Socket and resilient seat gate valves play an essential role in various industries, offering unparalleled reliability and performance for fluid control systems. As professionals navigate the complexities of pipeline installations, understanding the nuances of these gate valves becomes imperative.
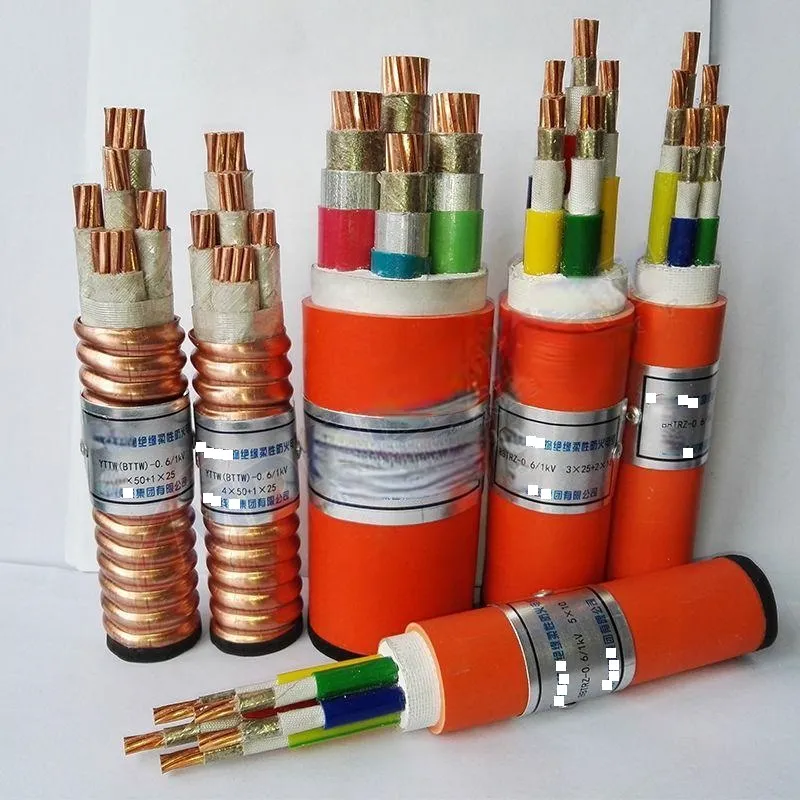
Engineers and industrial technicians frequently select socket and resilient seat gate valves due to their superior sealing capabilities and durability. The socket end ensures a simplistic yet robust connection ideally suited for high-pressure environments. This connection type facilitates straightforward installation and maintenance, diminishing the downtime often associated with industrial valve servicing. Furthermore, the structural integrity provided by the socket end enhances the valve's performance under stressful conditions, thereby ensuring system reliability.
The resilient seat design is another remarkable feature of these gate valves. Manufactured primarily from elastomers and reinforced with rubber components, the resilient seat offers exceptional sealing even in low-pressure applications, a distinct advantage over traditional metal-seated valves. This flexibility ensures a watertight seal, effectively minimizing the risk of leakage. Moreover, the adaptability of the resilient seat makes it less susceptible to the wear and tear typically encountered in systems experiencing frequent fluctuations in pressure and temperature.
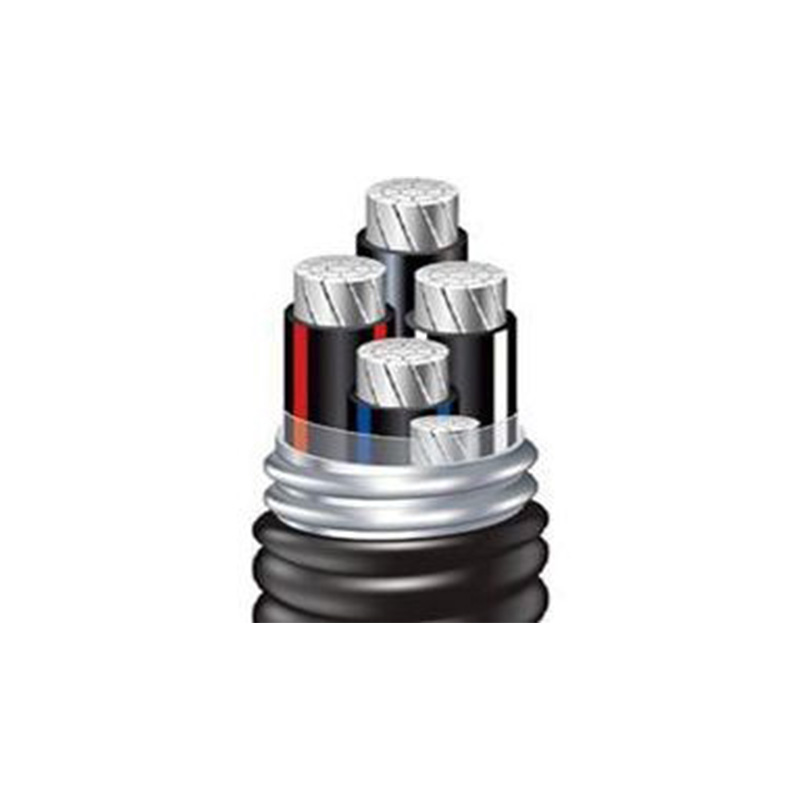
In industry contexts where durability and long-term performance are non-negotiable, professionals attest to the excellence of resilient seat gate valves. Manufacturers often highlight their resistance to corrosion and chemical degradation, rendering them suitable for diverse applications ranging from water treatment facilities to petrochemical plants. The valves' longevity is bolstered by their ability to resist scaling, thus requiring less frequent replacements and providing a cost-effective solution over their lifespan.
socket and resilient seat gate valve
From an operational standpoint, the gate valve's design facilitates smooth operation, requiring minimal torque. This ease of use translates to more efficient manual or automated control, thereby optimizing system efficiency. Technicians favor these valves for their dependable shutoff capabilities, which are crucial in preventing contamination and ensuring the integrity of the transported fluid.
Furthermore, industry experts underscore the importance of choosing the right materials for the construction of these valves. Factors such as fluid type, pressure, and temperature emphasize the need for careful selection to maximize the valve's efficacy and lifespan. This level of expertise ensures custom solutions tailored to meet the specific demands of varied applications, further solidifying the reputation of socket and resilient seat gate valves as trustworthy components in fluid dynamics.
As industries move towards smarter and more efficient systems, incorporating IoT technology with traditional valve mechanisms is becoming increasingly common. The adaptability of socket and resilient seat gate valves to these advancements is a testament to their engineering superiority. The integration of sensors and remote monitoring have further enhanced the reliability and operational oversight of these valves, enabling real-time diagnostics and predictive maintenance.
Across various sectors, the confidence placed in socket and resilient seat gate valves stems not only from their engineering excellence but also from a deep understanding of industry requirements. Their proven track record of performance and resilience has established them as authoritative components in fluid systems. Consequently, the trustworthiness of these valves continues to be affirmed by professionals and industry leaders globally, ensuring they remain at the forefront of fluid management solutions.