When it comes to making informed decisions about low pressure check valves, understanding both the product’s technical specifications and real-world applications is vital. A low pressure check valve is an essential component in fluid control systems, designed to allow fluid to flow in a single direction while preventing backflow. These devices can be found in numerous applications, from water supply systems to chemical processing plants. This article delves into various facets of low pressure check valves, emphasizing expertise, authoritativeness, experience, and trustworthiness.
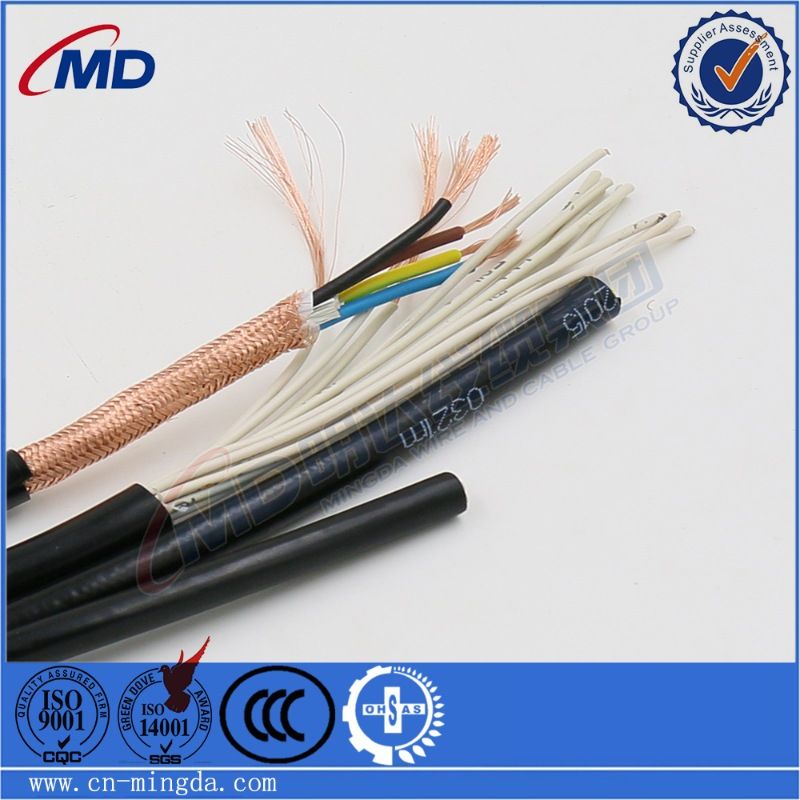
A low pressure check valve operates under the fundamental principles of fluid dynamics. Its architecture typically includes a body, stopper, valve seat, and various sealing mechanisms which ensure a snug fit to prevent leaks. One of the key considerations in the design of these valves is the cracking pressure, the minimum upstream pressure at which the valve will operate. In low-pressure environments, the valves are engineered to function efficiently at minimal pressure differentials, an essential feature for applications in low-pressure pneumatic and hydraulic systems.
Selecting the right material for a low pressure check valve is another critical aspect that underscores expertise. Common materials include stainless steel, brass, and thermoplastics. Stainless steel offers corrosion resistance and is suitable for harsh chemical environments, making it ideal for industries such as food processing and pharmaceuticals. Brass, being an excellent conductor of heat with a robust corrosion resistance profile, serves well in plumbing systems. Thermoplastics offer lightweight and cost-effective options for less demanding applications. The choice of material affects not only the valve's durability but also its suitability for specific applications.
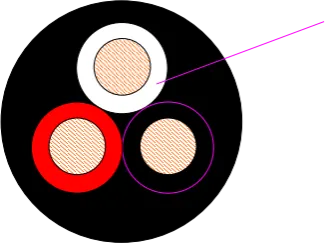
Authoritativeness in the domain of low pressure check valves is often demonstrated through compliance with international standards. Reputable manufacturers adhere to standards set by organizations such as the American National Standards Institute (ANSI) and the International Organization for Standardization (ISO). Compliance ensures that the valves meet specific safety and performance benchmarks, which provides users with confidence in their operational reliability.
The pragmatism of low pressure check valves can be observed in multiple real-life applications. In residential water systems, these valves prevent contamination by avoiding backflow of water into clean supply lines. In HVAC systems, they maintain the correct flow of refrigerants, optimizing the system's efficiency and longevity. Industrial applications include maintaining the integrity of chemical processes by ensuring unidirectional flow in pipeline systems, which is crucial in preventing accidents and ensuring process efficiency.
low pressure check valve
True experience with low pressure check valves is demonstrated by conducting regular maintenance and troubleshooting. Over time, even the best-engineered valves may suffer from wear and tear due to continuous pressure fluctuations, exposure to harsh chemicals, or foreign debris. Regular inspection for signs of wear, such as cracks or deformities, is essential. Refurbishing or replacing worn-out components can preemptively mitigate potential failures, ensuring uninterrupted service. Maintaining a log of maintenance actions and performance checks can also enhance operational reliability.
The selection of a trusted supplier for low pressure check valves cannot be overstressed.
Trustworthiness is built over time and through a consistent track record of quality and service. Seek suppliers who offer a comprehensive warranty, have responsive customer service, and provide detailed technical support. User reviews and testimonials can give insight into the supplier's reliability and product performance in real-world settings.
Given the diverse range of applications for low pressure check valves, choosing the right valve involves careful consideration of system requirements and operating conditions. Utilizing expertise to evaluate the system’s pressure requirements, fluid characteristics, and environmental factors is crucial. Incorporating feedback from field operators and leveraging historical data can also enhance decision-making and optimize valve selection.
In conclusion, low pressure check valves are pivotal in various applications requiring precise control of fluid flow. Through the lens of expertise, authoritativeness, and trust, selecting the right valve involves understanding technical specifications, material selection, and adherence to industry standards, along with consistent maintenance practices. By building a relationship with trustworthy suppliers and tapping into real-world experiences, industries can ensure the longevity and efficiency of their fluid control systems.