A non-return ball valve, often known as a check valve, is an essential component in various fluid handling applications. It functions primarily to permit fluid flow in one direction while preventing backflow, making it invaluable in systems such as water, oil, and gas pipelines. This simple yet effective mechanism ensures the longevity and efficiency of a multitude of industrial processes.
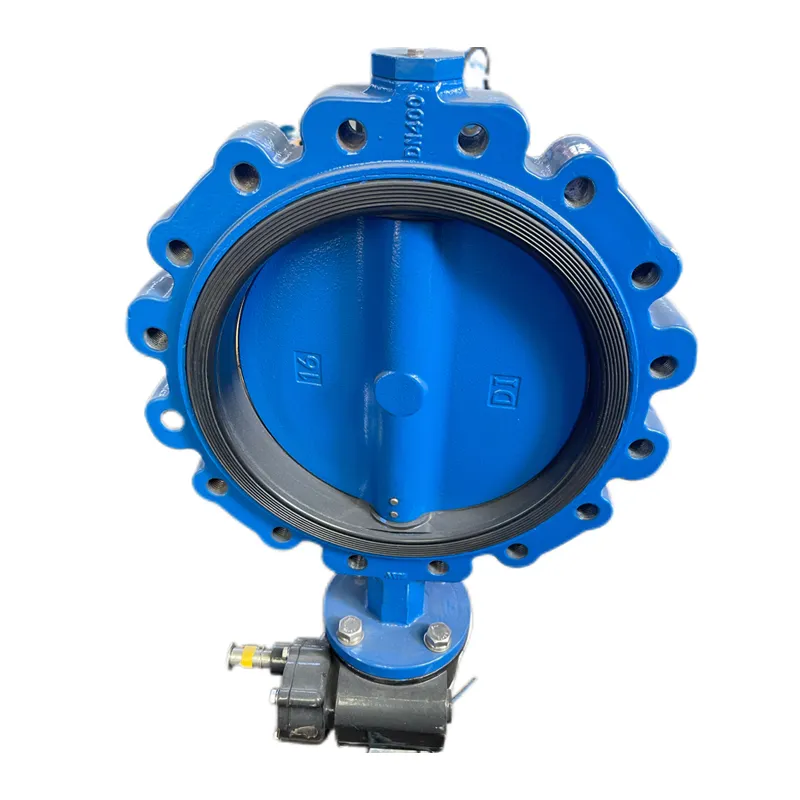
In engineering, the design and choice of a non-return ball valve can significantly influence operational efficiency and cost-effectiveness. The ball valve is highly prized for its quick-acting function. When fluid enters the valve, the pressure pushes a ball, usually made of stainless steel or another robust material, allowing fluid to flow through. Should the fluid attempt to reverse direction, the ball is immediately pushed into the seat of the valve, effectively sealing and preventing backflow.
The expertise involved in selecting the appropriate non-return ball valve is crucial for maintaining system integrity. Considerations include the material compatibility with the fluid, pressure ratings, and the operational environment. For instance, a ball valve used in a corrosive chemical pipeline needs to be made from materials resistant to corrosion to ensure longevity and avoid potential leaks that could have severe environmental or safety consequences.
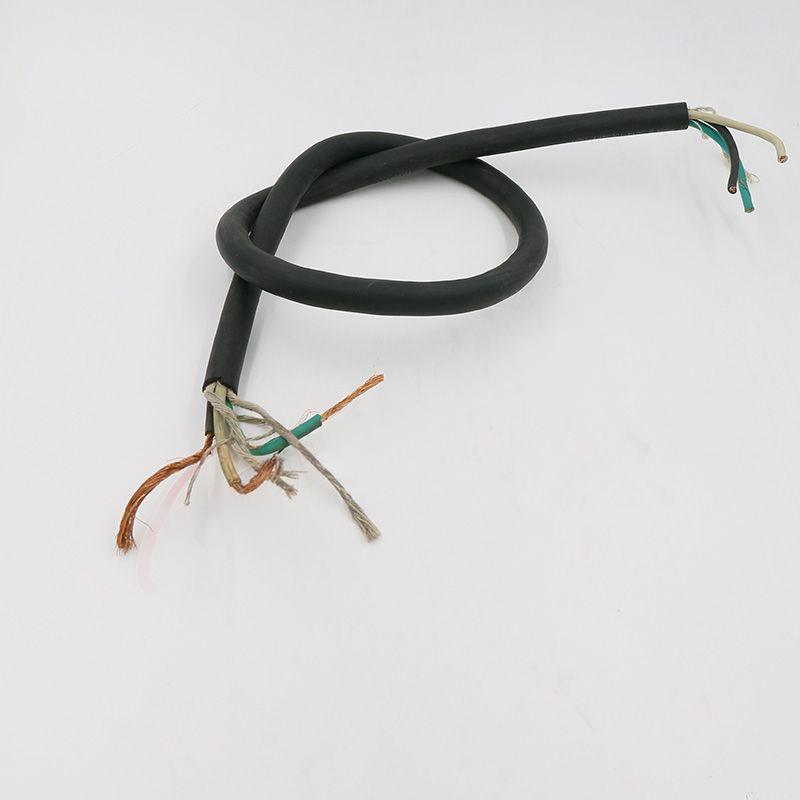
Industry professionals value the non-return ball valve for its simplicity and reliability. Unlike other types of check valves, such as swing or lift check valves, the ball valve is often chosen for applications where space is limited or where rapid shut-off is needed. Its compact design allows for easy installation and maintenance. Moreover, advancements in technology have led to models that reduce turbulence and wear, significantly boosting their lifespan.
Authoritativeness in the manufacturing and quality assurance of non-return ball valves cannot be overstated. Leading manufacturers subject these valves to rigorous testing, ensuring they meet industry standards such as API, ANSI, or ISO certifications. These standards are a testament to the quality and reliability of the valve, instilling confidence in end users that the valves will perform as expected under specified conditions.
non return ball valve
Trustworthiness in the operation of non-return ball valves is pivotal. In industries where fluid dynamics play a critical role, such as firefighting, pharmaceuticals, or HVAC systems, the assurance that the valve will function correctly without manual intervention is paramount. The use of non-return ball valves mitigates the risk of system failures, safeguarding machinery, protecting sensitive processes, and ultimately ensuring the safety of personnel and the public.
Real-world experience shows that the deployment of non-return ball valves can lead to significant cost savings. By preventing backflow, these valves help maintain pressure in the system, reducing the energy required for pumps and consequently lowering operational costs. Frequent issues such as reverse flow-induced water hammer or pressure surges are minimized, reducing wear and tear on pipelines and associated machinery and lessening the need for repair and maintenance.
Investment in high-quality non-return ball valves is an investment in reliability and performance. As industries continue to expand and innovate, the demand for robust, efficient fluid handling solutions will only grow. Choosing the right valve, backed by detailed performance data and a strong reputation for quality, can drive productivity improvements and ensure sustainable operations.
For businesses and industries at the cutting edge of technology, the adoption of non-return ball valves designed with the latest materials and technology represents not merely a purchase but a strategic initiative aimed at achieving seamless operations. By working closely with reputable manufacturers and suppliers, businesses can tailor solutions to meet specific needs, ensuring both short-term efficiency and long-term reliability.