Rubber expansion joint flange types have emerged as critical components in industrial piping systems, providing solutions that address the issues of vibration, stress, and heat. The reliability and efficiency of these products make them indispensable in various sectors, including petrochemicals, water treatment, and power generation. Understanding the intricacies of these joints is vital for engineers and procurement specialists seeking durable solutions.
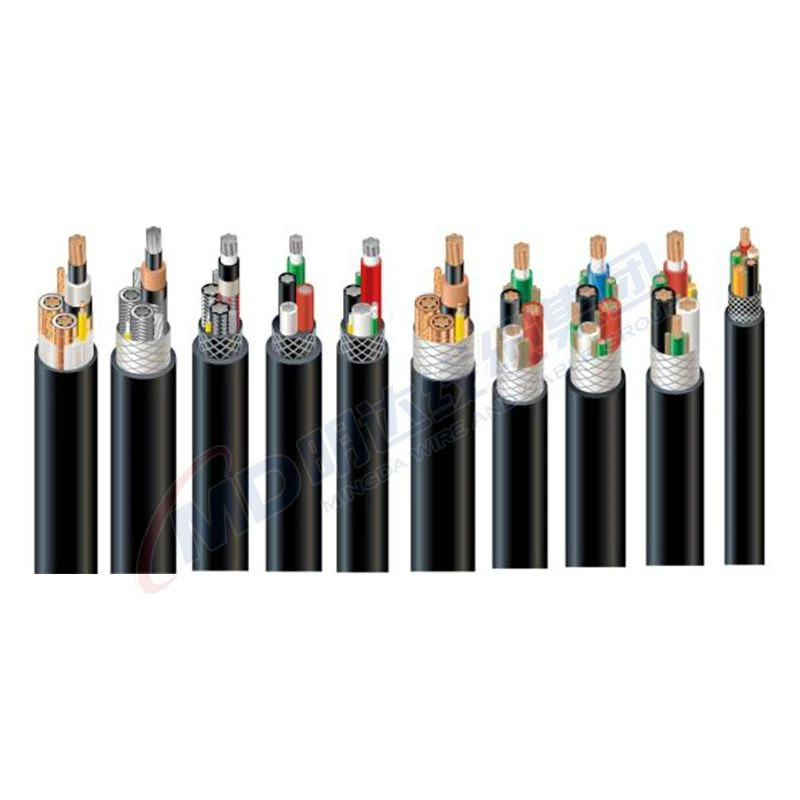
Flange type rubber expansion joints are specifically designed to connect two fixed parts of a piping system, providing flexibility, vibration absorption, and noise reduction. These joints typically consist of a flexible rubber element flanked by metal flanges on either end. This combination not only enhances their ability to withstand pressure and temperature fluctuations but also facilitates easy installation and maintenance.
The longevity and reliability of rubber expansion joints largely depend on the rubber material used. Natural rubber, EPDM (ethylene propylene diene monomer), and neoprene are among the most common materials, each offering unique properties suited for different environments. For instance, EPDM boasts excellent resistance to heat, ozone, and weathering, making it ideal for outdoor and high-temperature applications. Conversely, neoprene provides superior resistance to oil and grease, making it preferable for petrochemical industries.
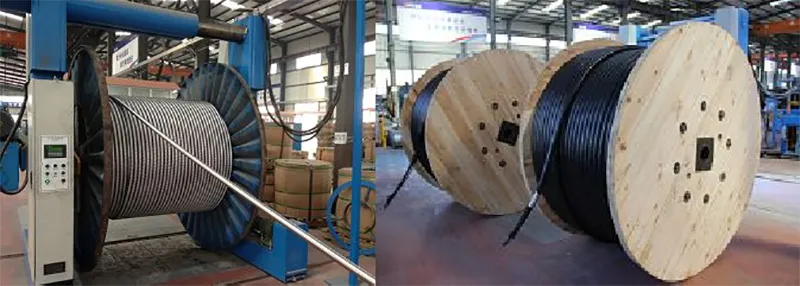
Engineering experts emphasize the importance of specifically selecting the right flange material to complement the rubber component. Common flange materials include carbon steel, stainless steel, and ductile iron, chosen based on the demands of particular applications. Stainless steel offers excellent corrosion resistance, which is crucial in environments exposed to corrosive fluids or harsh weather conditions. In comparison, carbon steel is often chosen for its cost-effectiveness and strength, provided that the environment isn't corrosive.
Incorporating rubber expansion joint flange types into a piping system improves flexibility by allowing axial compression and lateral deflection, which minimizes stress on pipes and anchors. It also notably enhances the system's ability to manage thermal expansion, pressure surges, and vibrations, which can significantly extend the lifespan of the entire assembly. For industrial plants where these factors are prevalent, the implementation of high-quality rubber expansion joints can reduce maintenance costs and prevent unplanned downtime.
rubber expansion joint flange type
A crucial aspect of the application of these joints lies in their ability to protect sensitive components and machinery. By absorbing mechanical loads and settling pipe misalignments, they prevent the transmission of these forces to pumps, valves, and other critical components, ensuring smoother operation and longevity of equipment. In water treatment facilities, for instance, the dynamic nature of flow operations might induce severe vibrations, making rubber expansion joints essential in preserving the integrity of complex systems.
Experts also highlight the installation practices as pivotal to the performance of rubber expansion joints. Proper alignment, correct bolt torque, and appropriate flange face interaction significantly impact the joint's efficacy and durability. Regular inspection and maintenance, including checking for signs of wear or degradation and ensuring bolts remain securely tightened, can prevent failures and ensure optimal functionality over an extended period.
In terms of authoritativeness and trustworthiness, manufacturers with ISO certifications and compliance with international standards such as ASTM (American Society for Testing and Materials) or EN (European Norms) provide assurance of quality and performance. Procuring products from reputable manufacturers reduces the risk of substandard quality and enhances trust in the product's ability to meet operational needs.
Furthermore, the ongoing advances in technology are yielding innovative rubber formulations and joint designs that offer improved performance characteristics. For example, newly developed rubber compounds with superior chemical and temperature resistance are expanding the operational envelopes of these joints, facilitating their application in highly demanding environments.
Conclusively, rubber expansion joint flange types play an instrumental role in enhancing the resilience and efficiency of piping systems across various industries. The thoughtful selection of materials, adherence to proper installation protocols, and regular maintenance are essential practices to maximize their benefits. By leveraging the expertise of seasoned professionals and certified manufacturers, businesses can ensure high performance and reliability of their piping systems, ultimately safeguarding their investments and operational productivity.