Industrial valves are integral components in diverse fields, from oil and gas to water treatment and beyond. As an industry expert with extensive hands-on experience, I can assert that choosing the right industrial valve can significantly enhance operational efficiency, safety, and reliability.
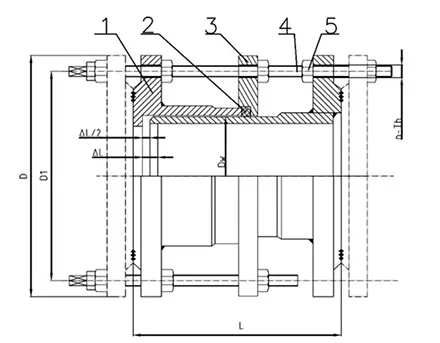
Having worked closely with a myriad of industrial set-ups, one of the foremost insights is the importance of understanding your system requirements before valve selection. Not all valves are created equal; their applications can vastly differ. Industrial valves serve various functions such as flow regulation, pressure control, and direction management of liquids, gases, and slurries within a pipeline system.
Butterfly valves, for instance, are preferred in scenarios where space is constrained. Their compact design and minimal weight make them ideal for applications where quick shutoff is necessary. However, with a relatively low-pressure drop, they may not be suitable for high-pressure scenarios, unlike globe valves, which are excellent for precise throttling.
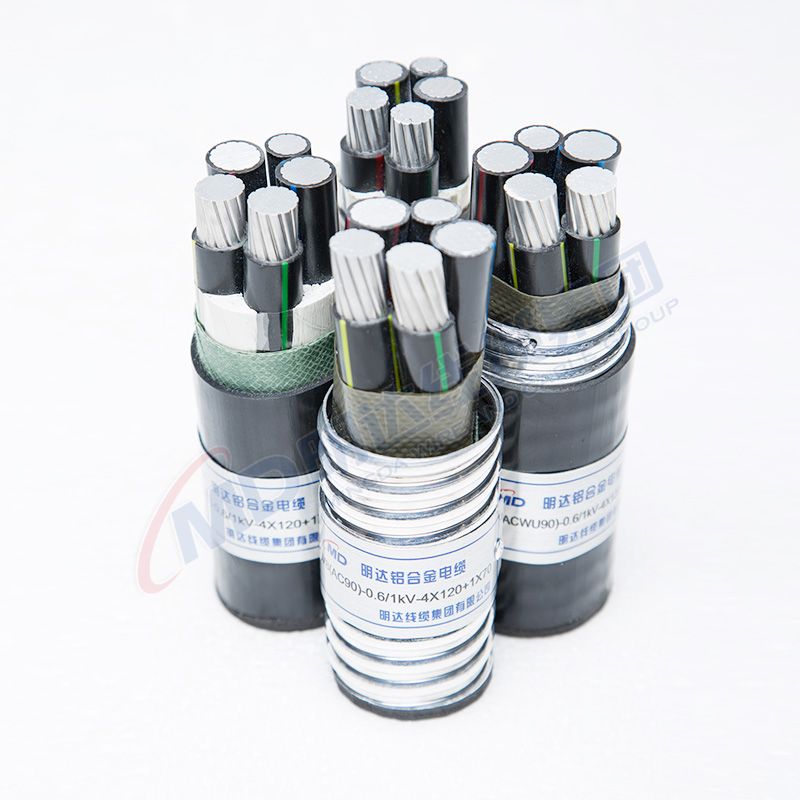
Ball valves, characterized by their spherical disc operation, are renowned for offering a perfect seal. This makes them a staple in industries that handle corrosive and toxic substances, offering reliable isolation with minimal leakage. My field experience suggests that while ball valves are durable, their maintenance, particularly for large diameters, should never be overlooked to prevent operational hiccups.
In terms of specialized application, solenoid valves emerge as champions in automated systems. With their electromagnetic operations, they provide precise control over fluid and gas flow in minimal timeframes, making them suitable for applications that require frequent cycle times. However, expertise in electrical systems is necessary for installation and troubleshooting, thereby emphasizing the importance of having trained personnel.
industrial valve
Expertise in valve material selection is also crucial when addressing corrosion and temperature challenges. Stainless steel valves are typically used in industries where corrosion is a significant concern, while brass and PVC valves may be adequate for less demanding environments such as water management systems.
From a sustainability viewpoint, incorporating smart valves with IoT capabilities is becoming increasingly popular. These valves enable real-time data collection and remote monitoring, optimizing system performance and predicting maintenance needs. As I have emphasized in several implementations, this leads to cost savings and enhances system longevity through predictive maintenance strategies.
Establishing authority in valve management relies heavily on an ongoing commitment to innovation and understanding sector advancements. Attending industry conferences and engaging in continuous professional development ensures you remain at the cutting edge, aware of trends such as energy-efficient valve solutions and regulatory changes.
Trustworthiness in industrial valve provision is fortified by transparency and clarity in communication. As part of best practices, manufacturers and distributors should provide detailed specifications and robust after-sales support. Field experience reinforced this notion clients consistently seek partners who not only supply products but also offer comprehensive lifecycle management services.
In conclusion, the industrial valve landscape is dynamic and integral to the core functionalities of numerous systems. Through refined expertise and hands-on experience, one can adeptly navigate the challenges of valve selection and system integration. Establishing oneself as an authority in this field is achieved through a blend of innovation, continuous learning, and a commitment to delivering trustworthy solutions tailored to client needs.