Silent check valves, a pivotal innovation in fluid control systems, are renowned for their ability to maintain flow direction without the prevalent valve-induced noise. Predominantly used across various industries such as water treatment, oil and gas, and HVAC systems, these valves offer significant advantages in maintaining operational efficiency. The hallmark of a silent check valve is its expertly designed mechanism that prevents backflow while simultaneously minimizing water hammer, a common problem in pipeline systems.
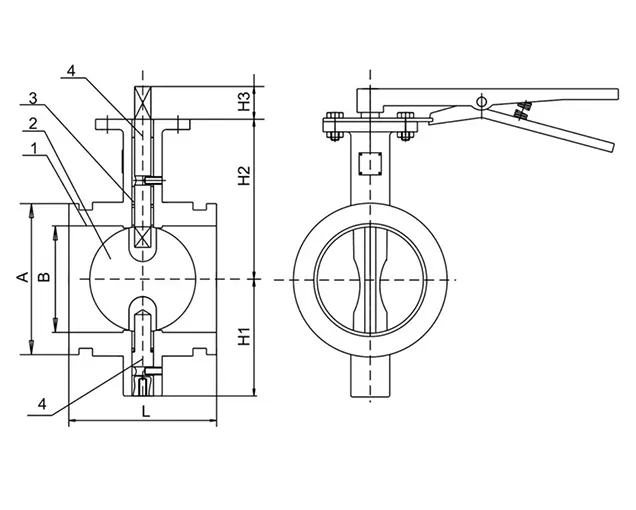
The operation of silent check valves relies on a spring-loaded disc that responds to fluid flow, ensuring that the valve opens and closes swiftly yet quietly. When the fluid pushes the disc, the valve opens, and upon a halt in flow, the spring mechanism ensures rapid closure. This prompt action prevents water from flowing backward,
thereby decreasing the likelihood of water hammer. The expert use of materials like stainless steel or other durable metals underpins the silent check valve's reliability in high-pressure applications, showcasing the remarkable engineering behind these devices.
Industries heavily depend on silent check valves due to their inherent trustworthiness and efficiency. For instance, in water distribution systems where constant operation is crucial, the non-intrusive nature of silent check valves ensures consistency and reliability. This trust in silent check valves stems from their robust construction and the long history of dependability in critical applications. Expertise in material selection and design parameter tuning allows manufacturers to offer silent check valves that meet specific industrial standards, thus guaranteeing operational longevity and safety.
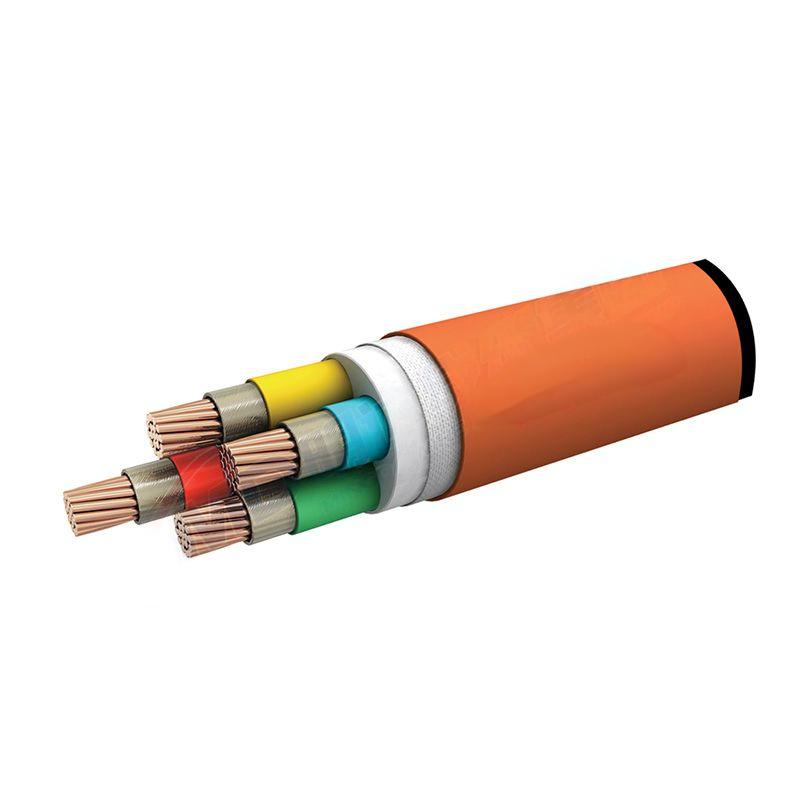
The installation of silent check valves contributes significantly to the reduction of maintenance costs. Given their streamlined operation, silent check valves are less prone to wear and tear, which translates into less frequent need for repairs or part replacements. This aspect brings an authoritative edge to silent check valves, as companies can rely on these components to function seamlessly for extended periods, enhancing overall system efficiency. The expertise embodied in the design and engineering of silent check valves is tailored to address the demanding needs of modern industrial processes.
silent check valve
Field experiences corroborate the efficacy and trust silent check valves provide. In real-world applications, these valves have demonstrated remarkable performance in mitigating the damaging effects of backflow and pressure surges. Operational data consistently highlights their role in extending the lifespan of piping systems by preventing undue stress caused by fluid surges. This reinforces the authoritative position silent check valves hold in the market as essential components of fluid handling systems.
Moreover, the adaptability of silent check valves to various environmental conditions is a testament to their versatility and dependable performance in diverse settings. Whether handling cold water in municipal services or managing hot steam in power plants, the expert craftsmanship involved in the production of silent check valves assures that they will perform optimally regardless of temperature swings or flow variations.
In conclusion, silent check valves represent a pinnacle of experience and engineering precision in fluid management. Companies invest in these valves not merely for their silence, but also for the authoritative assurance they convey through reliable, sustained use. Their expert design, operational trustworthiness, and proven track record in enhancing the service life of complex systems underscore their value in the evolving landscape of industrial fluid control solutions. With silent check valves, industries benefit from peace of mind and the confidence that operational demands will meet with seamless, silent compliance.