When it comes to ensuring optimal fluid control in industrial systems, the groove check valve is an indispensable component. As someone with extensive experience in the field of fluid dynamics and valve technology, I am keenly aware of the intricacies involved in selecting and maintaining these essential devices to guarantee peak performance and reliability.
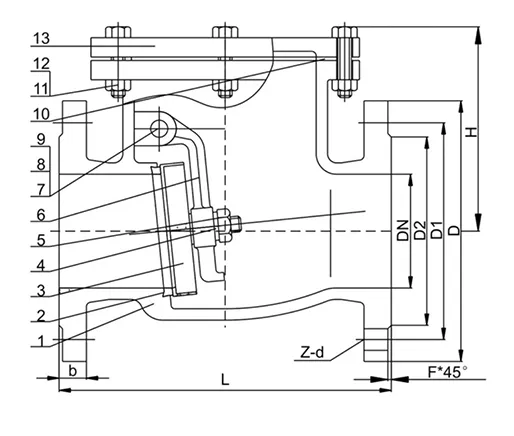
Groove check valves are specifically designed to prevent the backflow of fluids in a pipeline, providing a crucial safety mechanism that protects pumps, compressors, and other critical machinery. Unlike traditional check valves, groove check valves offer a simplified installation process, thanks to their grooved coupling ends. This innovative design allows for quick and secure assembly, reducing the time and labor costs associated with valve installation and maintenance.
The expertise behind groove check valves lies in their engineering. These valves typically feature a robust disc or swing mechanism that responds promptly to changes in fluid pressure, ensuring that flow direction is maintained effectively. The materials used in the construction of groove check valves are chosen for their durability and resistance to corrosion, which is vital for prolonged operation in harsh industrial environments. Common materials include stainless steel, ductile iron, and high-grade polymers, each selected based on the specific requirements of the application.
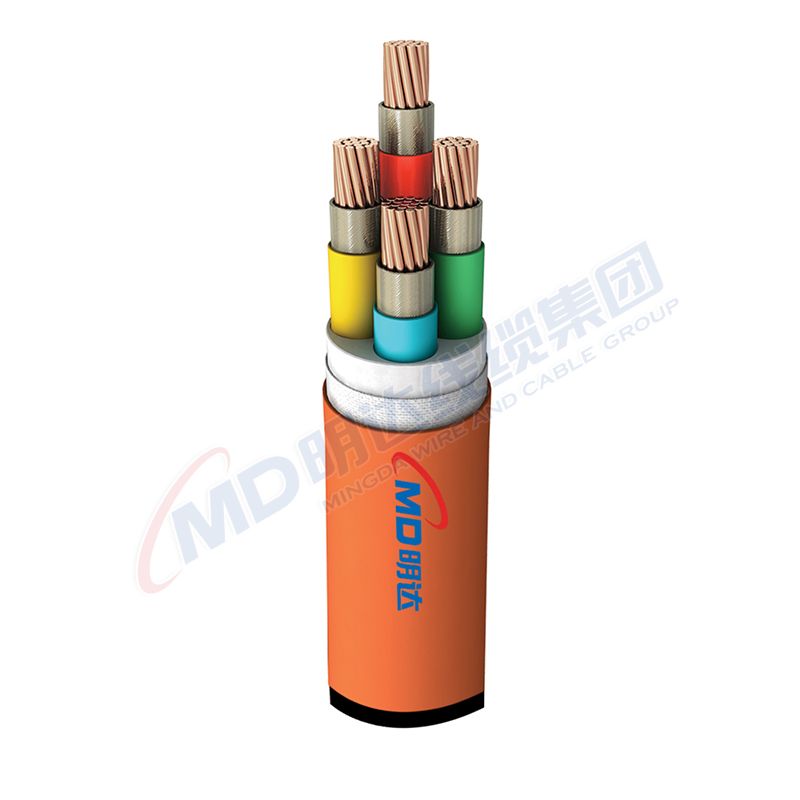
Authoritativeness in the realm of groove check valves can be substantiated by data from field tests and peer-reviewed studies. Such evidence consistently highlights the efficacy of these valves in reducing water hammer effects, a common issue caused by sudden changes in fluid flow that can lead to pipeline damage. Additionally, the low-pressure drops associated with groove check valves contribute to energy savings, which is a significant consideration for operations looking to improve efficiency and reduce operational costs.
groove check valve
Furthermore, the trustworthiness of groove check valves is reinforced by adherence to international standards and certifications. Manufacturers often subject these valves to rigorous quality control processes and testing, ensuring compliance with industry regulations such as ASME, ISO, and API standards. Users, therefore, have the assurance that their systems are safeguarded by components that meet the highest levels of safety and performance.
In practice, the selection of a groove check valve should be guided by specific application requirements such as fluid type, system pressure, and temperature range. Consulting with professionals who have a deep understanding of fluid systems and valve technology is crucial to make informed choices. These experts can provide invaluable insights into compatibility and longevity, helping ensure that the valve integrates seamlessly into existing infrastructure while delivering expected performance outcomes.
To maximize the lifespan and functionality of groove check valves, regular maintenance and inspections are recommended. Routine checks can identify wear and tear or potential malfunctions before they escalate into major issues, thereby preventing costly downtime.
Ensuring proper alignment and lubrication of moving parts is also essential to preserve the valve's operational integrity over time.
In summary, groove check valves offer a blend of simplicity and functionality, making them a favored choice in various industrial applications. Their ease of installation, coupled with their engineered resilience against demanding operational conditions, make them a reliable component in fluid control systems. By leveraging the expertise and authoritative insights available in the industry, and prioritizing trust and standards compliance, organizations can enhance the efficiency and safety of their operations with the integration of groove check valves.