Single plate check valves, an indispensable component in modern fluid control systems, embody the perfect blend of efficiency and reliability. These valves, also known as swing check valves, play a crucial role in maintaining the directional flow of fluids, thereby protecting piping systems from potential damage caused by reverse flow.
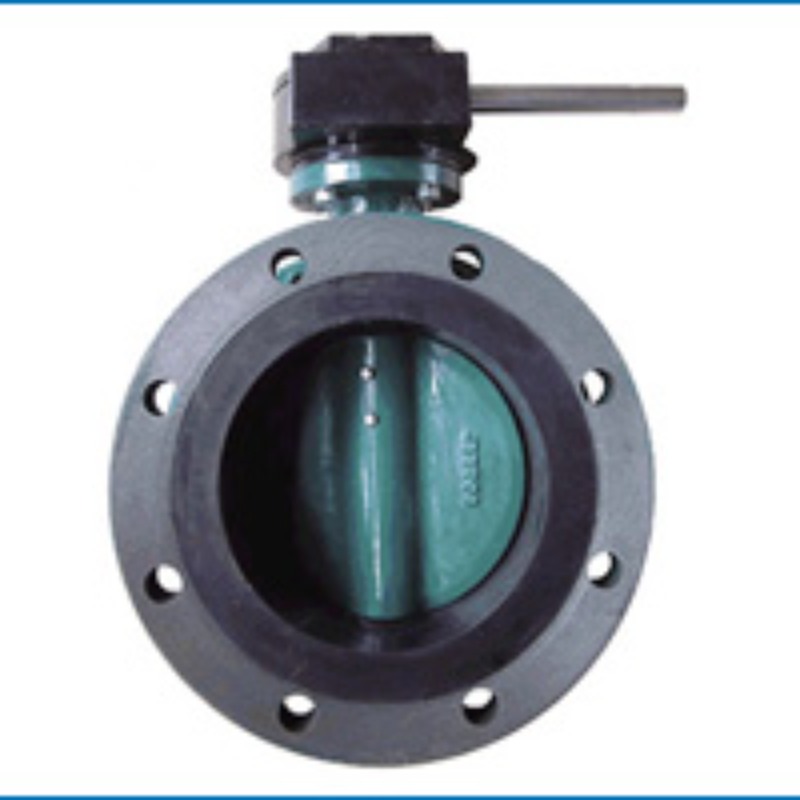
Understanding the importance of single plate check valves begins with acknowledging their functional capabilities. As fluid dynamics often involve various pressures and flow rates, ensuring that each valve in a system operates optimally is paramount. These valves, with their simple yet effective design, utilize a hinged disc to allow fluid to flow in one direction; when the flow stops or reverses, the disc automatically closes to prevent backflow. This seamless response to fluid flow changes makes single plate check valves exceptionally efficient.
The design of a single plate check valve typically features a compact and streamlined construction, which not only simplifies installation but also minimizes pressure drop across the valve. Their construction often uses robust materials like stainless steel, cast iron, or alloys that can withstand corrosive environments, high temperatures, and varying pressures. Therefore, they are widely used in industries ranging from water treatment and chemical processing to oil and gas.
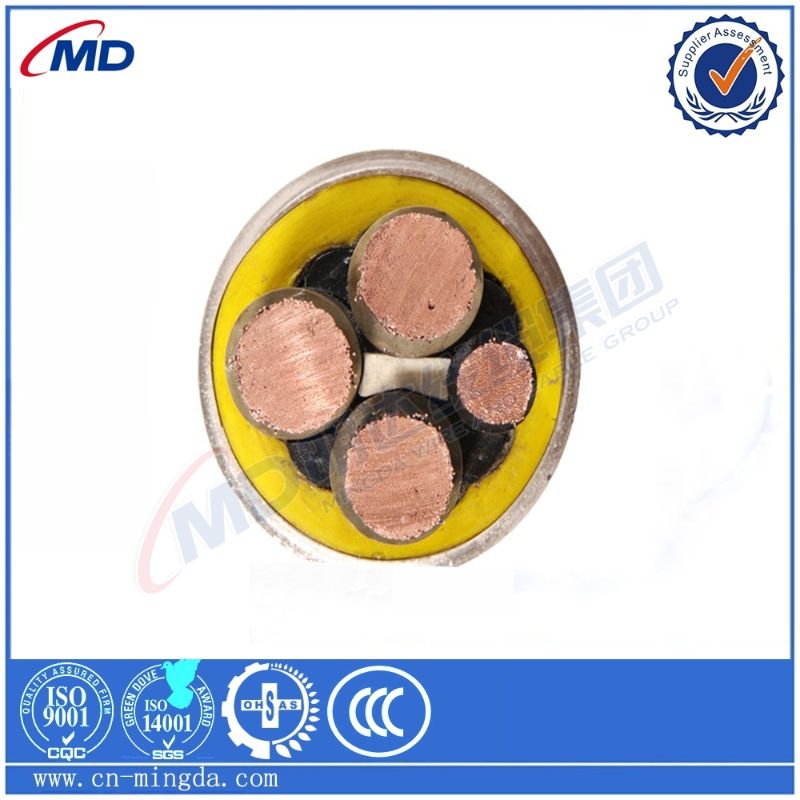
From an expertise perspective, it is essential to choose the right size and material of the single plate check valve to match the specific requirements of a system. Selecting an oversized valve can lead to unnecessary system costs and operational inefficiency, while an undersized valve may not provide sufficient protection against backflow. Therefore, engineers must conduct a detailed analysis of the system’s conditions such as the type of fluid, temperature range, and expected pressure drops. Leveraging software tools for flow analysis can further enhance the decision-making process, ensuring that the selected valve meets the application’s demands thoroughly.
single plate check valve
Single plate check valves also score high on maintenability. Their simplicity not only translates to easier installation but also to straightforward maintenance procedures. Periodic inspections, which involve checking for any wear or damage to the disc and its seating surface, can ensure long-term functionality. Moreover, these inspections can usually be carried out without removing the valve from the pipeline, thus reducing downtime and maintenance costs. This feature illustrates the valve's user-friendly design and operational economy.
With respect to authoritativeness, regulatory standards play a significant role in ensuring the reliability and safety of single plate check valves. Valves that comply with international standards such as API, ANSI, or DIN offer an additional assurance of quality. Manufacturers specializing in valve production generally subject their products to rigorous testing procedures to achieve certifications that underline their commitment to safety and performance.
Lastly, trustworthiness in the context of single plate check valves can be assessed by evaluating manufacturer reputation and customer reviews. Established manufacturers provide warranty offerings and after-sales support, which are crucial parameters for establishing customer confidence. Moreover, real-world case studies and testimonials can offer invaluable insights into the operational reliability of these valves across different scenarios and industries.
In conclusion, single plate check valves remain an integral element in fluid systems engineering, offering unmatched efficiency and reliability. Their strategic implementation, supported by precise technical specifications and periodic maintenance, ensures system integrity across various industrial applications. By adhering to recognized standards and leveraging technological advancements, organizations can maximize the performance and lifespan of their single plate check valves, thereby safeguarding their operations and investments.