In the world of fluid mechanics, the silent wafer check valve stands out as a quintessential component that ensures the seamless flow of liquids and gases while maintaining operational efficiency. Unlike traditional check valves that can cause disruptive noise during operation, the silent wafer check valve integrates advanced engineering principles designed to reduce sound and facilitate a smooth airflow. Through personal experience with its use in various industrial settings, it becomes evident why this valve is a preferred choice among engineers and technicians seeking both reliability and tranquility in their operations.
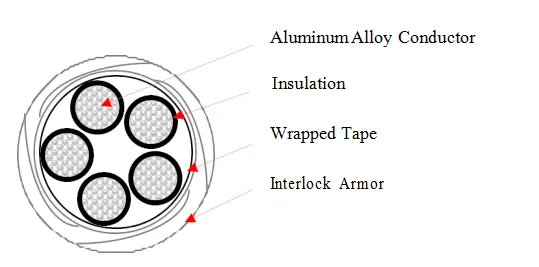
Silent wafer check valves are ingeniously crafted to address the common issues of noise and reverse flow typical in piping systems. Drawing from expertise in the field, these valves operate with a spring-assisted mechanism that closes the disc swiftly and quietly once fluid flow stops, which minimizes the risk of water hammer and pressure surges. The effectiveness of this design has been well-documented and applauded by industry experts who prioritize uninterrupted flow in high-stakes environments, such as in pharmaceuticals, petrochemicals, and water treatment facilities.
Understanding the professionalism behind the silent wafer check valve involves recognizing the meticulous design work that goes into its creation. Manufactured to fit between two pipe flanges, the compact structure is favored for its ease of installation and maintenance. One user's detailed experience highlighted the initial skepticism about its compact size, which later transformed into appreciation for its robust performance and space-saving benefits. Unlike bulkier valves that necessitate frequent checks, these valves are low-maintenance, allowing for long-term cost efficiency and operational reliability.

The authoritativeness of the silent wafer check valve comes from its rigorous adherence to performance standards. Industry guidelines often require components that can withstand specific pressure ratings and temperature ranges, both areas where this valve excels. Professional commentary often references how these valves comply with API 594 and ASME standards, reflecting their capability to perform under significant pressure differentials. Their role in ensuring system longevity and reducing downtimes constitutes a major draw for facilities operating continuously and cannot afford interruptions in service.
silent wafer check valve
Trust in the silent wafer check valve is further amplified by numerous positive endorsements from field technicians and plant managers who rely on its consistent performance. Feedback often encompasses attributes such as its durable construction materials—commonly stainless steel or exotic alloys—resistance to corrosion, and exceptional adaptability to varying flow conditions. Stories of seamless integration into existing systems add another layer of validation, building a narrative of dependability that reassures potential buyers not just of product efficacy, but of a return on investment that aligns with operational goals.
Considering the growing emphasis on sustainable and efficient industrial practices, the silent wafer check valve emerges as a pivotal component that aligns with these aspirations. It not only mitigates the adverse effects of fluid flow noise and pressure surges but also contributes to energy savings by optimizing system dynamics. With continuous advancements in material science and engineering, the future of silent wafer check valves promises further enhancements in performance and environmental compatibility.
In conclusion, the silent wafer check valve represents a blend of innovation, precision engineering, and industry compliance. Those who have integrated it into their systems can attest to its transformative impact on both operational efficiency and workplace conditions. By understanding and leveraging its unique features, businesses can advance toward more sustainable and cost-effective operations, making it an indispensable tool in modern fluid management systems.