Industrial check valves are crucial components in various sectors, including oil and gas, water treatment, and manufacturing. Their primary function is to ensure fluid flows in only one direction, preventing backflow that could damage equipment or disrupt operations. Understanding these devices requires a comprehensive exploration of their design, applications, and benefits.
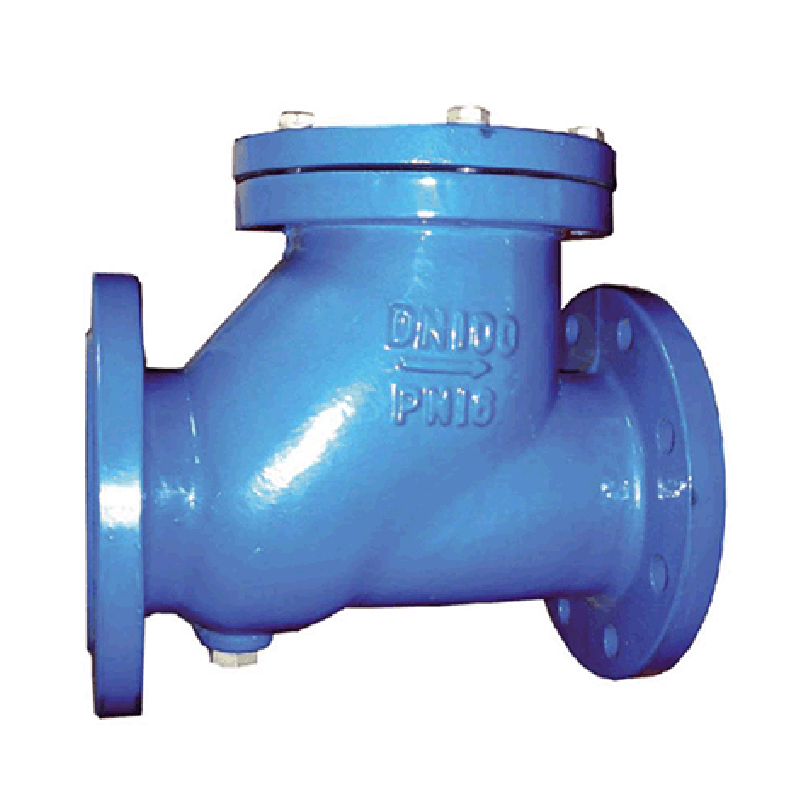
Check valves, often underappreciated, play an indispensable role in maintaining the integrity of fluid systems. Their unidirectional flow feature is critical in preventing contamination, maintaining pressure, and promoting efficient operation of complex mechanical systems. These valves are direction-sensitive, ensuring that once the fluid passes through, it can't reverse, safeguarding against potential equipment failures.
Industrially, check valves come in various types, each tailored for specific applications. Swing check valves, for instance, use a swinging disc to permit or block flow and are ideal in situations where full flow is essential with minimal pressure drop. They are particularly useful in water supply systems and large-scale industrial processes where fluid dynamics must be carefully managed.
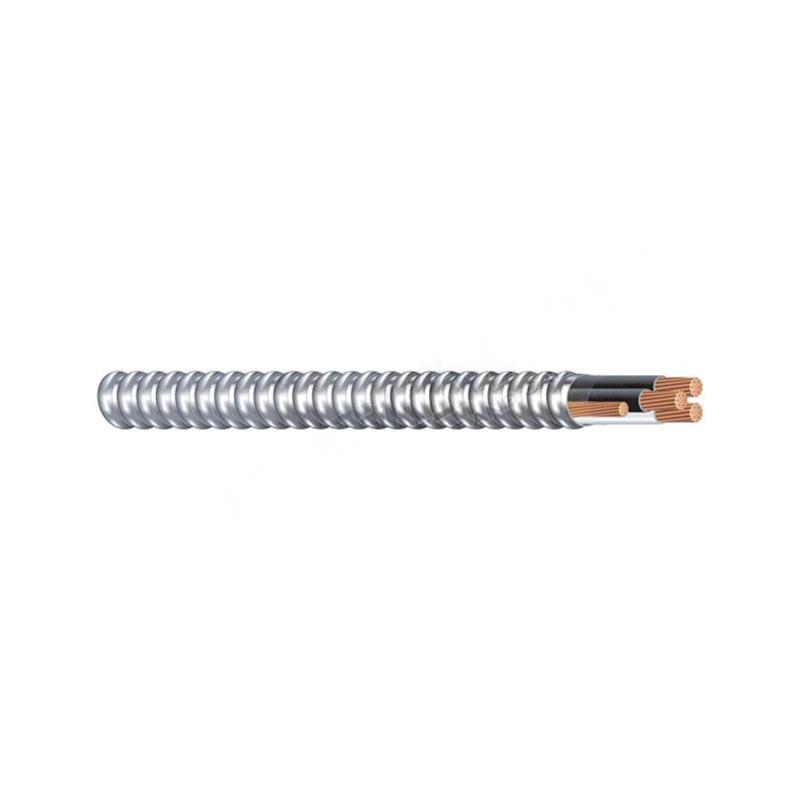
In contrast, lift check valves operate by opening or closing a disc that moves along a guided path, suitable for high-pressure applications. These are typically found in petroleum refining and chemical manufacturing due to their robustness and efficiency in high-stress environments.
One notable variant is the ball check valve, which uses a spherical ball to block reverse flow. This type is renowned for its simple design and effectiveness in systems where low-pressure drops are crucial. They are commonly used in the slurry or viscous fluid systems found in mining or wastewater treatment facilities.
industrial check valve
The materials used in manufacturing industrial check valves vary depending on their application. Stainless steel, for instance, is prized for its resistance to corrosion and durability under extreme temperatures or pressures. Engineers often select materials based on compatibility with the fluid media and the valve's operating conditions, ensuring longevity and reliability.
From an engineering perspective, selecting the appropriate check valve requires an understanding of the system's operational demands. Flow rate, pressure, temperature, and the nature of the fluid all influence the ideal choice. Experts advocate for a thorough assessment of these factors to maintain system efficiency and prevent costly downtime due to improper valve selection.
Reliability and maintenance are also crucial considerations. Industrial check valves must be meticulously designed to withstand rigorous operating conditions with minimal maintenance intervention. Advanced technologies and materials have been developed to enhance the durability and performance of these valves, ensuring they meet the stringent demands of modern industrial applications.
Trust in reputable manufacturers is fundamental, as their expertise ensures adherence to industry standards and regulations. Choosing a valve from a recognized leader in the field not only assures quality and performance but also guarantees support and service that protects long-term investments.
In conclusion, industrial check valves are the unsung heroes of many mechanical systems, requiring careful consideration in their selection and application. Their design, materials, and operation must align with system requirements to ensure optimal performance. Engaging with manufacturers and relying on engineering expertise enhance the trustworthiness and longevity of these essential components. With the right choice, industries can improve operational efficiency, safeguard system integrity, and secure the seamless flow of processes.