In the realm of industrial applications, products labeled for severe service must meet rigorous standards. Such products are specially designed to endure extreme conditions—be it temperature, pressure, or corrosive environments. Understanding and optimizing for severe service conditions require an expert blend of experience, technical knowledge, authoritative insights, and trustworthiness to ensure the right product is selected for the job.
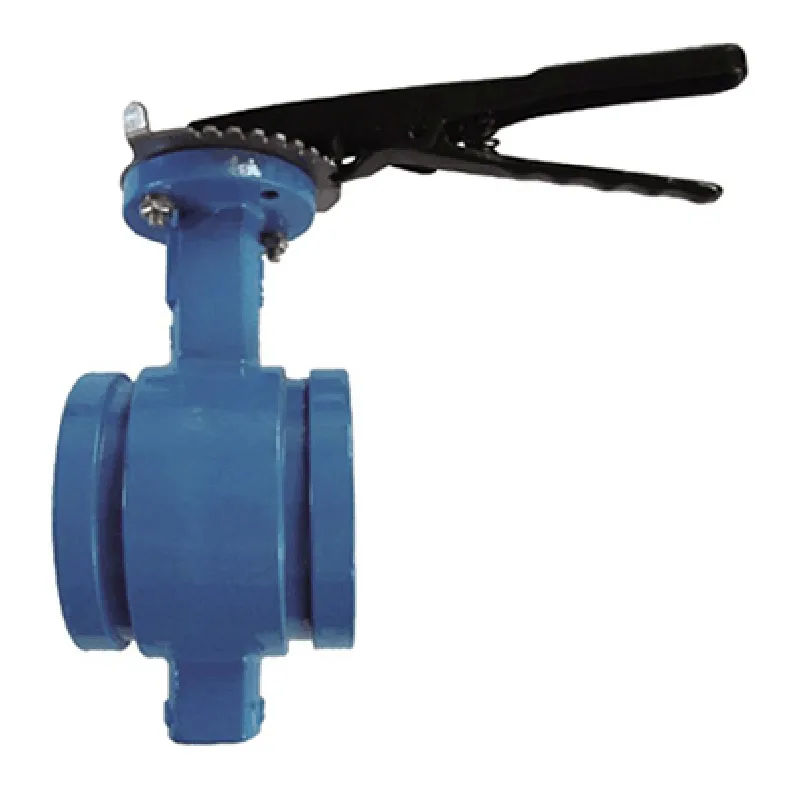
Experience plays a pivotal role in distinguishing products capable of truly surviving severe service conditions. The success stories of reliable brands in the industry often provide valuable insights. For instance, industrial valves used in petrochemical plants must perform without fail, as any malfunction could lead to catastrophic outcomes. For a product to earn its reputation for severe service, it must withstand real-world testing, demonstrating performance under the most strenuous conditions over time. Companies with decades of experience, such as Emerson or Flowserve, have developed products that reliably perform in these harsh environments. Experience, therefore, is not just measured in time but in the proven resilience and reliability of the products provided.
Expertise is crucial in developing products designed for severe service. Engineers and manufacturers deploy a deep understanding of materials science, physics, and engineering principles to innovate solutions that will hold up under duress. Take specialized coatings, for instance—they provide a critical barrier against corrosion and wear that can lead to failure in conventional equipment. Knowledge in metallurgy and chemical resistant materials enables manufacturers to tailor their products for the demands of different severe service industries, from chemical processing to oil extraction. Expert insights foster not only product development but also advise best practices for maintenance and operation, enhancing the lifespan and performance of the equipment.

severe service
Authoritativeness stems from a proven track record and certifications from recognized bodies. Products bearing endorsements from global standards organizations, such as the American National Standards Institute (ANSI) or the International Organization for Standardization (ISO), instill confidence in their capabilities. Manufacturers frequently subject their products to rigorous testing by independent organizations to demonstrate compliance with international standards. The authority of a product for severe service is also reflected in its industry certifications that verify its ability to operate under specified severe conditions, cementing its status as a reliable component in critical industrial processes.
Trustworthiness cannot be overstated when it comes to severe service products. Trust is built on transparency regarding the materials used, manufacturing processes, and performance statistics. Detailed documentation, including case studies and performance analyses, should be readily available to potential buyers, clearly illustrating how a product has performed in environments similar to their own. Manufacturers should provide clear guidance on installation and maintenance to further assure users of the product's reliability and longevity. When companies take accountability for their products by offering robust warranties and exemplary customer service, they earn the trust of their clients, who depend on these products to keep their operations running smoothly.
In the ever-evolving landscape of severe service industrial applications, the confluence of experience, expertise, authoritativeness, and trustworthiness defines the success of products designed to operate in the harshest conditions. By prioritizing these elements, companies not only ensure their products perform to the highest standards but also foster enduring relationships rooted in reliability and mutual success with their clients.