Control valves are pivotal in a wide array of industries, from petrochemical to food processing, ensuring precise regulation of fluid flow, temperature, and pressure. Understanding their essential role and choosing the right one can significantly impact operational efficiency and reliability. As an experienced engineer and industry consultant, I've seen firsthand how the proper selection and maintenance of control valves can lead to increased operational resilience and cost savings.
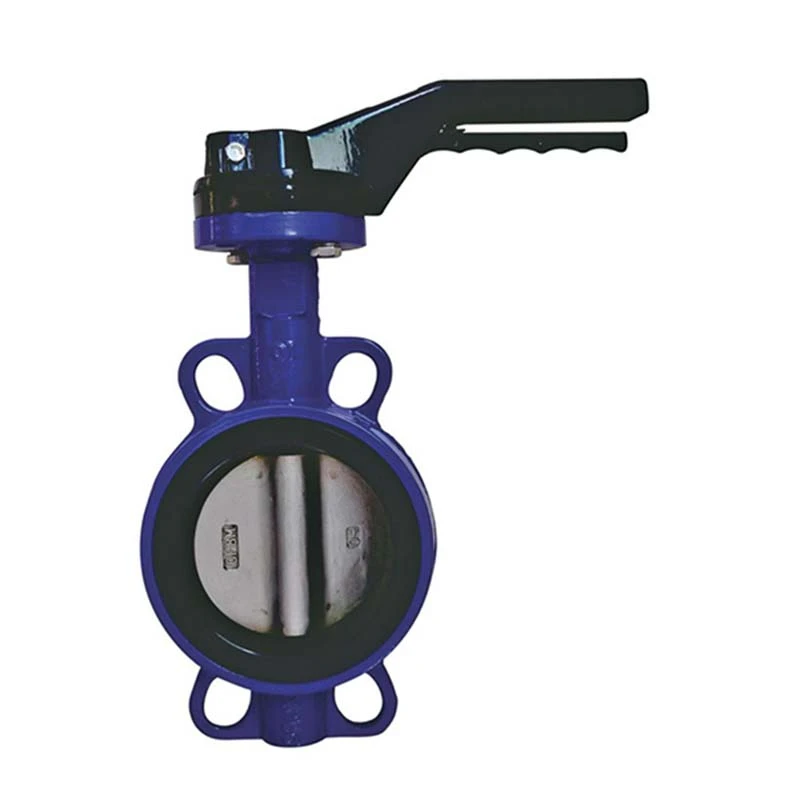
A control valve's primary function is to alter the flow of liquids or gases by varying the size of the flow passage as directed by a signal from a controller. These sophisticated devices are indispensable in process control industries where minute adjustments can have substantial outcomes. Selecting the right control valve requires a deep understanding of the operational environment, including the nature of the fluid, temperature, and pressure conditions.
Precision is a hallmark of effective control valves. High-standard manufacturing processes and materials are essential. For instance, valves constructed from stainless steel or durable polymers resist corrosion, thus ensuring longevity and reliability in harsh environments. The expert craftsmanship involved in producing these valves guarantees that they maintain their integrity under diverse conditions, which is crucial for minimizing downtime and maintaining safety standards.
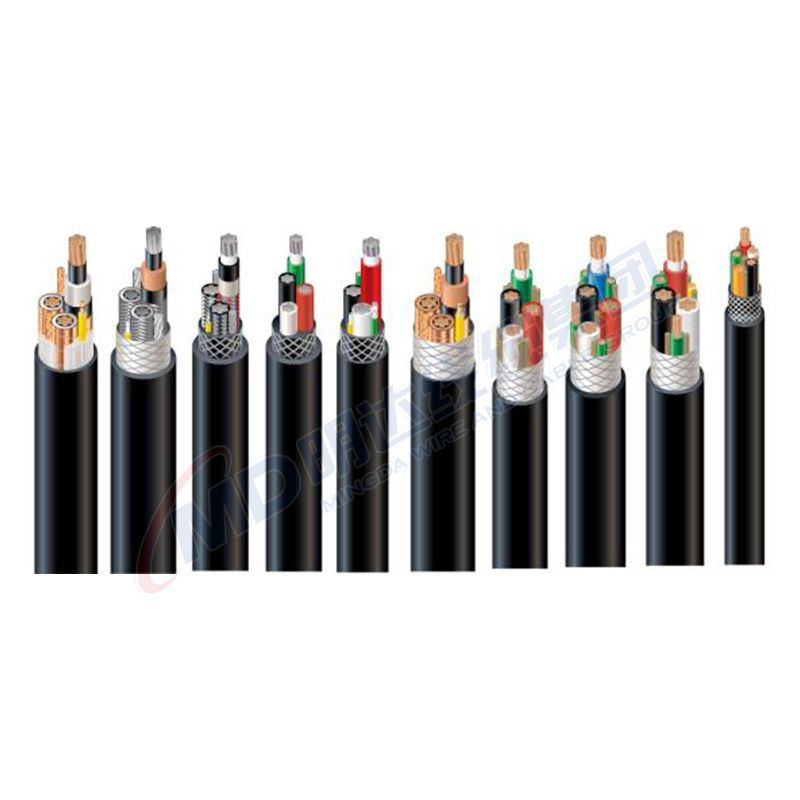
The adaptability of modern control valves comes from their ability to integrate with advanced automation systems. Smart control valves equipped with digital positioners provide real-time feedback, enabling operators to monitor and adjust settings remotely. This integration allows for predictive maintenance, reducing unexpected failures and optimizing operational efficiency. It is these technological innovations that distinguish leading manufacturers in the control valve industry.
Choosing a control valve also involves consideration of the type of actuator used. Pneumatic actuators are common due to their reliability and ease of use in many applications, offering excellent precision and durability. However, in applications where precise positioning is required, electric actuators might be preferred due to their ability to deliver exact positioning and rapid response times.
control valve
Beyond selecting the appropriate valve type and materials, regular maintenance schedules are imperative for ensuring peak performance. An effective maintenance program includes routine inspections, cleaning, and testing to detect early signs of wear or potential failure. This proactive approach can prevent costly repairs and extend the life span of the valve, promoting a culture of safety and efficiency.
In addition to operational factors, compliance with international standards is crucial. Control valves should adhere to relevant industry standards such as ANSI, ISO, or API to ensure they meet safety and performance expectations. These standards are set by authorities with substantial expertise, guaranteeing that products are robust, reliable, and apt for their intended use.
From an expertise perspective, the selection and maintenance of control valves should be managed by professionals with a comprehensive understanding of fluid dynamics and process control systems. Training programs for engineers and technicians should include hands-on experience and theoretical knowledge to instill a level of expertise that matches industry demands. Organizations that prioritize continuous professional development tend to have lower incidents of operational failures.
Control valves serve as a testament to the significant improvements in safety, efficiency, and reliability across industrial processes. Choosing a high-quality control valve and maintaining it effectively is an investment that pays off in enhanced performance, reduced downtime, and substantial cost savings over time. By consulting with industry experts and leveraging the latest technological advancements, businesses can ensure their operations remain competitive and sustainable.
In summary, control valves are more than just components in a system; they are crucial elements that safeguard the continuity and efficiency of industrial processes. As we advance towards more sophisticated and automated systems, the role of expert knowledge and experience in managing control valves becomes increasingly significant. It is through emboldening this foundation of expertise and authoritative practices that industries can harness the full potential of control valves, thus ensuring their operations are at the cutting edge of efficiency and efficacy.