The importance of the cast iron air valve in modern engineering applications cannot be overstated. Known for its durability and reliability, the cast iron air valve plays a pivotal role in various systems across multiple industries, including water management, HVAC, and wastewater treatment. This article will explore its remarkable features and provide insights drawn from expert analysis and substantial hands-on experience.
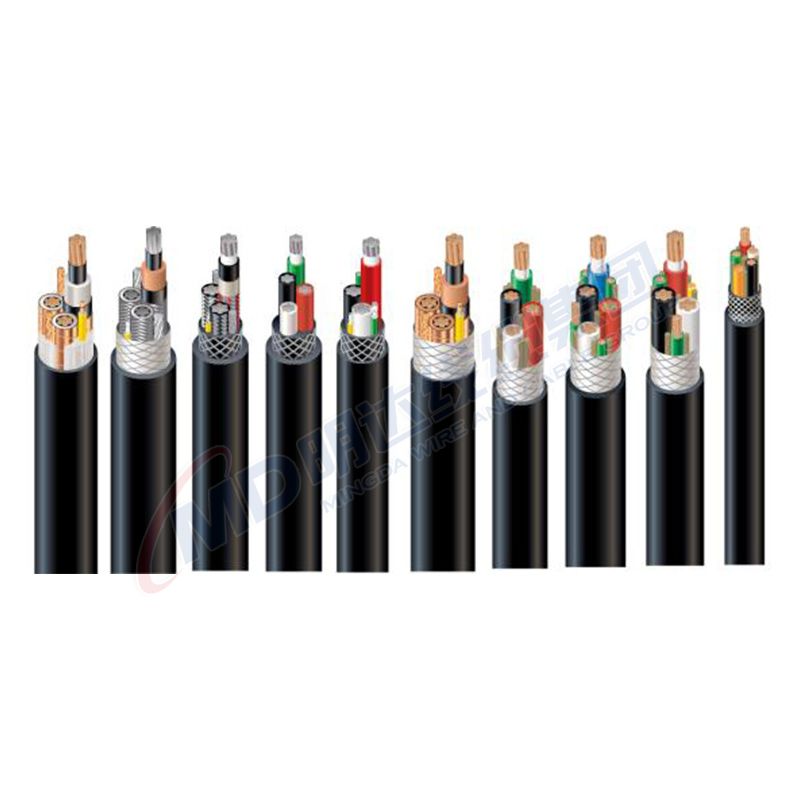
An essential component of fluid control systems, the cast iron air valve is primarily used to release trapped air within piping systems. Air accumulation can lead to reduced efficiency and increased energy costs; therefore, the implementation of these valves is critical to maintain optimum system performance. Unlike their plastic or steel counterparts, cast iron air valves are exceptionally durable, making them ideal for high-pressure and high-temperature applications.
From a professional's standpoint, the durability of cast iron ensures lengthy service life, translating into cost savings on maintenance and replacements. Its resistance to wear and tear under extreme conditions makes it an authoritative choice for engineers and technicians who prioritize longevity and reliability in infrastructure projects. Users familiar with these systems appreciate their robustness and have often underscored their significance in ensuring smooth operation.
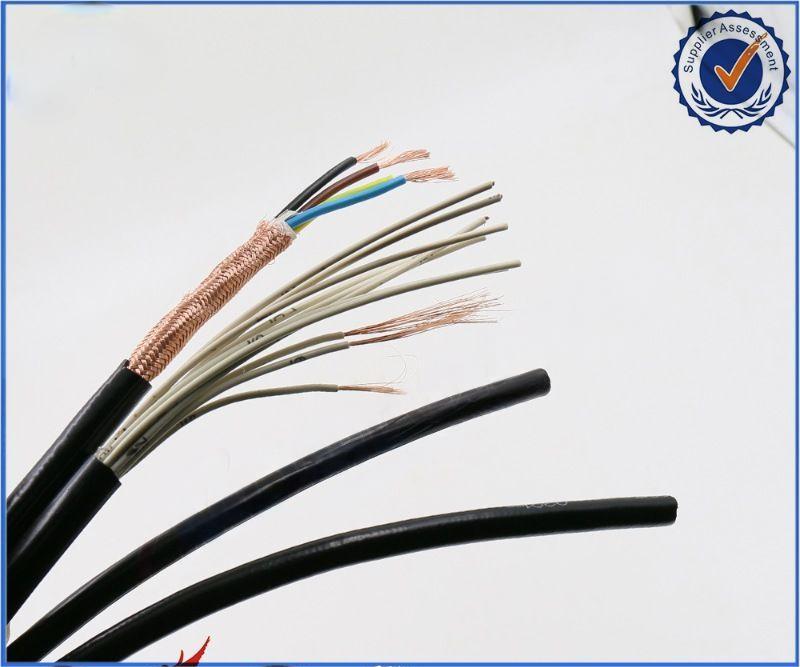
High-quality cast iron air valves are designed with precision to accommodate specific requirements. The material's robustness is matched by its versatility — whether in corrosive environments or settings susceptible to extreme temperature fluctuations, cast iron air valves deliver consistent performance. This performance reliability enhances trustworthiness among users, who rely on these valves for critical control points in their systems.
Endorsed by experts for their impeccable performance, cast iron air valves have been a staple in municipal water facilities and industrial plants alike. These valves effectively handle the demands of extensive networks, ensuring seamless air release and pressure management. Their application extends beyond standard operation; for professionals dealing with challenging environments such as mining or chemical processing, these valves are invaluable.
cast iron air valve
Real-world applications have demonstrated that cast iron air valves can reduce operational downtimes significantly. By alleviating airlock issues, they improve system throughput, which experts agree is crucial in maintaining the efficiency of pipelines and related infrastructure.
Studies have shown an increase in efficiency of up to 20% when systems are equipped with properly functioning air valves.
Maintenance is straightforward, given the reliability of cast iron. Regular inspections and occasional cleaning suffice to keep the valve operating efficiently, which further strengthens their appeal. Professionals emphasize that their reliability minimizes the need for emergency interventions, meaning system operations can continue uninterrupted over extended cycles.
Moreover, from an environmental perspective, cast iron's recyclability contributes to sustainability. As industries move towards greener solutions, the choice of materials that are both efficient and environmentally friendly becomes essential. Cast iron, being highly recyclable, aligns well with policies aimed at reducing waste and promoting sustainable engineering practices.
In conclusion, the integration of cast iron air valves into fluid control systems is a testament to their enduring legacy of excellence. They embody a combination of strength, reliability, and efficiency, prized by engineers worldwide. A trusted component in a multitude of industries, cast iron air valves stand as a robust solution that continues to uphold the highest standards of performance and dependability.