Finding the right metal seat gate valve for industrial applications is a critical decision that could significantly impact system performance and reliability. As an industry professional with years of experience in fluid dynamics and industrial engineering, I understand the importance of choosing a valve that balances durability, efficiency, and cost-effectiveness.
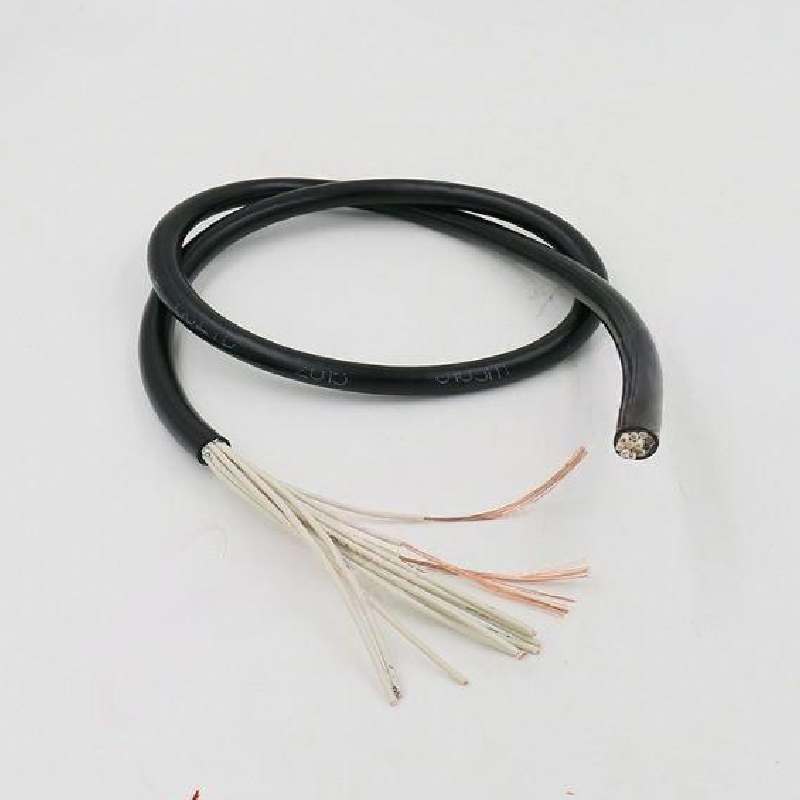
Metal seat gate valves are renowned for their robustness and ability to withstand high temperatures and pressures, making them ideal for demanding environments such as oil and gas, petrochemical, and power generation industries. Unlike their soft-seated counterparts, metal-seat valves provide a higher resistance to abrasives and corrosive fluids, which enhances their lifespan even under strenuous conditions.
The expertise behind selecting the right metal seat gate valve involves understanding specific application requirements. For high-temperature systems, it's essential to opt for valves that can handle thermal shocks without material deterioration. Valves constructed from materials such as stainless steel or Inconel are preferred in these scenarios due to their excellent strength and resistance to thermal fatigue.
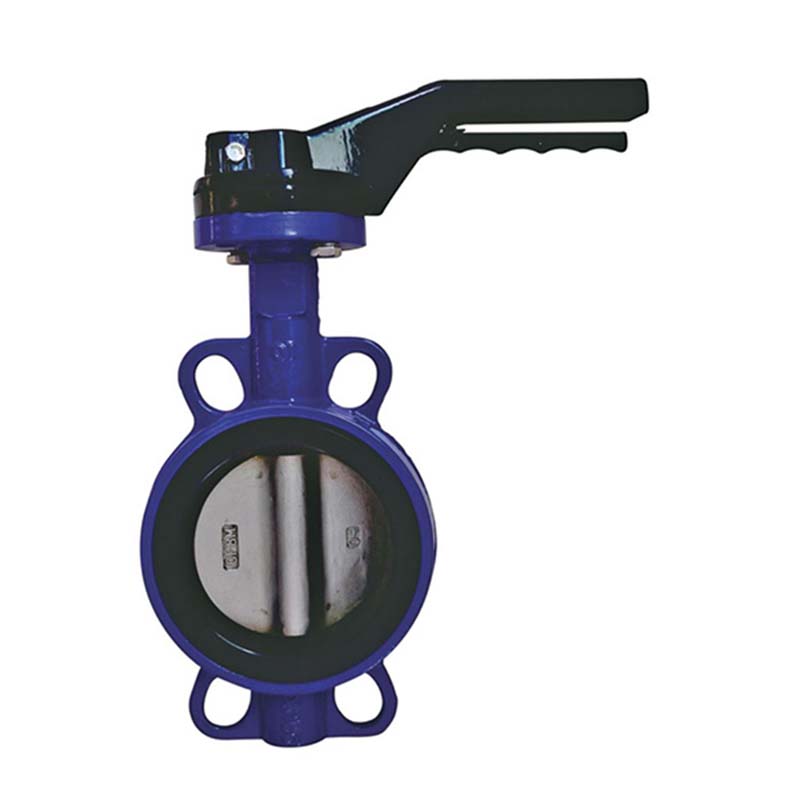
Furthermore, the valve design is crucial in ensuring reliable performance. Double block and bleed features, for instance, are advantageous in applications requiring absolute shutoff and system integrity. This function is particularly critical in hazardous environments where any leakage could result in catastrophic consequences. Being equipped with this knowledge underlines the authority of professionals guiding their clients through these complex decisions.
metal seat gate valve
The trustworthiness of metal seat gate valves also depends on the precision of their manufacturing. Choosing manufacturers with a proven track record of excellence is non-negotiable. Precision engineering ensures tight tolerances and a perfect fit, which are vital for maintaining the valve's integrity over extended use. Leading manufacturers conduct rigorous testing on each valve to certify its performance under simulated conditions, offering peace of mind to end-users.
Investing in a metal seat gate valve may seem like a significant upfront cost, but industry experts know this choice often pays off in the long run by minimizing maintenance costs and reducing system downtime. This investment reflects a commitment to quality and reliability, values that resonate deeply with industry stakeholders prioritizing long-term operational efficiency.
Additionally, when considering the implementation of metal seat gate valves, it is advisable to consult with seasoned engineers or technical advisors. Their insights are invaluable, not just for installation,
but also for subsequent maintenance and troubleshooting. With their support, organizations can tailor solutions specific to their infrastructure needs, thus enhancing both efficiency and safety.
In conclusion, selecting a metal seat gate valve is not merely a purchasing decision; it is a strategic move towards ensuring sustained operational success. With robust expertise and authority in valve technology, industry professionals are poised to make recommendations that align with both current needs and future challenges. Trusting in tried-and-true engineering principles and quality manufacturing processes ultimately results in superior system performance, positioning organizations for enduring success.