In the intricate world of fluid control systems, the industrial globe valve stands as an essential component with an impressive track record of reliability and performance. For industries ranging from petrochemicals to manufacturing, the globe valve is celebrated for its versatility and precision in regulating flow. This article delves into the distinctive features, applications, and advantages of industrial globe valves, providing a comprehensive guide for professionals seeking expert insights.

Industrial globe valves are primarily used to start, stop, and regulate the flow of a fluid. The valve contains a movable disk-type element and a stationary ring seat in a generally spherical body. This design gives the globe valve its superior throttling capability, making it ideal for applications where flow control and leak tightness are critical.
Experience reveals that choosing the right globe valve can significantly influence the efficiency and safety of a pipeline system. Among the key features that make globe valves a preferred choice is their ability to handle high-pressure drops with minimal leakage. The practicality of a globe valve is further evidenced by its robust design, which typically includes a yoke that allows for easy actuation through manual, electric, or pneumatic operators.
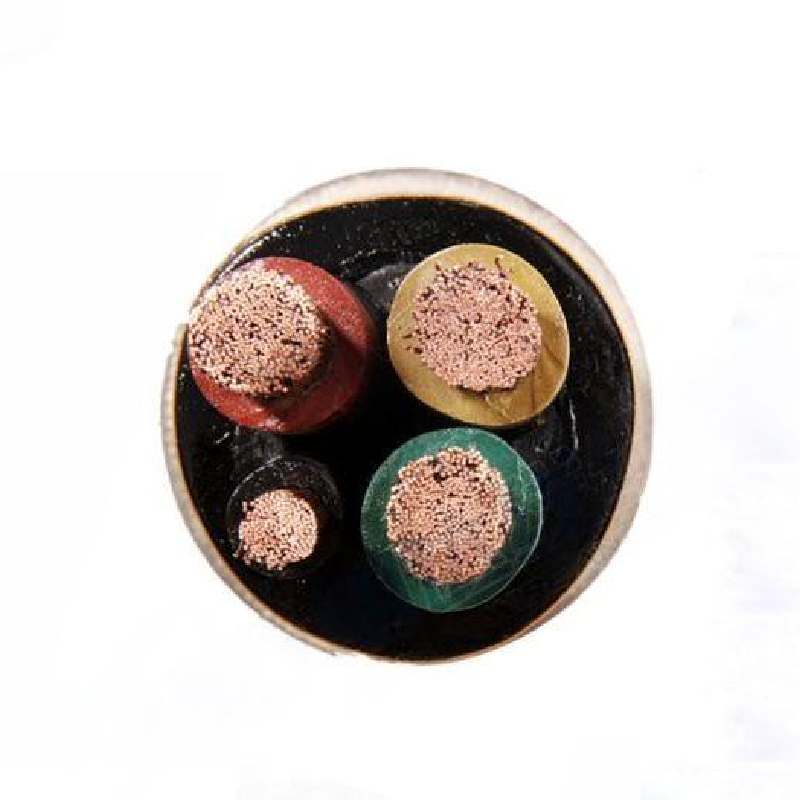
One of the primary reasons industries favor globe valves is their reliability in scenarios that demand frequent operation and low-maintenance solutions. The valve's distinct linear motion operation contributes to its longevity and dependability, as the actuation process does not require excessive force, reducing wear over time. This becomes particularly important in settings like power plants or refineries, where valve failure can lead to significant downtime and economic losses.
From an engineering perspective, globe valves come in various types, such as Tee, Wye, and Angle types, each suited for different piping configurations and operational needs. The Tee pattern provides a higher resistance to flow, which is beneficial for precise throttling applications. Wye pattern globe valves are designed for high-pressure applications, offering a straighter flow path with minimal pressure drop. Meanwhile, angle pattern globe valves serve well in corner installations where pipelines intersect at 90-degree angles, saving space and reducing the need for additional fittings.
industrial globe valve
Expertise in material selection is crucial for maximizing the functionality and lifespan of a globe valve. Common materials used include stainless steel, cast iron, and various bronze alloys, each offering unique advantages in terms of corrosion resistance, temperature tolerance, and structural integrity. For example, stainless steel is ideal for corrosive environments, while cast iron offers cost-effective solutions for less demanding conditions.
In terms of authoritativeness, it’s essential to recognize that the success of a globe valve in industrial applications hinges on proper sizing and installation. Incorrect sizing can lead to inefficient valve operation and energy losses, while incorrect installation may cause leakage and early wear. Therefore, consulting with valve specialists during the design phase of a project ensures optimal performance and adherence to industry standards.
Trustworthiness in the use of globe valves is also reaffirmed by adherence to stringent quality assurance practices during manufacturing. Leading manufacturers implement rigorous testing protocols, including pressure testing, material certification, and compliance with international standards such as ASME B16.34 and API 623. These measures ensure that each valve delivers consistent performance even under the most challenging conditions.
Ultimately, the choice and implementation of an industrial globe valve can determine the success of a fluid management system. It's not merely about selecting a valve but understanding its role within a complex interplay of pipeline dynamics, pressure, temperature, and flow requirements. By leveraging the globe valve's versatile capabilities and ensuring meticulous compliance with technical standards, professionals can enhance both the efficiency and reliability of their fluid control systems.
For industries that demand precision, durability, and performance, the industrial globe valve remains an irreplaceable component. Whether used in chemical manufacturing or oil and gas exploration, its well-documented reliability and functionality continue to earn the trust of engineers and operators worldwide. Through expert knowledge and thoughtful application, globe valves will undoubtedly continue to play a pivotal role in advancing industrial fluid handling technologies.