Globe valves have become indispensable components in various industrial applications due to their robust design and exceptional control capabilities. These valves excel in regulating flow, offering precision and stability that other types may not provide. Understanding their core functionalities and advantages is crucial for industries ranging from chemical processing to power generation.
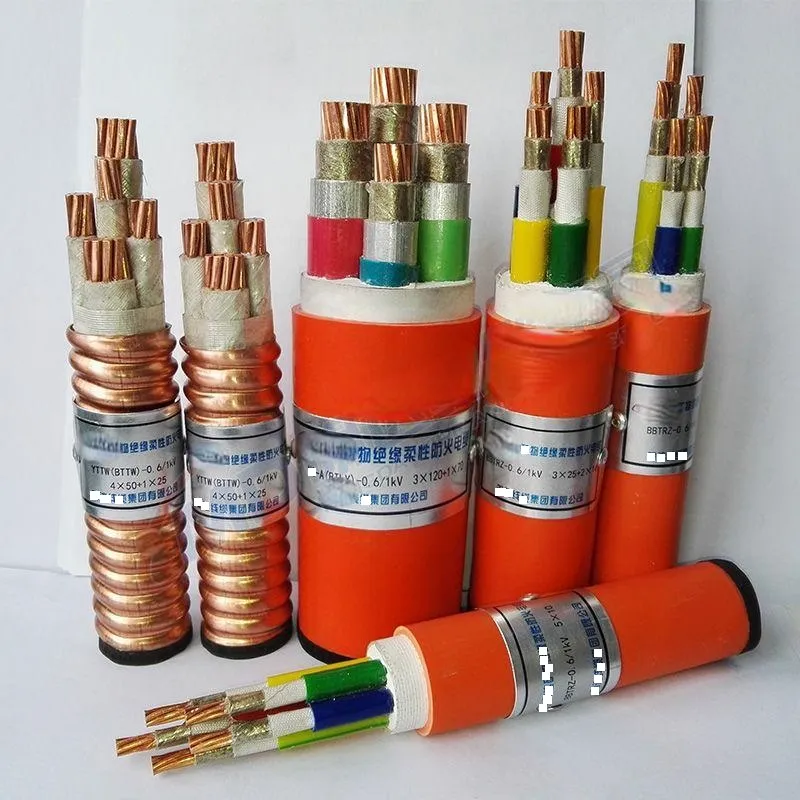
In industries where the precise regulation of fluid flow is critical, globe valves stand out due to their unique design, involving a movable disk and a stationary ring seat in a generally spherical body. This structure allows for linear motion necessary for throttling and isolation, offering unparalleled control over fluid flow. Unlike gate valves, which are primarily used for isolation, or ball valves that are better suited for quick shut-off functions, globe valves are engineered for precision control.
One of the prime benefits of globe valves is their ability to provide a tight sealing mechanism. This capability minimizes leakage and enhances energy efficiency, particularly in systems operating under variable flow conditions. Being hydraulically balanced, globe valves significantly reduce the operational torque needed, thereby prolonging service life and decreasing maintenance costs. As a result, industries dealing with steam, oil, gas, and water systems frequently rely on globe valves for both safety and efficiency.
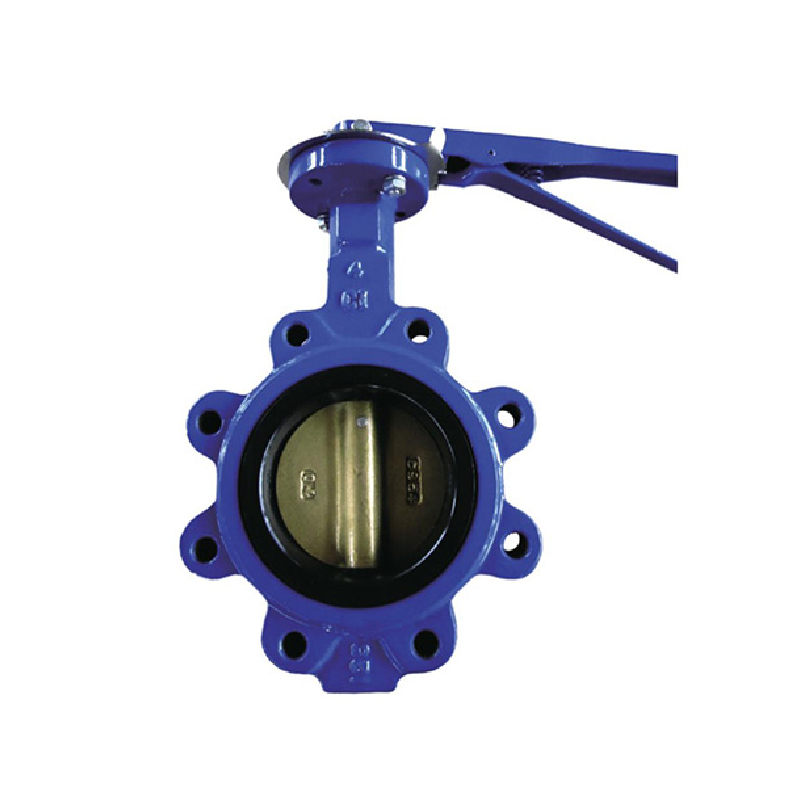
Moreover, the versatility of globe valves cannot be overstated. Available in a range of sizes, materials, and configurations, these valves can be tailored to withstand extreme pressures and temperatures, making them suitable for high-performance systems. Materials commonly used include stainless steel, carbon steel, and various alloys, ensuring compatibility with different types of media. This adaptability ensures that they are well-suited for use in corrosive and high-temperature environments.
globe valve
The construction of globe valves allows for easy maintenance and replacement of parts, a considerable advantage in industries where downtime can lead to significant financial losses. With their top-entry design, operators can quickly access internal components for repairs, thus minimizing downtime and maintaining operational continuity. This design feature also supports the critical requirement of maintaining system integrity in high-stakes environments such as chemical plants and oil refineries.
The efficacy of globe valves in control applications is further enhanced by advancements in automation and digitalization. Many modern systems integrate these valves with smart actuators and sensors, enabling precise, automated flow control and real-time monitoring. This integration facilitates predictive maintenance, improves operational efficiency, and enhances safety measures by providing instant alerts to potential system anomalies.
Expertise in selecting the right globe valve for an application involves a thorough understanding of the system requirements and the specific properties of the media involved. Engineers and procurement specialists must consider factors such as pressure ratings, temperature ranges, and flow characteristics.
Knowledge of these elements ensures optimal valve performance and longevity, aligning with industry standards and regulations.
In summary, globe valves are a critical component in modern industrial systems, praised for their ability to deliver exact control and reliability. Their durable construction, ease of maintenance, and adaptability to various environments make them essential in managing complex fluid dynamics. When correctly implemented, they contribute significantly to operational efficiency, system safety, and cost-effectiveness, underscoring their authoritative role in industrial valve solutions.