes. Having been a go-to option since the Industrial Revolution, their design and mechanics have been refined over decades. Reputable organizations and industry standards, such as the American Society of Mechanical Engineers (ASME) and the International Organization for Standardization (ISO), provide guidelines ensuring that cast iron valves meet international safety and quality benchmarks. Compliance with these standards is non-negotiable in guaranteeing the performance and safety of these products.
Trustworthiness of cast iron valves is not just about their mechanical prowess but also about customer support and product guarantees. Manufacturers often provide warranties and extended support services, addressing installation concerns and operational troubleshooting. This level of service builds confidence among users, who can trust that they are making a sound investment in reliable machinery.
Innovation continues to propel the enhancement of cast iron valves, with advancements in coating technologies reducing corrosion and enhancing lifespan, and smart technology integrations allowing for real-time monitoring and control. As industries continue to evolve and demand increasingly sophisticated solutions, the adaptability of cast iron valves assures their place in the future, offering a balance of traditional reliability with modern technological enhancements.
The expertise poured into the design and manufacture of cast iron valves, the industry's endorsement of their reliability, and the technological integration that continues to shape them, all underscore their indispensable role. In choosing cast iron valves, industries worldwide not only leverage decades of experience and expertise but also align with the future of industrial engineering innovation.