When addressing the concept of dismantling joint in mechanical or structural engineering, it's critical to dive into a comprehensive exploration of the process that involves a blend of physical expertise, specialized tools, and adherence to safety standards. Here, we delve into the intricacies and best practices, ensuring that your approach to dismantling joints is both effective and innovative.
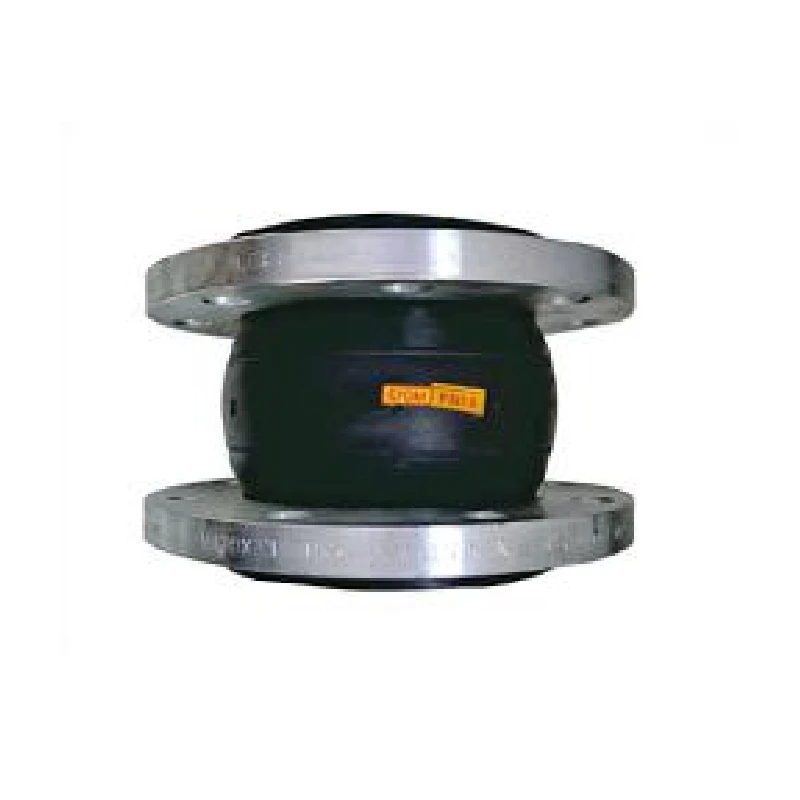
Dismantling joints, crucial components in various industrial applications, are central to assembling and disassembling structures without damage. The integrity of these joints directly impacts the longevity and functionality of machinery or frameworks. Throughout this detailed analysis, we will focus on the experiential insights and technical expertise necessary for optimizing dismantling joint procedures, promoting both efficiency and safety.
At the heart of successful dismantling processes lies an in-depth understanding of the joint types involved. Mechanical joints such as bolted, welded, or riveted connections demand distinct methods. For bolted connections, precision tools such as torque wrenches are indispensable in ensuring the safe loosening and tightening of nuts and bolts. It is crucial to follow a cross-pattern sequence to maintain balance and prevent a concentration of stress which might lead to component distortion.
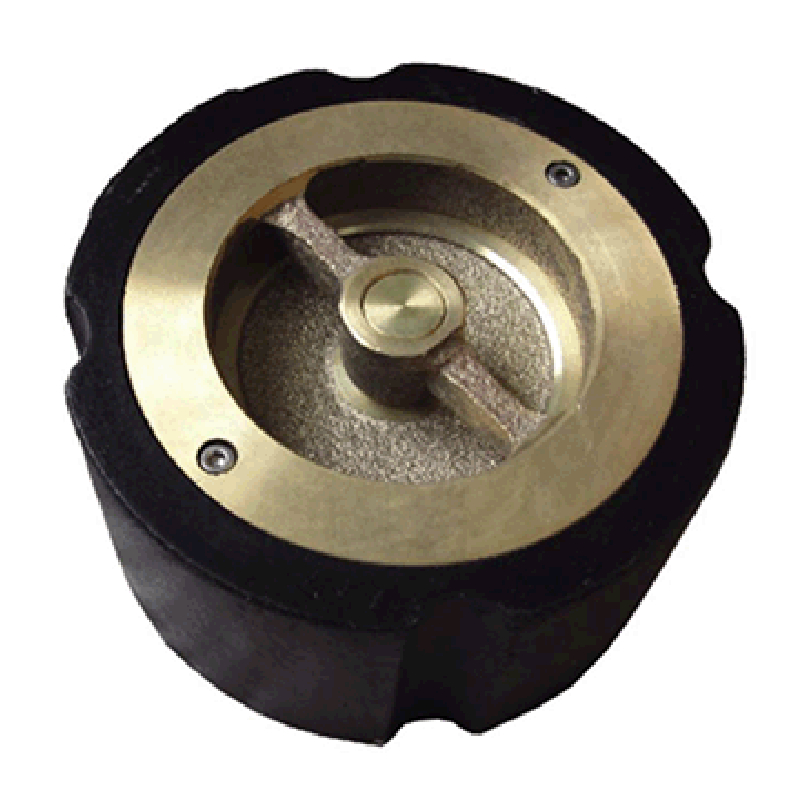
In welded joints, it's essential to apply advanced dismantling techniques, like hot-cutting or mechanical grinding, under stringent supervision. Here, the expertise of a certified welder comes into play, as incorrect procedures can compromise structural integrity, leading to potential hazards. For riveted joints, employing the correct rotary tools to drill out rivets without damaging surrounding materials underscores the need for skilled workmanship.
dismantling joint
From an engineering standpoint, the ever-evolving technology in Modelling and Simulation (M&S) significantly enhances the dismantling process. Using computerized models to simulate the dismantling of a joint allows engineers to anticipate potential challenges and devise strategies to mitigate them. This proactive approach not only saves time but also minimizes resource utilization and reduces the risk of failure.
Safety cannot be overstressed in the dismantling joint process. Minimizing risks requires a multi-disciplinary approach, combining the expertise of engineers, safety inspectors, and skilled laborers. Routine training and compliance with Occupational Safety and Health Administration (OSHA) standards ensure that operations are conducted without incidents. Furthermore, the use of personal protective equipment (PPE) and regular equipment inspections are non-negotiable aspects of an effective safety regime.
Finally, fostering an environment of trustworthiness and reliability within the dismantling industry is achieved by consistently meeting, if not exceeding, client expectations through transparent communication and accountability. This encompasses timely updates on project progression and responsiveness to client inquiries.
In exploring dismantling joint processes, the goal is not just to deconstruct but to do so with a profound sense of responsibility and professionalism. By integrating experiential learning, cutting-edge technologies, and stringent safety protocols, one can ensure the dismantling of joints is executed flawlessly. This positions you as an authority within your field, earning the trust and respect of peers and clients alike while maintaining a pioneering stand on contemporary engineering challenges.