Rubber joints have become indispensable in modern industrial applications, offering a versatile solution for vibration reduction, noise attenuation, and accommodating misalignments in piping systems. Unlike their metal counterparts, rubber joints provide enhanced flexibility and resilience under diverse conditions, making them a preferred choice in sectors ranging from chemical processing to HVAC systems.
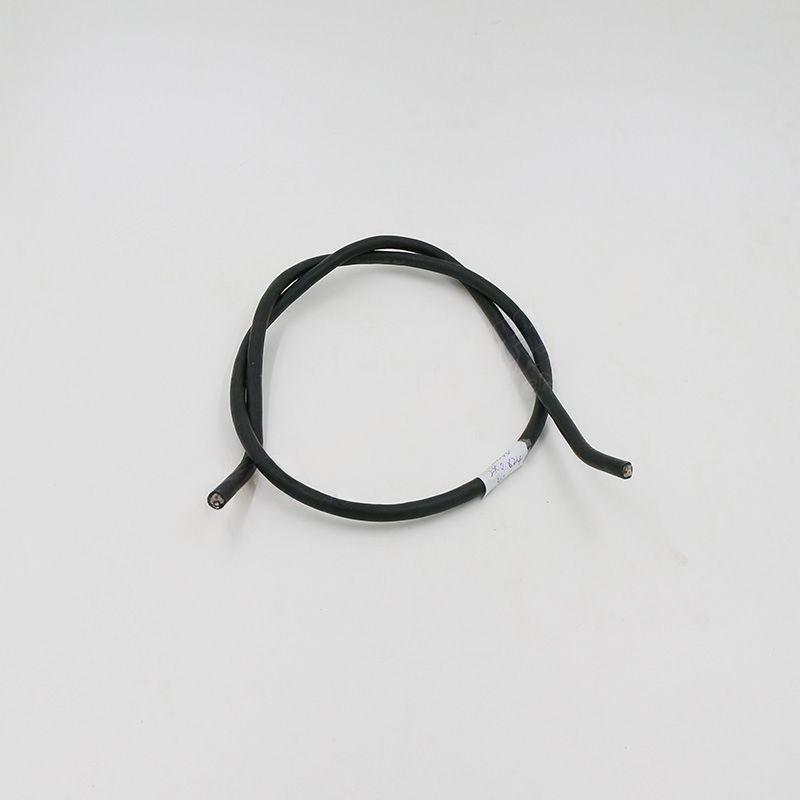
When discussing the real-world experience of using rubber joints, several benefits stand prominent. Users consistently report a notable reduction in system vibration, which is crucial for minimizing wear and tear that can lead to costly maintenance. For instance, in high-pressure water systems, rubber joints absorb substantial shock, preventing potential damage to connected components. This flexibility under pressure not only prolongs system life but also maintains the integrity of pipeline connections, ensuring optimal performance.
The expertise in rubber joint manufacturing has evolved significantly, focusing on multiple aspects such as material composition, durability, and temperature resistance. High-grade EPDM, neoprene, and NBR are among the materials often used, each offering unique properties. EPDM is excellent for resisting weather and ozone,
ideal for HVAC and outdoor applications. Neoprene provides superior oil resistance, making it suitable for petroleum-based environments, whereas NBR is highly effective in handling moderate temperature ranges and various chemicals. Understanding the material properties is key for specialists aiming to optimize system functionality and lifespan, thereby enhancing product reliability.
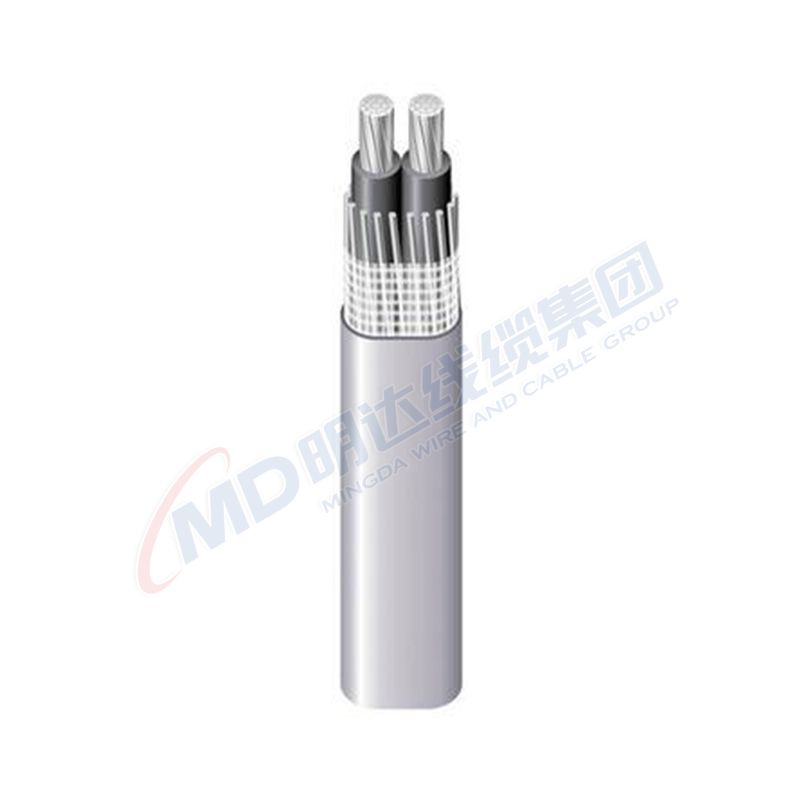
Authoritativeness in the field of rubber joints is demonstrated through strict adherence to international standards such as ASTM, ISO, and ANSI. Products manufactured under these guidelines guarantee not only quality but also compatibility with a wide array of industrial norms and equipment. Industry leaders regularly publish studies and white papers detailing innovations and improvements in rubber joint technology, highlighting advancements such as enhanced tensile strength and decomposition resistance. Adoption of these standards results in products that stand up to demanding application requirements, establishing confidence in their use.
rubber joint
Trustworthiness is built on the foundation of rigorous testing and quality assurance procedures. Leading manufacturers implement extensive testing regimens before products reach the market, including hydrostatic, burst, and cycle life tests. Furthermore, case studies showing successful long-term deployments across various industries serve to reassure potential users of their dependability. Testimonials from professionals in the field consistently highlight the efficacy of rubber joints in challenging environments, further establishing trust in their performance. By ensuring that every aspect of design, production, and testing meets the highest industry standards, manufacturers foster long-lasting relationships with their clients, who rely on their products for mission-critical operations.
For engineers and procurement specialists looking to integrate rubber joints into their systems, several considerations are vital. Selecting the appropriate rubber joint involves evaluating the application's specific requirements — pressure ratings, chemical exposure, and temperature range are critical factors that influence joint selection. Consulting with a supplier that provides expert guidance and support can simplify this process significantly. Tailored solutions that address particular operational needs not only improve system efficiency but also align with budgetary constraints, ensuring cost-effectiveness.
In conclusion, rubber joints stand as a testament to engineering innovation, combining material science and industrial necessity to deliver solutions that meet and exceed modern demands. Their role in enhancing the performance and longevity of piping systems is undeniable, with continued advancements promising even greater efficiency and application diversity. As industries evolve, so too will the technology behind rubber joints, ensuring they remain an integral component of infrastructure projects worldwide.