Rising stem globe valves are a critical component in many industrial applications where fluid control is essential. These valves are favored for their ability to provide tight shut-off capabilities while offering precise flow regulation. Their unique design, characterized by a stem that rises out of the valve body when opened, provides an immediate visual indication of the valve's status—an advantageous feature in high-stakes environments.
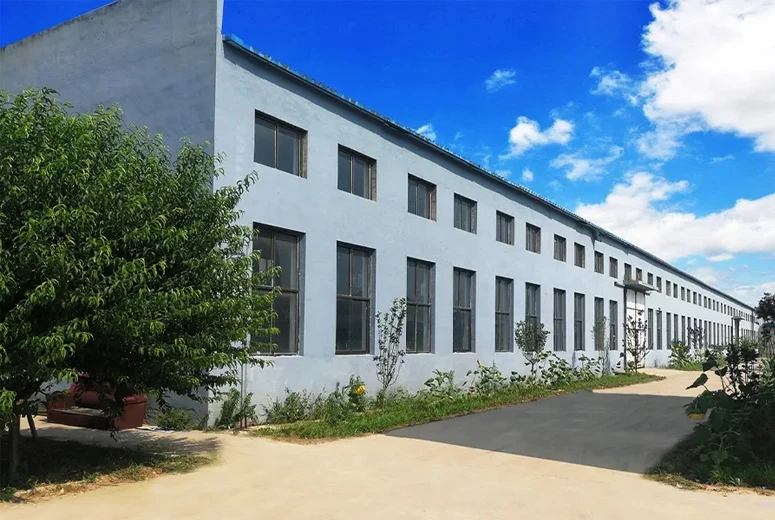
Industrial experts understand that choosing the right valve is pivotal for optimizing performance and ensuring safety within fluid management systems. With years of hands-on experience in the field, I’ve seen how rising stem globe valves have outperformed other valve types in scenarios demanding stringent regulatory compliance and unmatched reliability.
Rising stem globe valves are frequently employed in industries such as oil and gas, chemical processing, and water treatment. They are ideal for applications involving high-pressure scenarios and corrosive media. Their design allows for a throttling function, which makes them suitable for varying flow conditions. This adaptability is a major reason why they are trusted in environments where flexible operation and precise control are paramount.
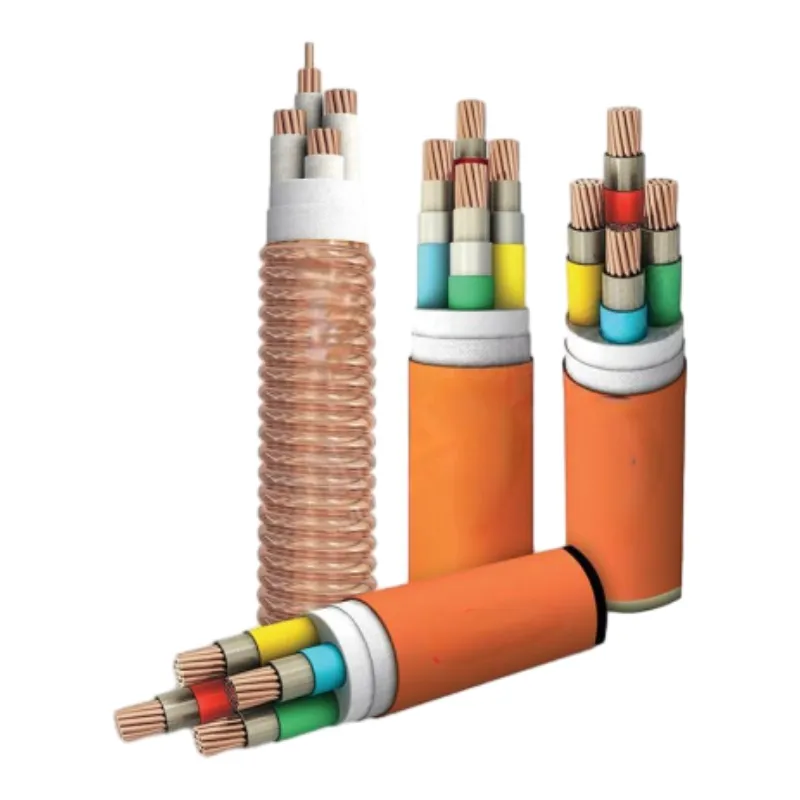
From an engineering perspective, the rising stem design is ingenious. As the valve opens, the stem moves upward. This action provides several advantages It prevents the valve seat from being exposed to direct flow, which minimizes wear and extends the valve's lifespan. Furthermore, it enables easy monitoring, as operators can quickly determine if the valve is open or shut simply by observing the stem's position. This characteristic is particularly useful in systems where multiple valves are in close proximity.
rising stem globe valve
The construction of a rising stem globe valve typically involves materials such as stainless steel, bronze, or cast iron, selected according to the specific operating environment. The material choice directly impacts the valve's durability, corrosion resistance, and ability to withstand high temperatures and pressures. Stainless steel, in particular, is often chosen for its exceptional resistance to corrosive substances and high heat, making it a go-to option for chemical processing plants.
Installation and maintenance are critical aspects affecting the performance and longevity of rising stem globe valves. During installation, care must be taken to ensure that the valve is aligned correctly within the pipeline to prevent leaks and minimize turbulence. Maintenance involves regular inspections to ensure the stem operates smoothly and seats remain uncontaminated. For those with extensive operational experience, it's clear that routine maintenance can prevent costly downtimes and avoid catastrophic system failures.
In terms of authority and trustworthiness, manufacturers of rising stem globe valves often undergo rigorous testing to comply with international standards such as API and ASME. Certification from these organizations is a testimony to the valve’s quality, affirming its suitability for use in critical applications. As part of best practices, industries often collaborate with certified suppliers to secure valves that not only meet but exceed these stringent standards.
In conclusion, the rising stem globe valve is a quintessential tool in robust industrial fluid control. Its design, material selection, installation precision, and adherence to international standards underscore its role as a reliable component in complex systems. By integrating these valves into their operations, industries fortify their infrastructure against the challenges of modern processing demands. Through careful selection and maintenance, these valves ensure that fluid control systems operate efficiently and securely, reflecting the pinnacle of engineering expertise and operational dependability.