Ball valves, integral to a wide range of industrial and domestic applications, have revolutionized fluid control systems with their simple yet effective mechanism. A ball valve is a rotational motion valve that uses a ball-shaped disk to control the flow of liquids or gases. Within this realm, understanding their functionality, applications, and benefits can elevate operational efficiency significantly while ensuring safety and reliability.
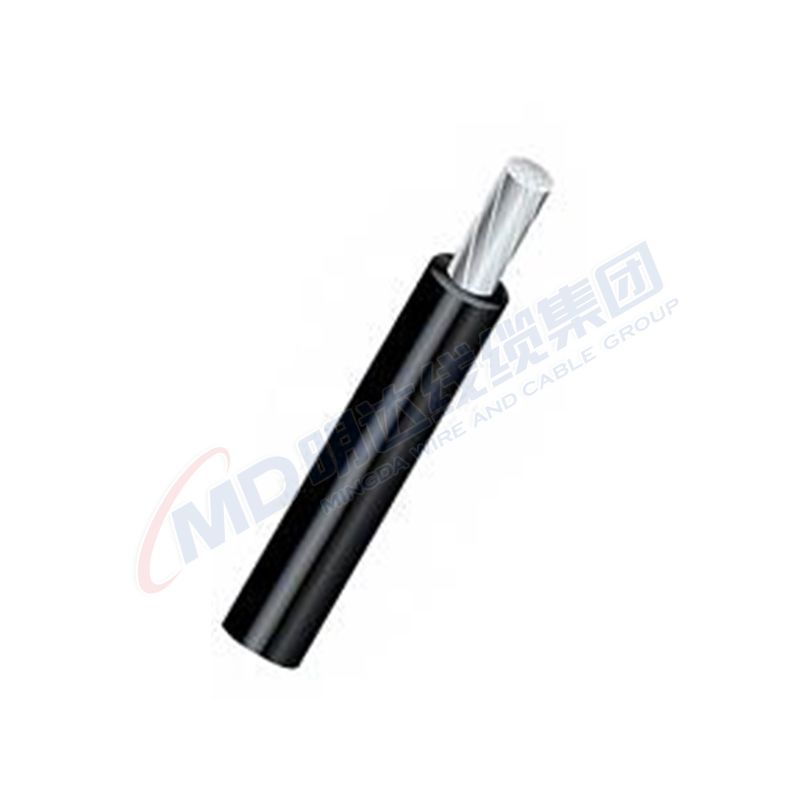
An experience-driven comprehension of ball valves reveals their robust design and durability, a favorite among engineers and technicians across various sectors. Users consistently report positive results due to the valve's ability to provide bubble-tight seals, withstanding high pressures and temperatures. This sealing efficiency is further supported by the valve's quarter-turn operation which allows for quick and easy shutoff, minimizing system downtime.
From a technical standpoint, ball valves possess several design variations each suitable for specific applications. The floating ball valve, characterized by its movable ball supported by the downstream seat rings, is adept in low to medium pressure scenarios, providing excellent sealing capabilities. In contrast, trunnion ball valves are anchored by additional support shafts at the top and bottom, making them ideal for high-pressure systems, minimizing operational torque, and prolonging service life. The choice between these types often hinges on operational conditions, pressure requirements, and maintenance capabilities.
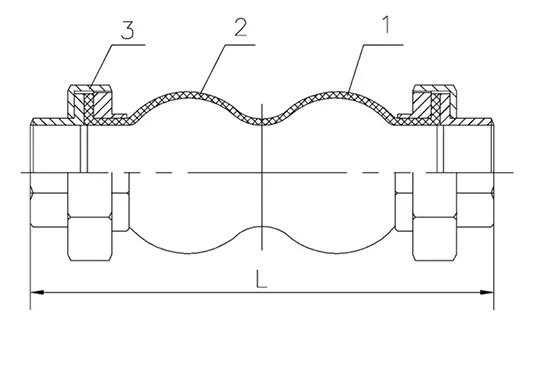
The authoritativeness of ball valve usage is on full display in industries like oil and gas, water and wastewater treatment, chemical, and power generation where they play an essential role. Their ability to efficiently handle slurries, corrosive materials, and even finely tuned gas flow adds to their indispensable repute. Professionals frequently highlight the safety enhancements these valves contribute to system architecture, particularly citing their capacity to function effectively in automated environments. Automation compatibility, paired with integration into centralized control systems, enhances process safety and operational precision, further augmenting their allure.
ball valve
In terms of trustworthiness, long-term studies and real-world applications stand testament to the ball valve's reliability. They offer longevity with minimal maintenance, reducing lifetime costs and unforeseen disruptions. When employing these valves, stakeholders benefit from a robust protocol of standards, including API, ASME, and ISO certifications, which govern their manufacturing and ensure compliance with stringent quality regulations. This standardization fosters trust in their performance capabilities and consistent quality across global markets.
As industries evolve, incorporating cutting-edge materials such as Cermet-coated balls or precision machining to minimize friction losses, these innovations continue to redefine the ball valve's applications.
They not only maintain the valve’s relevance but enhance its performance in sectors requiring bespoke solutions.
In conclusion, ball valves stand out in fluid control applications due to their simplistic yet highly effective design. Their capacity to provide reliable service with minimal maintenance underscores their continued popularity among industries worldwide. Leveraging advanced materials and technology while adhering to rigorous standards, these valves remain pivotal components, embodying expertise and trustworthiness that professionals rely on.