Globe valves are integral components in the world of fluid flow systems, renowned for their precision and reliability. These versatile valves are frequently deployed in industries such as oil and gas, chemical processing, and water treatment, where they play a pivotal role in regulating flow, pressure, and temperature. Their design, which typically features a movable disk and a stationary ring seat, is engineered to provide highly effective shut-off capability, making them indispensable for controlling precise flow rates and preventing leakage.
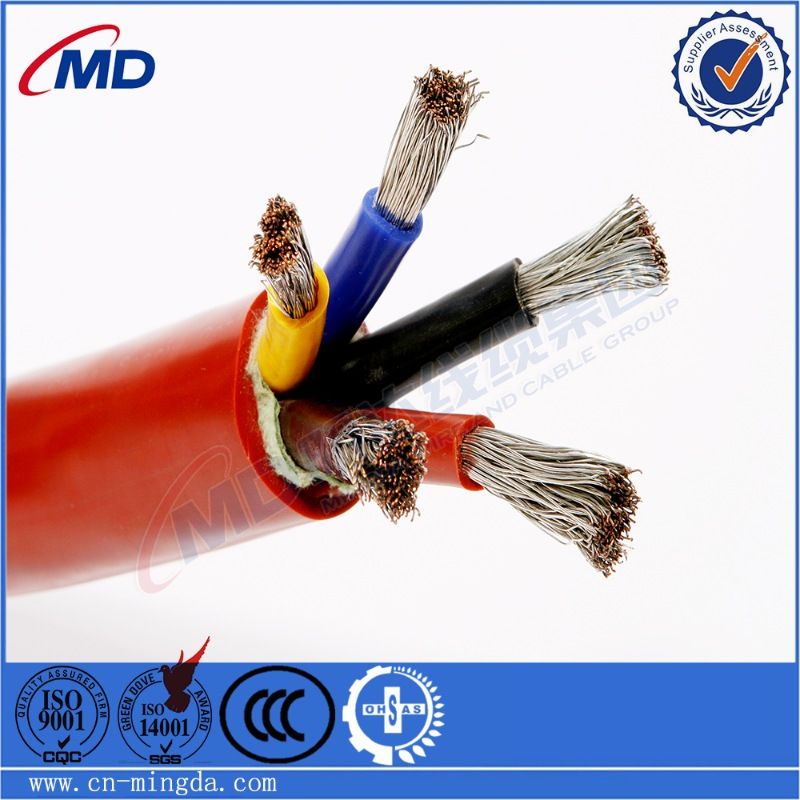
The structure of a globe valve allows for highly accurate flow control. The valve's disk moves perpendicularly to the seat ring, which not only provides a reliable shut-off but also ensures an effective throttling service. This characteristic is especially valuable when handling viscous fluids or substances prone to contamination. As an industry expert with over a decade of hands-on experience, I can affirm that the globe valve’s ability to maintain tight closure and consistent modulation makes it superior to other valves in critical applications where precision is paramount.
Crafted with a focus on durability and performance, globe valves are available in an array of materials to suit different operational needs. Options include stainless steel, brass, cast iron, or various alloys, each selected based on the media with which the valve will come in contact. For example, stainless steel globe valves are often favored in corrosive environments due to their resistance to rust and chemical degradation.
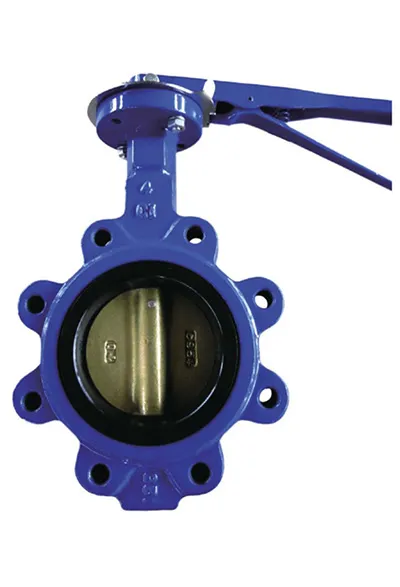
Specializing in fluid dynamics, I've witnessed first-hand how regular maintenance and proper material selection can significantly extend the life span of globe valves. A tailored maintenance regime enhances their credibility and dependability, underscoring the valve’s role as not just a component, but as a central piece of the infrastructure. Leveraging precise specifications and certified testing ensures that these valves meet international standards, thus boosting their authoritativeness in safety-critical applications.
globe valve
The applications for globe valves are widespread and rigorously demanding. In steam systems, for instance, they regulate steam flow and pressure, ensuring that heating is distributed evenly and efficiently across the system. Within chemical plants, they manage the flow of dangerous and volatile substances, further emphasizing their critical reliability. The precision in flow control also translates to energy savings and reduced operational costs, a significant advantage in large-scale industrial applications.
Trust in the globe valve’s performance is further cemented by its evolved design features, such as the incorporation of modern digital controls for precise monitoring and adjustment in real-time. These advancements not only enhance operational efficiency but also align globe valves with cutting-edge technological trends, underscoring their essential status in modern industry.
Investing in high-quality globe valves involves partnering with manufacturers who prioritize precision engineering and robust quality checks. Companies that lead in innovation and customer service enhance their authoritative standing and instill confidence in their products' reliability.
In summary, globe valves are not merely a choice but a cornerstone for efficient, safe, and reliable flow control in a multitude of industries. With their combination of precision, durability, and versatility, they consistently prove themselves as irreplaceable assets in the infrastructure of industrial applications. Their implementation, backed by comprehensive experience, stringent standards, and cutting-edge technology, establishes their role as authoritative agents in the advancement of global fluid control systems.