Swing check valves are an essential component in fluid control systems, ensuring that the medium flows in only one direction and preventing potential backflow. In systems handling liquids such as water, oil, or gas, the proper function of these valves is crucial for both safety and efficiency. Here, we delve into the components, benefits, applications, and technical specifications of swing check valves to provide a comprehensive understanding of their importance and utility.
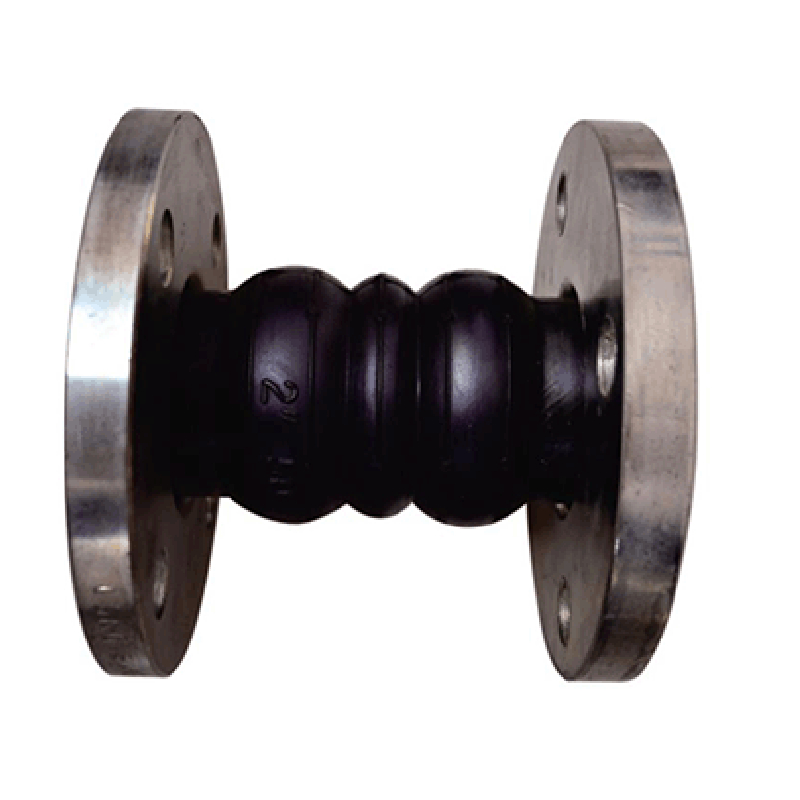
At the core of a swing check valve’s operation is a disk that swings away from the valve seat to allow forward flow and swings back onto the seat when the flow stops, thereby preventing backflow. The simplicity of this design ensures reliable performance even in demanding environments, making it a go-to choice in industries like oil and gas, water treatment, and power generation.
One of the standout qualities of swing check valves is their minimal pressure drop. Thanks to the unobstructed flow path, these valves facilitate smooth fluid dynamics, which is essential in applications where maintaining pressure levels is critical. The reduction in pressure drop not only optimizes the system's energy use but also prolongs the lifespan of the pump components by reducing operational stress.
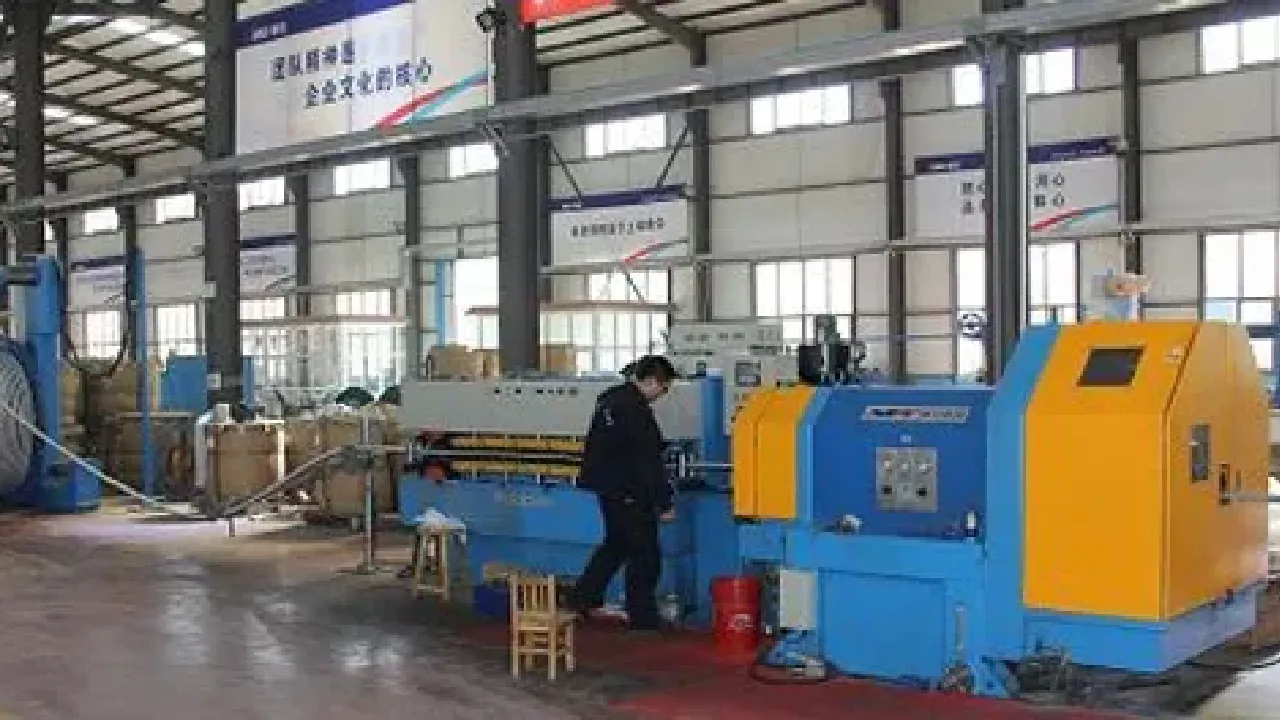
Swing check valves are favored for their versatility. Available in a variety of materials, including stainless steel, brass, and cast iron, these valves meet the needs of diverse industrial applications. The choice of material often reflects the specific requirements of a system, such as resistance to corrosion, ability to withstand high temperatures, or compatibility with different types of media.
Expert installation and maintenance are paramount to ensuring the longevity and effectiveness of swing check valves. While they are generally low-maintenance, regular inspections can preemptively identify potential issues such as wear and tear of the hinge or foreign material build-up, which can impede function. Hiring an experienced technician to assess and maintain the valves can save significant costs by preventing system downtime.
One of the challenges in implementing swing check valves is ensuring proper orientation during installation. Improper installation can lead to issues such as valve chattering, where the disk opens and closes rapidly due to turbulence, leading to wear and noise. This emphasizes the importance of following manufacturer guidelines and engaging with professionals who understand the nuances of fluid dynamics.
swing check valve
In terms of expert recommendations, considerations should include flow rate, pressure rating, and the specific gravity of the fluids being handled. Manufacturers typically provide detailed specifications to guide the selection of the appropriate valve size and material. Consulting these specifications and aligning them with the environmental and operational demands ensures the chosen valve delivers optimal performance.
Swing check valves must also comply with industry standards, which vary globally. For instance, in the United States, the American Society of Mechanical Engineers (ASME) provides guidelines that manufacturers and installation teams follow to ensure safety and efficacy. Having products certified with ASME standards or equivalent provides reassurance of their quality and suitability for use in critical applications.
Trustworthiness in swing check valve function is built on both product reliability and supplier reputation. It is advisable to work with established brands that have a proven track record and offer warranties on their products. These companies often provide comprehensive support, from technical guidance to after-sales service, which adds an additional layer of confidence in the product’s performance and durability.
When choosing a supplier, consider one that invests in research and development, continuously improving upon existing designs to enhance efficiency and reliability. These improvements may include innovations such as quieter operation, lower response time for closure, and enhanced material coatings that resist corrosion more effectively.
In conclusion, swing check valves are a vital component of fluid management systems across various industries. Their simple yet effective design, coupled with a wide range of material options, make them a reliable choice for ensuring unidirectional flow and preventing backflow. By focusing on proper installation, maintenance, and ensuring compliance with industry standards, users can maximize their system’s efficiency and longevity. Partnering with reputable suppliers guarantees that these critical components will perform as expected, maintaining the integrity and safety of the fluid systems they control.