Globe valves, widely recognized for their precise control capabilities and robust construction, have become an integral component in various industrial applications. Their unique design, characterized by a movable disk and a stationary ring seat housed in a spherical body, allows them to effectively regulate flow, making them indispensable in the control of liquid and gas flow in pipelines.
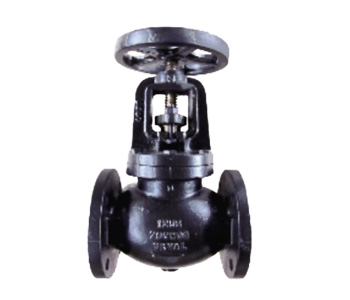
In industry practice, the selection of a globe valve is often guided by its ability to deliver exceptional control precision and durability. A veteran expert in industrial fluid dynamics would concur that the mechanism of a globe valve, which involves a linear motion to throttle flow, provides superior throttling capabilities compared to other valve types. This is due to the proportionate relationship between the valve position and the flow rate, which allows operators to achieve precise flow control essential for processes sensitive to flow variations.
When considering the expertise involved in operating globe valves, it is crucial to recognize the impact of design specifics on valve performance. For instance, in applications where minimizing pressure drop is of paramount importance, opting for a Y-pattern globe valve, which offers a straighter flow path, can be beneficial. The proficiency required in selecting the correct globe valve type, whether it be Z-pattern or angular, is testament to the valve's complexity and the necessity for specialist knowledge to optimize system performance.
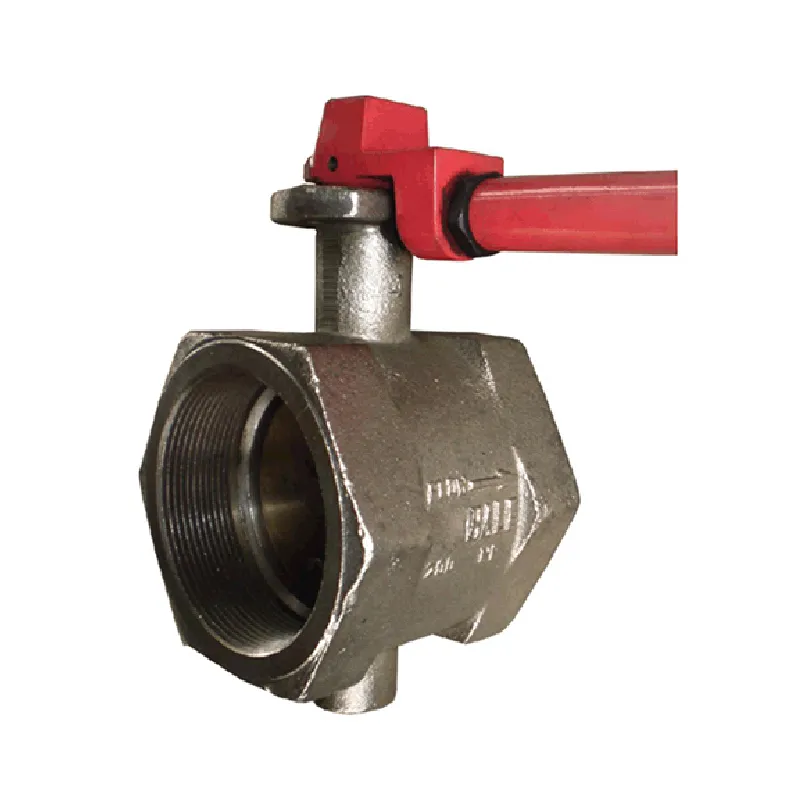
Authoritativeness in the sphere of globe valves is often demonstrated through adherence to industry standards and certifications, which affirm the valves' reliability and operational efficiency. Manufacturers that uphold certifications such as ISO 9001 for quality management, or API 6D for pipeline valves, underline their commitment to producing high-performance globe valves that meet rigorous technical benchmarks. This assurance of quality and conforming to international standards is a key factor in building trust with clients who demand valves that withstand challenging operational environments.
globe valve
Additionally, the choice of materials in globe valve construction significantly enhances their operational trustworthiness. Materials such as stainless steel, which offer excellent resistance to corrosion, or high-performance alloys engineered to withstand extreme temperatures and pressures, significantly extend the life and functionality of globe valves.
This not only ensures optimal performance in harsh conditions but reinforces user confidence in the valves' long-term reliability.
Real-world applications and user experiences further substantiate the importance and effectiveness of globe valves. For instance, chemical processing plants rely heavily on these valves due to their ability to precisely regulate the flow of potentially hazardous fluids, ensuring safety and process stability. Similarly, in power plants, globe valves play a crucial role in controlling steam and feedwater flows, where any deviation can impact energy efficiency and safety. These applications highlight the valves' versatility and the critical role they play in maintaining operational integrity across diverse sectors.
In summary, the selection and application of globe valves require a blend of comprehensive knowledge, adherence to established standards, and insightful analysis of operational requirements. Their proven reliability and precise flow control abilities make them a trusted choice across various industrial sectors, underscoring their indispensability in facilitating safe, efficient, and reliable operations. As industries continue to advance, the expertise and authoritative knowledge surrounding the optimal use and integration of globe valves will remain a cornerstone of fluid control management.