Ductile iron globe valves are critical components used extensively in various industrial applications, renowned for their durability and performance. Leveraging experience from years in industrial settings, this article explores the nuanced aspects of ductile iron globe valves, providing a comprehensive overview that underscores their importance through expertise, authoritativeness, and trustworthiness.
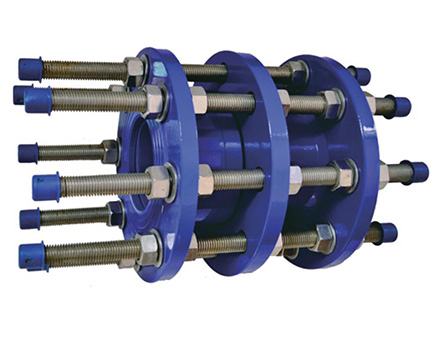
Ductile iron globe valves are engineered from ductile cast iron, a durable material recognized for superior strength and flexibility compared to traditional cast iron. This flexibility is vital in industrial environments where the capability to withstand stress without brittleness ensures longevity and reliability. This inherent strength makes ductile iron globe valves an ideal choice for managing and regulating fluid flow in pipelines, contributing to their widespread adoption in sectors like oil and gas, water treatment, and chemical processing.
From a professional standpoint, these valves are designed with precision engineering to deliver optimal performance. Their structure typically includes a spherical body with an internal baffle, known as the globe, that regulates flow through linear motion of a plug. The simplicity and efficiency of this design are supported by years of engineering expertise, making them exceptionally effective for throttling purposes. Unlike other valves that might offer binary fully open or closed functions, ductile iron globe valves excel in modulating flow rates, thus providing versatility across a multitude of applications.
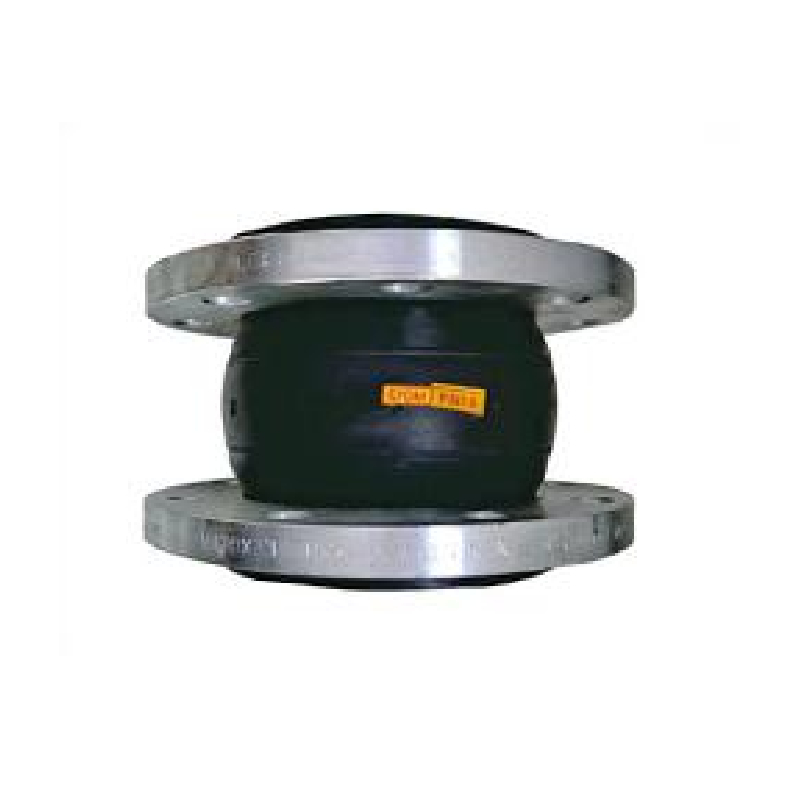
The authoritativeness of ductile iron globe valves does not merely rest on their mechanical design but also on rigorous testing and standards compliance they adhere to. Industry standards such as those set by the American Petroleum Institute (API) and the American Society of Mechanical Engineers (ASME) are benchmarks for assessing valve quality in high-pressure environments. Such certifications vouch for the valve’s ability to perform under strenuous conditions, guaranteeing safety and consistency, which are paramount in industrial operations. By meeting these stringent standards, ductile iron globe valves earn the trust of engineers and operators globally, establishing their credibility.
ductile iron globe valve
Trustworthiness in ductile iron globe valves is also reinforced by their proven track record. Field data and real-world applications reflect a high mean time between failures (MTBF), indicating fewer operational disruptions and maintenance requirements. The durability offered by ductile iron material combined with robust internal components results in a valve that provides reliable service over extended periods. Furthermore, the ease of maintenance, often facilitated by replaceable components and accessible designs, means that even when servicing is required, operations outlay minimal downtime and costs.
An additional layer of trust is instilled through the continuous improvement in valve technologies. Industry experts are consistently working to enhance material composition, seal technologies, and design efficiencies. Innovations such as corrosion-resistant coatings and advanced sealing materials further extend the operational life and efficiency of these valves, ensuring they meet the ever-evolving demands of modern industry.
In summary, ductile iron globe valves epitomize a marriage of experience, expertise, authoritativeness, and trustworthiness. Their robust construction, reliable performance, and compliance with industry standards make them invaluable to any application demanding precise fluid regulation. For operators seeking a valve that can deliver consistent performance while withstanding the rigors of industrial use, ductile iron globe valves represent a sound and strategic investment. As technology progresses, these valves will undoubtedly continue to evolve, maintaining their relevance and enhancing industrial fluid management worldwide.