Industrial valves are fundamental components in a myriad of sectors, playing a pivotal role in regulating the flow of fluids and gases in various applications. Companies and industries around the world depend heavily on these devices to ensure safety, efficiency, and operational integrity. With technological advancements and an ever-increasing demand for automation, the spotlight on industrial valves shines brighter than ever.
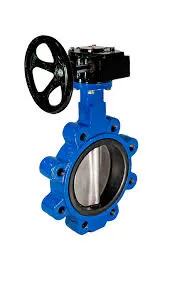
In an era where efficiency and precision are non-negotiable, industrial valves provide unmatched expertise in fluid control and management. By executing critical functions such as isolation, throttling, and non-return flow, these valves contribute significantly to the optimization of industrial processes. For instance, in petrochemical industries, where the margin for error is minimal, the correct choice and maintenance of industrial valves can mean the difference between smooth operations and potentially costly mishaps.
Industrial valves come in various types, including gate valves, globe valves, ball valves, butterfly valves, and check valves. Each type offers unique features suitable for specific purposes, highlighting the need for expertise in selecting the right valve for the task at hand. For example, ball valves are renowned for their durability and excellent shut-off capabilities, proving invaluable in applications where tight sealing is crucial. On the other hand, butterfly valves offer a lightweight, cost-effective solution with quick operation benefits, making them ideal for conditions requiring frequent valve actuation.
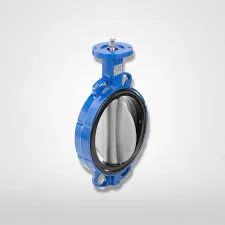
Authoritativeness in the industrial valve sector is built through decades of innovation and proven performance. Leading manufacturers like Emerson, Flowserve, and Cameron leverage cutting-edge technology to produce valves that meet stringent global standards and certifications. These companies invest heavily in research and development, constantly pushing the boundaries of valve design and functionality. Advanced materials and coatings are now utilized to enhance valve performance under extreme conditions, such as high temperature and corrosive environments. Expertise from such industry leaders ensures that the valves not only comply with international specifications but often exceed industry benchmarks, providing reliability and peace of mind to their users.
industrial valve
Safety and reliability are paramount, and manufacturers have robust systems in place to ensure the trustworthiness of their products. Rigorous testing procedures, which include hydrostatic, pneumatic, and life cycle testing, guarantee that every valve can withstand the operational stresses it is subjected to. Additionally, digital technologies, such as predictive maintenance systems, are increasingly being integrated into valve solutions. These systems enable real-time monitoring and diagnostics, allowing for proactive maintenance and reduction in unexpected downtimes.
Real-world experience shared by industry professionals illustrates the importance of valve selection and application. For example, in a case study involving a chemical manufacturing plant, the implementation of high-performance butterfly valves resulted in significantly reduced leakage, decreased maintenance costs, and enhanced process efficiency. Such experiences are not isolated; they echo across various industries, from water treatment facilities to power generation plants, underscoring the economic and operational advantages that well-chosen valves bring.
In environmentally sensitive projects, the role of valves becomes even more critical. Valves designed with environmental considerations ensure minimal emissions and leakages, aiding eco-friendly operations and compliance with environmental regulations. Zero-leakage valves, in particular, are gaining traction as industries strive to reduce their carbon footprints and contribute to sustainability goals.
In conclusion, industrial valves are indispensable in modern industrial operations, offering unparalleled expertise in flow management and operational efficiency. Their role in industrial automation and safety cannot be understated, while advancements in technology continue to elevate their capabilities. Trust in these components is bolstered by authority figures within the industry, whose expertise ensures that these valves are robust, reliable, and ready to meet the challenges of tomorrow’s industrial landscape. Whether through the lens of cost-effectiveness, precision, or environmental stewardship, industrial valves remain a cornerstone of industrial success.