Wafer type butterfly valves have carved their niche as indispensable components in various industrial applications. They offer efficient flow control and easy installation, making them a favorite in industries ranging from water treatment to oil and gas. Understanding the dimensions and the intricacies of these valves can significantly impact installation efficiency and system performance.
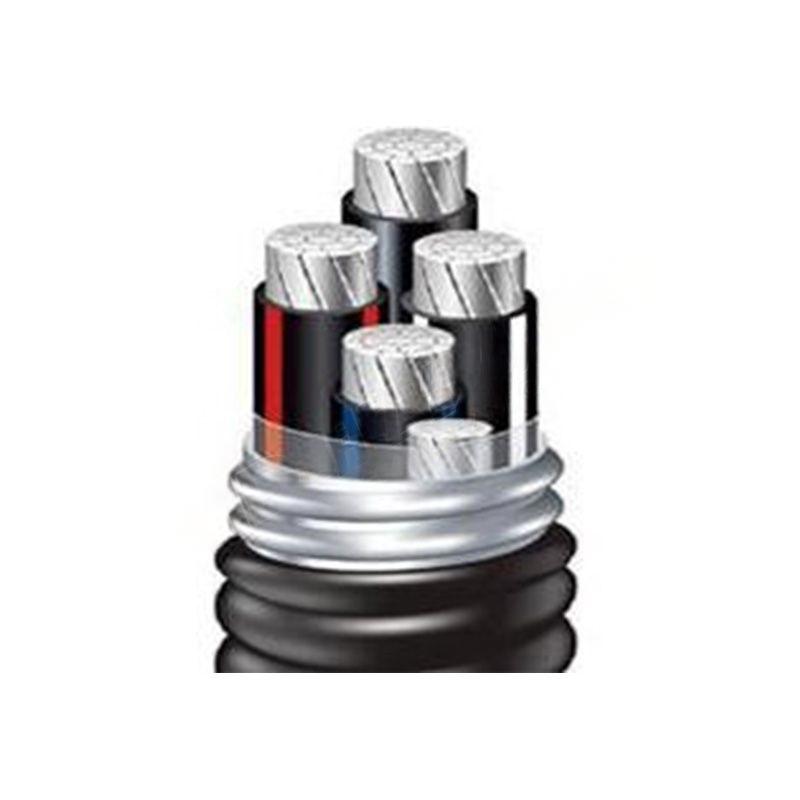
Typically, wafer type butterfly valves are characterized by their compact design and ease of use. These valves fit snugly between two pipe flanges. Instead of using bolts running through the entire valve, wafer butterfly valves rely on the flange bolts to hold the valve in place, providing a lighter and cost-effective option compared to lug-style valves.
The dimensions of a wafer type butterfly valve are crucial for ensuring compatibility and seamless integration into your existing piping system. The key dimensions include the valve's nominal diameter, face-to-face measurement, flange sizes, and bolt circle diameter.
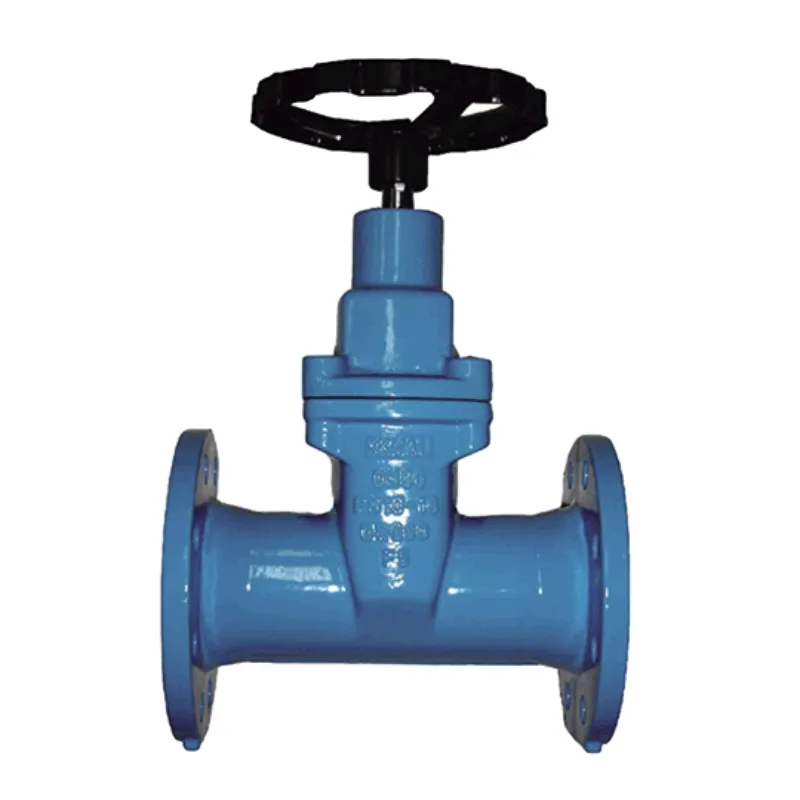
The nominal diameter (DN or NPS) is perhaps the most critical and basic dimension, as it determines the valve size required to fit your piping system. This measurement aligns with the pipeline's diameter, ensuring the valve can handle the system's flow capacity without causing turbulence or pressure drops.
Face-to-face measurement is the distance between the two ends of the valve that connect to the flanges. Its importance lies in maintaining system integrity and ensuring the valve fits perfectly into the allotted space, avoiding any potential misalignment which could lead to leaks or valve failure.
Flange sizes and bolt circle diameter ensure the valve can be securely mounted between the pipeline flanges. The proper alignment and installation of these connections are vital to preventing leaks and ensuring the system's long-term reliability.
wafer type butterfly valve dimension
The considerations don’t end with dimensions alone. Material selection plays a pivotal role in the performance and longevity of wafer type butterfly valves. Common materials include cast iron, ductile iron, stainless steel, and various types of plastics, each offering unique benefits suited to different environments. Stainless steel, for example, is favored in corrosive environments due to its resistance to rust and chemical degradation.
Despite being lightweight and compact, wafer type butterfly valves should not be underestimated in their function. The disc, which rotates to control the flow, should be made of materials that ensure minimal wear and tear while maintaining a tight seal to prevent leakage. The choice of sealing material impacts both the valve's temperature range and pressure handling capabilities.
For professionals in the industry, understanding the nuances of actuator compatibility is another aspect that cannot be overlooked. Wafer type butterfly valves can be operated manually or through an actuator for automated systems. Choosing the right actuation method—pneumatic, electric, or hydraulic—depends on the application requirements, such as speed of operation, control precision, and environmental factors.
In terms of installation, even though these valves are designed for ease, best practices suggest a thorough inspection of the valve seat and disc to ensure no foreign particles are present, which could compromise the seal and overall efficiency. Furthermore, the alignment of the valve within the piping system should be meticulously checked to mitigate any axial misalignment.
Regular maintenance of wafer type butterfly valves extends their lifespan significantly. Simple procedures like periodic cleaning, ensuring the actuator system works smoothly, and checking the sealing integrity can prevent unexpected system failures and costly downtime.
In conclusion, the efficacy of wafer type butterfly valves largely depends on a comprehensive understanding of their dimensions and material properties. Selecting the right valve for your application entails assessing these factors in tandem with the system's operational demands and environmental conditions. Adhering to these principles not only guarantees optimal performance but also upholds the high standards of safety and operational excellence expected in industrial processes.