In the intricate world of industrial systems, control valves stand as indispensable components that regulate the flow of fluid—liquids, gases, and slurries—within a system. This article aims to demystify control valves, offering insights into their importance, the expertise required for their application, and the authoritative guidelines ensuring their reliability and trustworthiness in various industries.
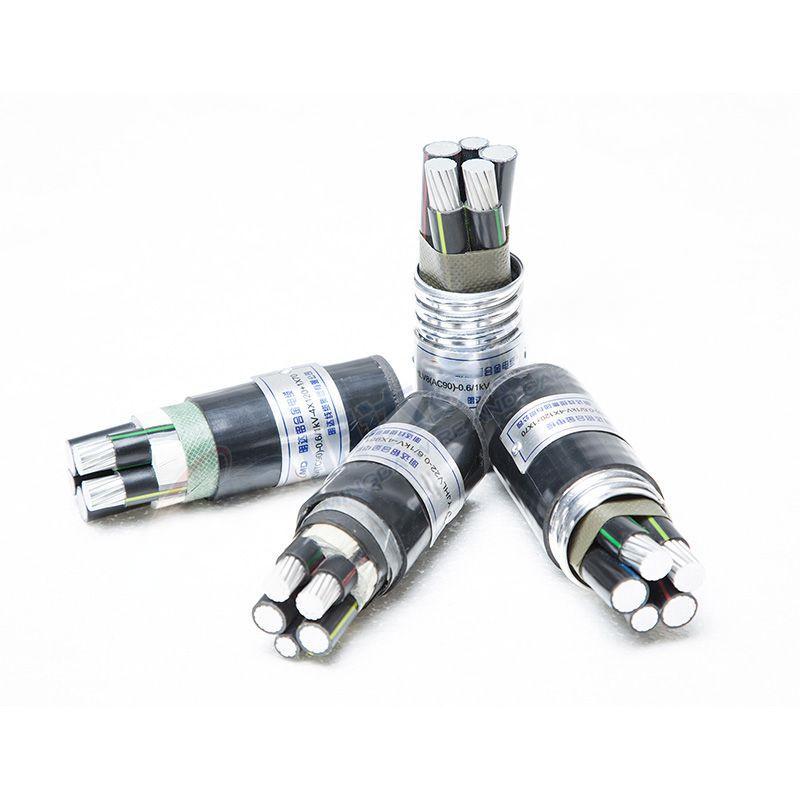
Control valves are vital in adjusting the pressure, temperature, and liquid levels by influencing the media flow rate. These adjustments are critical in industries such as oil and gas, water treatment, power generation, and chemical processing, where precise control of fluid dynamics is paramount. This expert maneuvering ensures system efficiency and safety, preventing leaks and ensuring smooth operation.
Selecting the right type of control valve is crucial. The options include globe valves,
butterfly valves, ball valves, plug valves, and diaphragm valves. Each of these valves offers different advantages and disadvantages, deeply rooted in their design and intended application. Globe valves, known for their precision, are often preferred in throttling services, while butterfly valves are valued for their cost-effectiveness and efficiency in large volume applications. Expertise in understanding the compatibility of these valve types with specific industrial requirements is essential for system optimization.
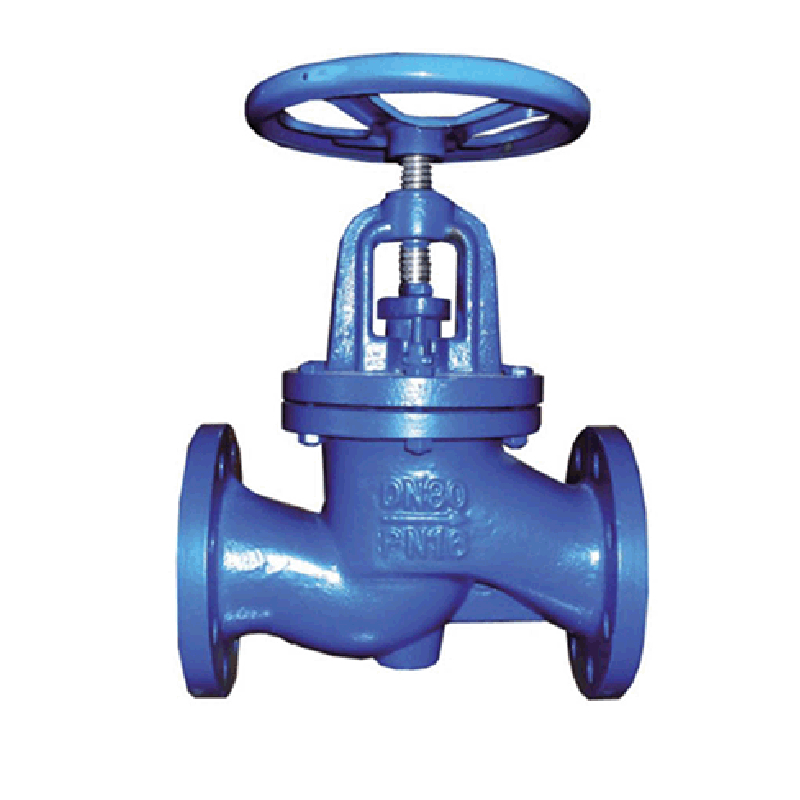
Trustworthiness in control valves is achieved by adhering to international standards such as those provided by ISO and ANSI. These standards guide manufacturers in producing valves that withstand high pressure and extreme temperatures, maintaining integrity under strenuous conditions. Manufacturers with certifications adhering to such standards are recognized for their authority and reliability in producing high-quality control valves.
control valve
Furthermore, experience in installation and maintenance is indispensable for ensuring the longevity and optimal performance of control valves. Professionals responsible for these tasks must be adept in implementing predictive maintenance techniques. These techniques often include regular inspections, ultrasonic testing, and thermal imaging—processes that predict potential failures and enhance the valve's operational lifespan.
In today's digital era, innovations in control valve technology have introduced smart valve solutions equipped with sensors for real-time diagnostics and automated adjustments. These intelligent systems enhance the efficiency of entire operations, allowing for quick responses to dynamic conditions. Expertise in integrating such technology into existing systems is increasingly becoming a benchmark for industrial leaders.
Understanding control valves involves comprehending their engineering design, material selection, and the operational pressures they can withstand. Such knowledge is crucial for anyone aiming to harness the full potential of these devices within complex systems.
In conclusion, control valves are more than simple components in an industrial setup; they are pivotal in maintaining the balance and functionality of the entire operation. The expertise required in selecting, applying, and maintaining these valves is matched by the need for authoritative standards ensuring their effectiveness and reliability. Trust in their performance is built on a foundation of experience, knowledge, and adherence to best practices, making control valves a critical element in the success of industrial applications worldwide.