In the intricate world of flow management within industrial applications, the industrial check valve plays a pivotal role. These dynamic components are integral to ensuring the efficiency and safety of fluid control in various sectors. A deep dive into the functionality, necessity, and selection of industrial check valves offers a profound understanding that aligns with key SEO strategies focusing on experience, expertise, authoritativeness, and trustworthiness.
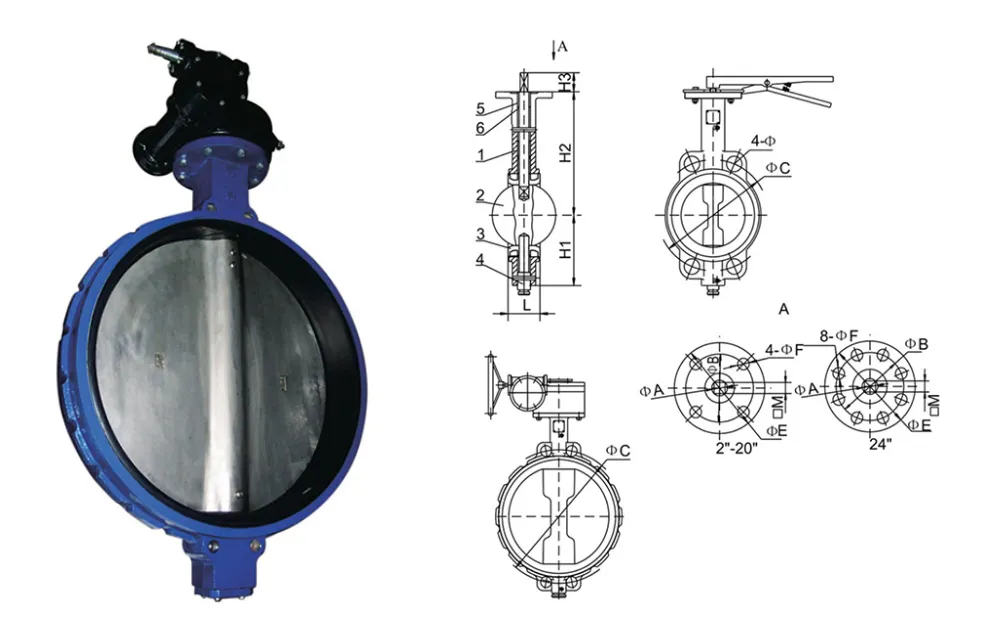
Industrial check valves, often unheralded, serve as silent sentinels in piping systems, designed to allow fluid to flow in one direction while preventing backflow. This one-way mechanism is essential across industries ranging from oil and gas to water treatment facilities. The importance of these valves becomes apparent when evaluating their impact on operational continuity and safety. Case studies within the oil industry reveal that malfunctioning check valves can lead to system failures, causing costly downtime and environmental hazards. Thus, the expertise in selecting the appropriate type of check valve—whether it be swing, lift, or ball check valve—is paramount.
Expertise in this domain requires a thorough knowledge of varying operational conditions. Each application demands careful consideration of valve materials, pressure ratings, and compatibility with the medium being transported. For instance, in corrosive environments, valves crafted from stainless steel or special alloys might be essential to withstand aggressive agents. Ensuring the longevity and performance of a check valve in such settings demonstrates not only product expertise but also an authoritative understanding of industrial standards and materials science.
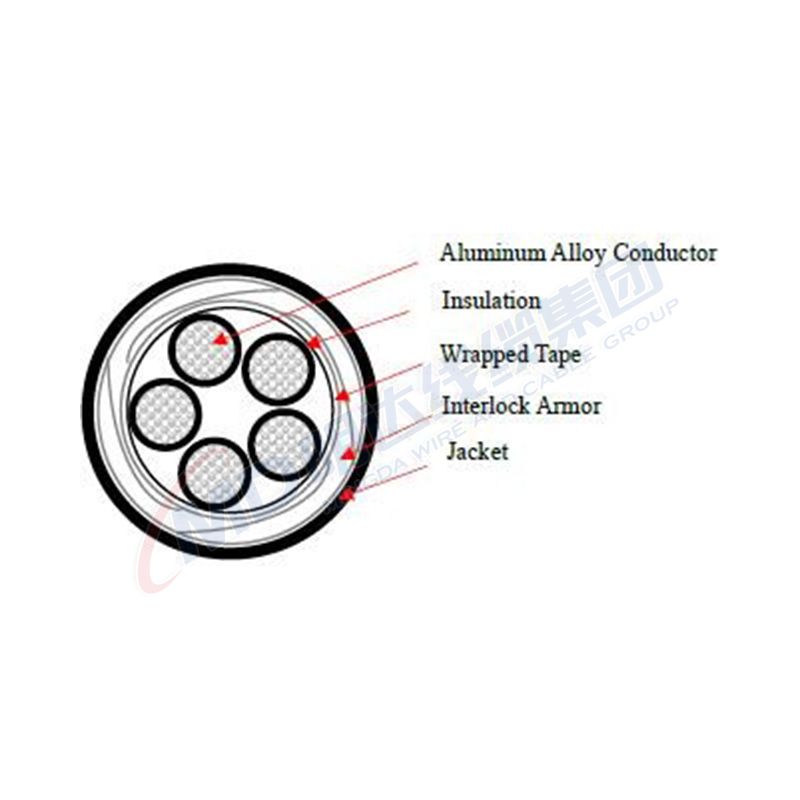
Furthermore, the authoritative nature of using check valves is underscored by adhering to industry standards such as those set by the American Petroleum Institute (API) or the American National Standards Institute (ANSI). Compliance with these benchmarks is crucial, reflecting a commitment to safety and quality. Installations adhering to these standards often enjoy extended operational life and reduced maintenance costs, reinforcing the trustworthiness of the systems they support.
industrial check valve
Real-world experiences further cement the value of industrial check valves. Plant managers and engineers often share success stories of reduced system maintenance and increased reliability after integrating high-quality check valves into their systems. These narratives, rooted in tangible outcomes, not only provide insight into the benefits but also build trust with potential clients exploring these options for their operations.
A recurring theme in discussions with experienced industry professionals is the critical role of maintenance and regular inspection. Neglecting these aspects can result in valve failures, causing unnecessary complications in system operations. Thus, the trustworthiness of any check valve solution is inherently tied to the expertise not only in selection but also in the production of supporting maintenance documentation and customized aftercare programs.
The decision matrix for choosing the right check valve must weigh cost-efficiency against performance metrics and safety considerations. Advanced computational fluid dynamics (CFD) software now aids in simulating valve operation within specific conditions, offering a scientific approach to valve selection. Such tools highlight the intersection of technology with traditional engineering, showcasing the evolution and adaptability of valve solutions.
In conclusion, the industrial check valve is more than a mere component—it is a cornerstone of fluid management that embodies expertise, authority, and trust. By choosing a check valve solution that meets rigorous industry standards and tailoring choices to specific application needs, businesses can mitigate risks, enhance system safety, and ensure a smooth, efficient operation.
As industries continue to advance, the role of reliable and expertly chosen check valves remains as significant as ever.