Exploring the World of Pneumatic Butterfly Valves Unmatched Efficiency and Control
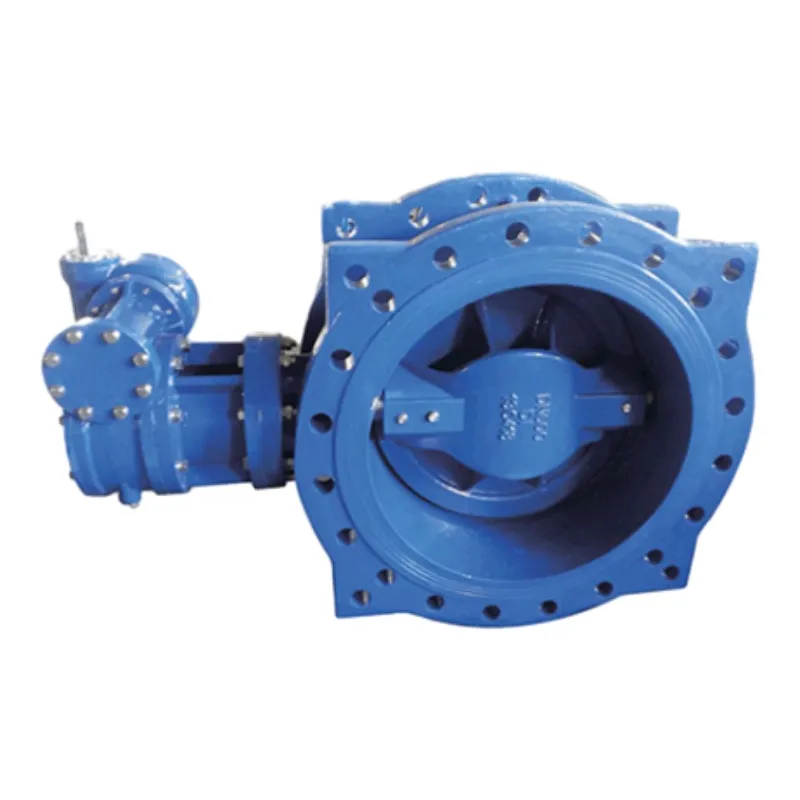
Pneumatic butterfly valves stand as a testament to the evolution of control mechanisms in fluid management systems. Known for their precision, durability, and efficiency, these valves play a pivotal role across numerous industries, from chemical processing plants to water treatment facilities. Here, we delve into the unique advantages and applications of pneumatic butterfly valves, highlighting their unparalleled capabilities and reassuring reliability.
Pneumatic butterfly valves are characterized by their distinct design—a disc mounted on a rotating shaft within a pipe. When the valve is closed, the disc blocks flow, and when open, it aligns with the flow, offering minimal resistance. What sets pneumatic butterfly valves apart is their actuation mechanism. Powered by compressed air, these valves offer swift and precise control, making them ideal for applications requiring rapid response times.
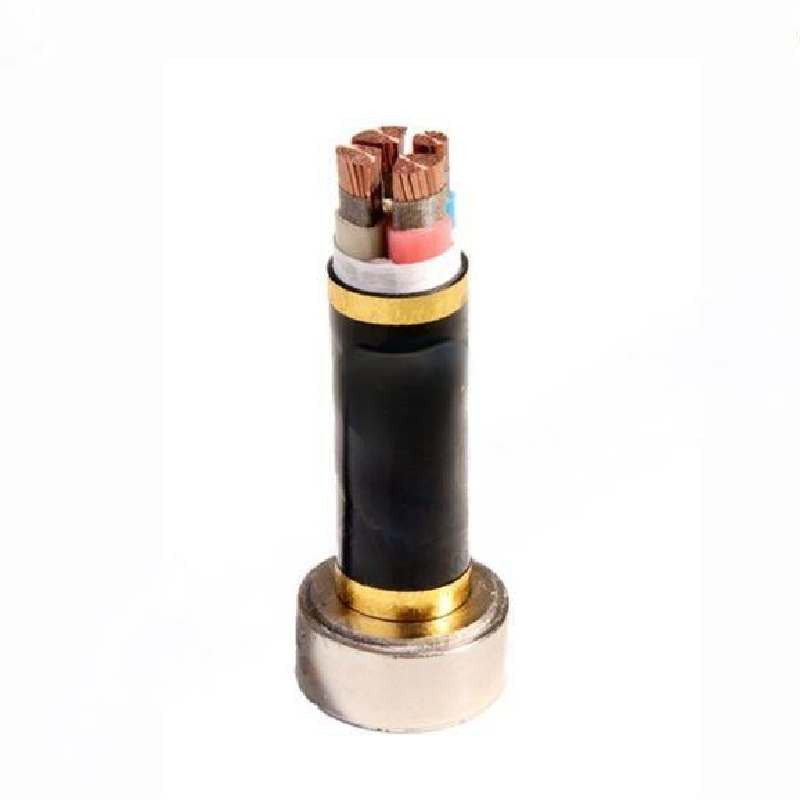
The engineering precision of pneumatic butterfly valves is evident in their ability to handle various media, including liquids, gases, and slurries. Their design minimizes pressure drop across the valve, ensuring efficient flow with minimal energy loss. This efficiency translates to reduced operational costs, a factor that significantly contributes to their widespread adoption.
Material selection is critical in the design of pneumatic butterfly valves, influencing their endurance and compatibility with different media. Valves constructed from stainless steel, for example, exhibit excellent resistance to corrosive environments, making them suitable for chemical industries. Meanwhile, those made with PVC or other synthetic materials are often chosen for applications involving less aggressive fluids. This diverse material adaptability ensures that pneumatic butterfly valves can be tailored to specific operational requirements, enhancing their versatility and utility.
pneumatic butterfly valve
The expertise involved in the manufacturing of pneumatic butterfly valves reflects decades of refinement and innovation. Modern valves are equipped with advanced sealing technologies that prevent leaks and ensure a long service life. High-quality elastomers and precision machining techniques contribute to the robustness of these seals, offering peace of mind in critical applications where containment of hazardous or precious substances is paramount.
Moreover, the installation of pneumatic butterfly valves is relatively straightforward compared to other valve types. Their compact design and lighter weight reduce the structural load on piping systems, facilitating easier assembly and maintenance. This ease of integration is particularly beneficial in retrofit projects, where existing infrastructure constraints demand flexible and adaptable solutions.
In terms of operational control, pneumatic butterfly valves excel with their quick opening and closing capabilities. The pneumatic actuators driving these valves can be finely tuned for either gradual modulation or rapid cycling, depending on the specific application needs. This adaptability in control makes them an authoritative choice for automated systems where precision and repeatability are crucial.
While pneumatic butterfly valves are renowned for their efficiency and ease of use, their reliability is equally noteworthy. They are designed to withstand harsh conditions, maintaining functionality in environments characterized by extreme temperatures, pressures, and chemical exposures. Their robust construction and dependable performance ensure that they uphold the trust placed in them by industries reliant on stable and consistent operational outputs.
In conclusion, pneumatic butterfly valves represent the epitome of experience, expertise, authority, and trustworthiness in the field of fluid control. Their ability to deliver precise regulation with high efficiency makes them indispensable in modern industrial applications. As the demand for smarter, more efficient industrial systems grows, the role of pneumatic butterfly valves as essential components of these systems becomes increasingly prominent. Their continued evolution promises even greater advancements in efficiency and control, positioning them as pivotal players in the future of industrial fluid management.