Rubber joint expansion products play an essential role in many industrial and residential piping systems. Their primary purpose is to absorb heat-induced expansion and contraction in pipelines, misalignment of spools, reduce vibration, noise, and shock, and accommodate building settling and ground shift. But to truly appreciate their value, it's crucial to understand their unique benefits, specific applications, and what sets high-quality rubber joint expansions apart in the global marketplace.
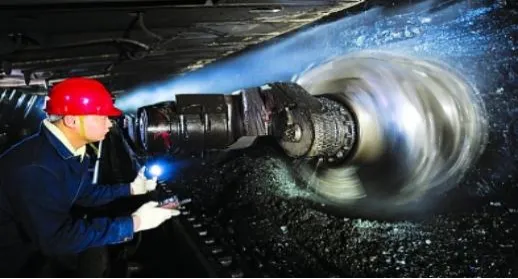
The experience with rubber joint expansions extends across various industries—from construction to chemical plants, waste treatment facilities to HVAC systems. What makes rubber joint expansions invaluable is their ability to maintain system integrity and efficiency under challenging conditions. Expert installers and engineers appreciate that while metallic expansions are often the default solution due to historical usage, rubber joint expansions actually provide superior flexibility and vibration damping that metals cannot match.
Professionally speaking, the expertise required to deploy rubber joint expansions effectively involves understanding the unique properties of different rubber materials. For instance, EPDM rubber is praised for its resilience in extreme temperature ranges and its environmental resistance. In contrast, Neoprene, Nitrile, or PTFE-coated rubbers are selected for their chemical resistance and specific application suitability. Identifying the right type of rubber is crucial because it ensures longevity and optimal performance, which is what any industry desires to maximize return on investment.
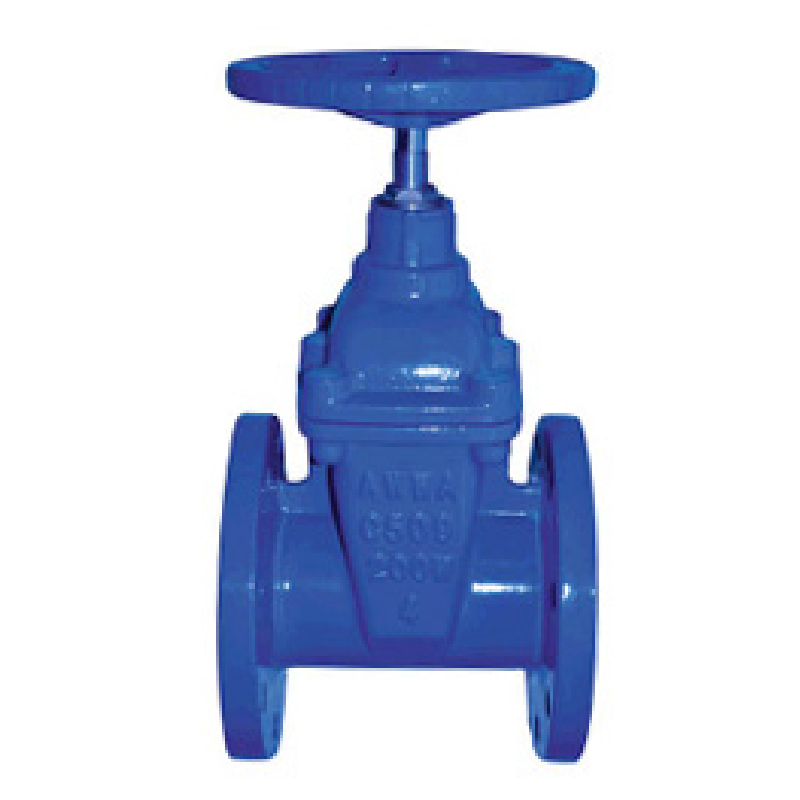
From an authoritative stance, guidelines from organizations like the Rubber Expansion Joints Division of the Fluid Sealing Association provide design, manufacturing, and installation standards. These guidelines are critical to ensuring reliability in systems that are, frankly, punishing environments for any form of joint. Certification and compliance with industry standards highlight the manufacturer's commitment to quality and safety, which serve as a trust metric for customers seeking dependable performance.
Trustworthiness is further enhanced in rubber joint expansions by real-world testing and customer testimonials, which paint a reliable picture of what to expect post-installation. Rubber joints are exposed to pressure tests and real-life operational conditions that challenge their design. Engineers can trust in their application when evidence shows that advanced compounds and manufacturing techniques yield products capable of withstanding immense mechanical stress.
rubber joint expansion
The versatility of rubber joint expansions is seen across various parameters, such as size diameters ranging from a few inches for household systems to several feet for large industrial applications. Moreover, their ability to be customized for specific pressures and temperatures makes them indispensable across industries that require specific tailoring to their operation environments.
In product selection, several key factors come to play the operational environment, required flexibility, pressure load expectations, media running through the system, and desired lifespan. These factors guide professionals when recommending products to clients. A well-chosen rubber joint not only enhances the safety and longevity of the piping system but also dramatically reduces maintenance costs and unscheduled downtime.
Ultimately, the field of rubber joint expansions is one where innovation is constantly evolving, driven by the need for increased durability and environmental adaptability. Industry advancements in compounding and structural design pave the way for products that are not only performing better but are also more environmentally friendly by reducing waste through extended service life and more efficient material usage.
In conclusion, rubber joint expansions hold a vital role in today's industrial and residential environments. Their unique characteristics of flexibility, durability, and adaptability make them a preferred choice for modern engineering needs. By focusing on material expertise, adherence to authoritative standards, and building trust through proven performance, the right rubber joint expansion can transform the efficiency and reliability of your piping systems.