Butterfly valves are an essential component in various industries, known for their efficiency, reliability, and cost-effectiveness. These valves are crucial in regulating fluid flow and are widely used in systems that require quick shut-off and minimal energy consumption. With their unique design and functionality, butterfly valves are employed across various sectors, including water treatment, chemical processing, and food industries.

From an experienced perspective, the allure of butterfly valves lies in their simple mechanism and robust performance. These valves consist of a disk mounted on a rotating shaft. When the valve is closed, the disk is turned perpendicular to the flow direction, thereby blocking the flow. Conversely, when opened, the disk is parallel to the flow, allowing fluid to pass through. This simplicity in design translates to fewer components, which minimizes maintenance needs and reduces the risk of failure.
Professional insights suggest that selecting the appropriate butterfly valve is a critical step in ensuring optimal system performance. Expertise in this field emphasizes the importance of material selection based on the fluid characteristics and operating conditions. For instance, while cast iron and stainless steel are common materials due to their durability and corrosion resistance, other materials like PVC or plastic may be preferable for systems involving corrosive chemicals. The type of material chosen not only affects the valve's longevity but also its efficiency and safety within the system.
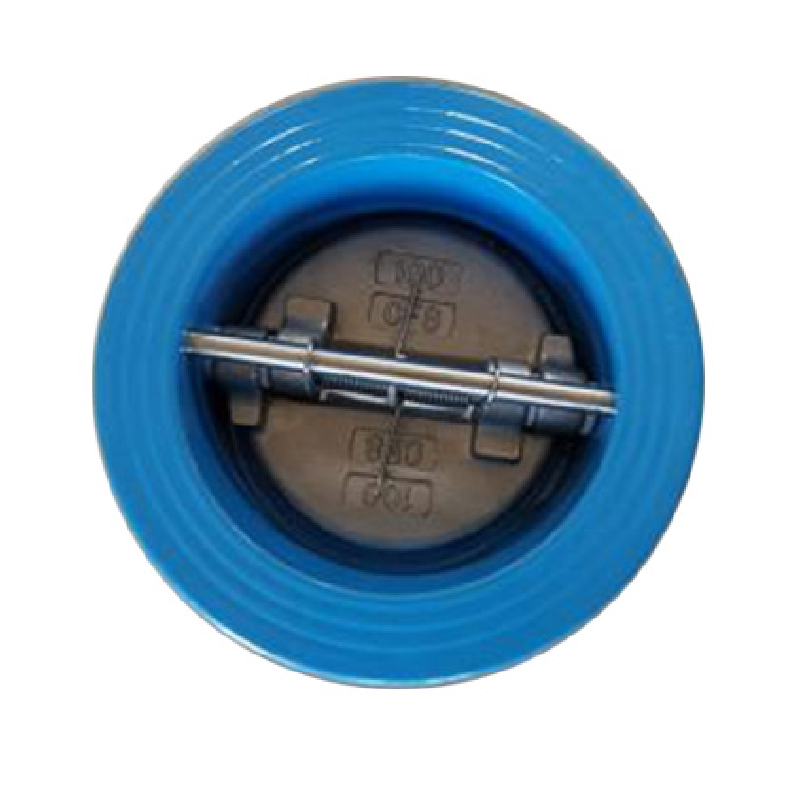
Industry authority recognizes butterfly valves for their versatility. These valves come in various types, such as concentric, double-eccentric, and triple-eccentric designs, each serving specific applications. Concentric butterfly valves, also known as resilient seated, are commonly used in low-pressure applications, offering a cost-effective solution with their simple yet effective design. In contrast, double-eccentric and triple-eccentric models are better suited for higher pressure systems, providing enhanced sealing capabilities and reduced wear on the disk and seat.
butterfly valve
Trust in butterfly valves is further cemented by their minimal environmental impact and resource efficiency. Their design allows for a compact, lightweight solution that requires less material to produce compared to other valve types. Additionally, the quick operation feature contributes to energy savings, particularly in systems where frequent opening and closing are necessary. This energy efficiency aligns with the growing focus on sustainable industrial practices.
For anyone considering the integration of butterfly valves into their operational framework, it is vital to understand the specific needs of their system. Seeking advice from experts and consulting with manufacturers can provide insights into the best type, material, and design for their particular application. Moreover, investing in quality products from reputable manufacturers ensures reliability and long-term performance, fostering trust in these critical components.
In reality, the longevity and reliability of butterfly valves also depend on proper installation and regular maintenance. Ensuring that the valves are installed correctly, aligned properly, and inspected routinely can prevent issues like leakage and wear that compromise system integrity. Maintenance routines should include regular checks for alignment, cleaning of components, and timely replacement of seals and bearings to maintain peak operational efficiency.
In conclusion, butterfly valves are a valuable asset in flow control solutions, offering a blend of simplicity, efficiency, and adaptability. Their role in modern industrial applications underscores their importance, and with the right expertise, they can provide reliable and sustainable performance. Prioritizing high-quality materials, appropriate type selection, and diligent maintenance not only maximizes the benefits of butterfly valves but also reinforces their status as a trusted component in fluid regulation systems.