Butterfly valves, often overshadowed by their more complex counterparts, are powerful components in industries ranging from water treatment to oil and gas. These valves excel in applications where space conservation, versatile pressure ratings, and efficient fluid flow are crucial. Integrating butterfly valves into your system requires not only an understanding of their mechanical dynamics but also a nuanced appreciation of their operational expertise, authoritative references, and construction trustworthiness.
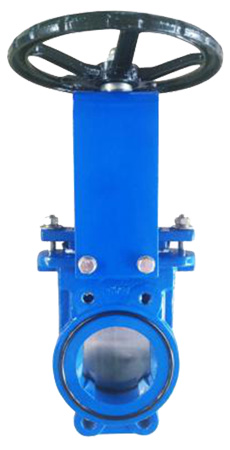
Experience demonstrates that butterfly valves are indispensable due to their simple structure and operational flexibility. Made versatile by their quarter-turn rotational movement, these valves allow precise flow control with minimal pressure drop. Field operators often commend their lightweight design, reducing the load on piping systems and supporting frameworks.
This intrinsic benefit translates to lower installation costs and maintenance overheads. From municipal water systems to industrial agriculture, butterfly valves provide a reliable solution that operators can depend on over extended periods.
In the realm of expertise, butterfly valves exhibit a remarkable adaptability. They are available in various configurations, including wafer, lug, and double flange types, each designed to meet specific demands in industrial applications. The choice of disc material—ranging from stainless steel to hard chromium—is critical, influencing the valve’s compatibility with different media and resistance to wear and corrosion. Engineers stress the importance of selecting a valve with the appropriate seat material, such as EPDM or PTFE, for optimal sealing efficiency and durability. Their straightforward design not only facilitates easy installation and operational training but also simplifies troubleshooting and repairs, making them a hot favorite among maintenance teams.
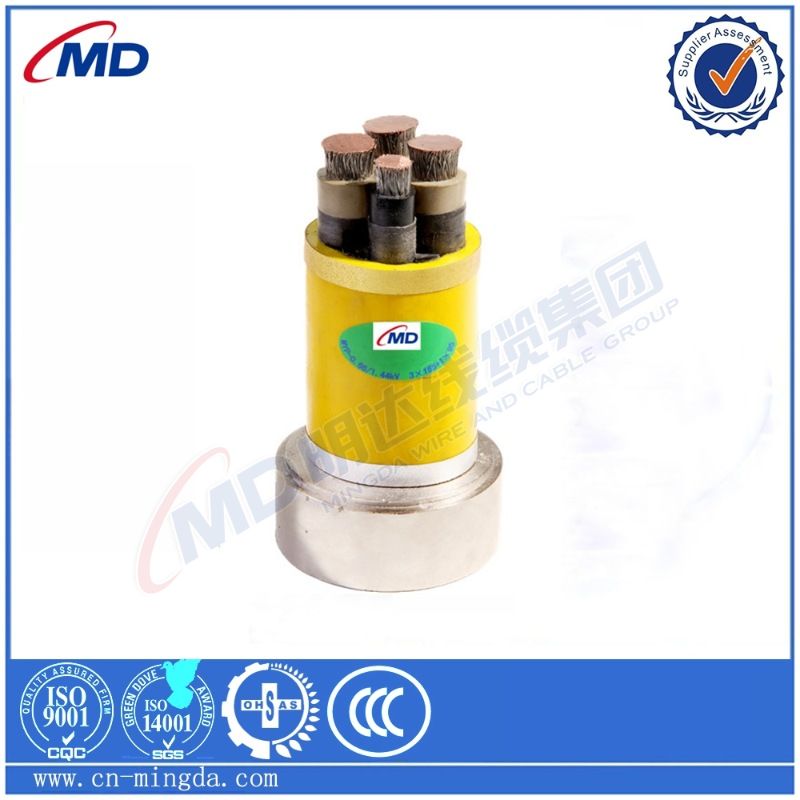
butterfly valve
Expert endorsements have shaped the authoritative stature of butterfly valves in industrial applications. Renowned manufacturers like Emerson and Kitz have pioneered advancements in valve technology, ensuring superior performance and extended lifecycle. These industry leaders invest in rigorous testing protocols, certifying their products under stringent international standards, such as ASME and ISO, to guarantee reliability and safety. Additionally, many such companies provide exhaustive technical documentation and customer support, reinforcing the assurance of product quality and providing valuable resources for system design and integration.
Trustworthiness remains a cornerstone for any operational component, and butterfly valves are no exception. Their dependability stems from meticulous manufacturing processes and advanced material science. A valve's integrity is often verified through pressure testing and lifecycle assessments, ensuring it withstands demanding operational environments. Industry feedback often lauds the robust construction and leak-tight performance, even in high-intensity settings. By maintaining a consistent track record of reliability, butterfly valves have cemented their place as trusted instruments in both conventional and cutting-edge systems.
Collectively, the synthesis of experience, expertise, authority, and trust empowers industry professionals to capitalize on the dynamic capabilities of butterfly valves. Each valve represents not just a mechanical component but a crucial element of a broader engineering strategy—streamlining fluid processes while safeguarding operational integrity. The continued evolution of materials and design principles holds promise for even greater innovations, ensuring that butterfly valves remain vital players in the landscape of fluid control. Investing in these valves means investing in the harmony of simplicity and sophistication, where each turn promises precision and reliability.