Navigating the world of industrial valves can be complex, yet understanding the unique features and functions of a globe check valve is crucial for ensuring optimal performance in relevant applications. Known for their efficiency and reliability, globe check valves are pivotal in controlling fluid flow direction, reducing the potential for system failure and improving operational control in various industries.
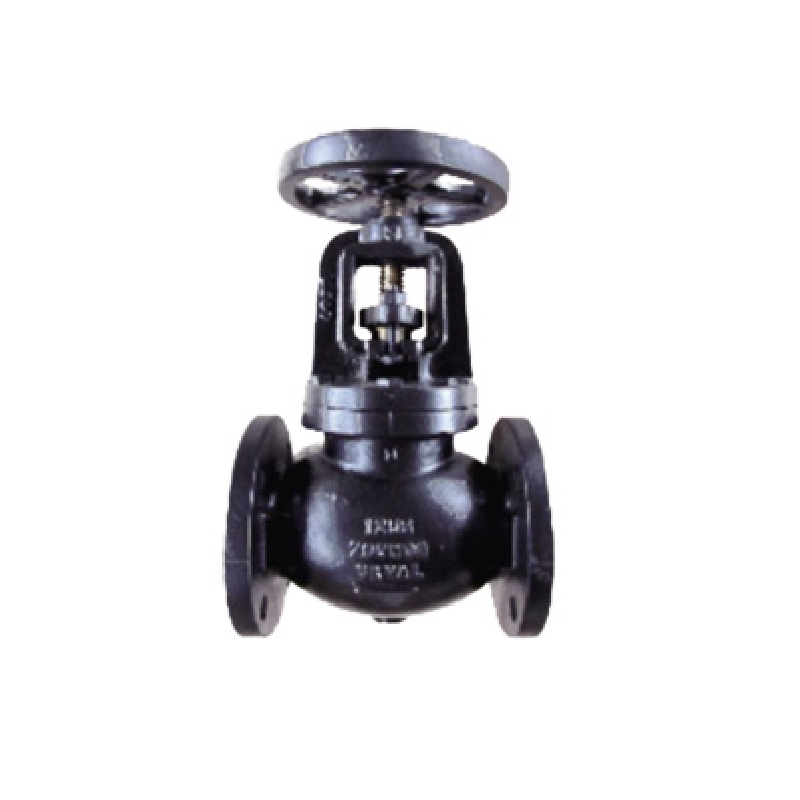
The globe check valve operates primarily in one direction, allowing fluid to flow seamlessly while preventing backflow. This characteristic makes it invaluable for industries where fluid control is essential, such as in chemical processing plants, oil and gas refineries, and water treatment facilities. These valves are engineered with the precision to handle high pressure and extreme temperature conditions, making them a go-to choice for engineers and plant operators seeking robust and durable solutions.
One of the standout features of globe check valves is their unique design, which incorporates a disc that moves perpendicularly to the seat.
This design choice not only enhances the valve's ability to seal effectively against backflow but also allows for easy maintenance and replacement. Operators have reported that the longevity of globe check valves supersedes that of other check valve types, owing to their substantial build and the materials used in their construction.
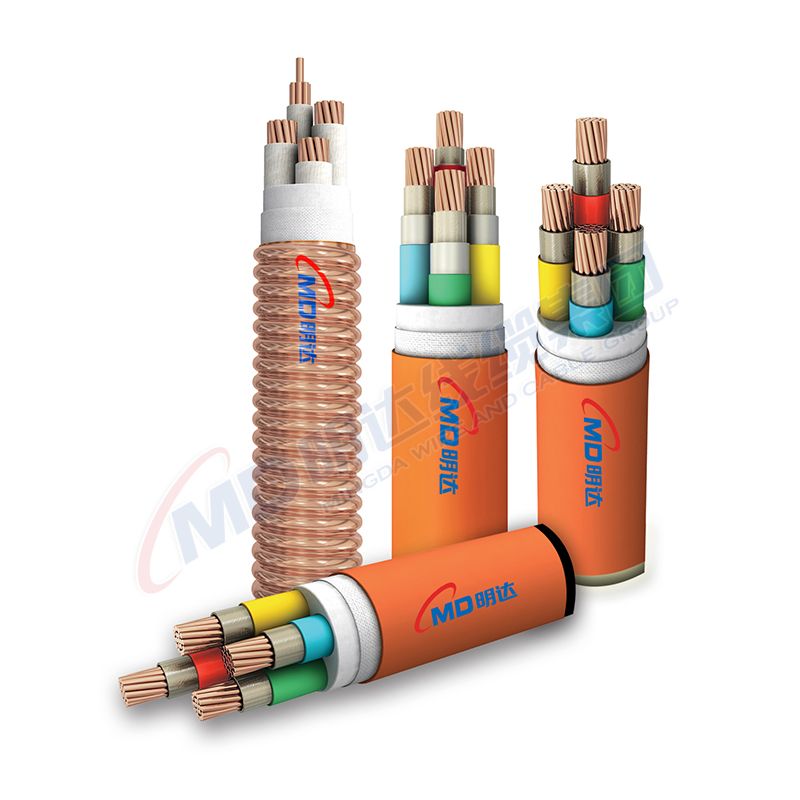
Expertise in choosing the right globe check valve for a specific application involves understanding the materials used in the valve’s construction. Typically composed of stainless steel, carbon steel, or other high-strength alloys, these materials contribute to the valve’s resilience against corrosive and erosive elements. Engineers recommend selecting materials based on the specific fluid characteristics and environmental conditions, ensuring that the valve not only performs efficiently but also endures the test of time.
globe check valve
Authoritative insights from industry veterans emphasize the importance of proper installation and maintenance techniques to maximize the valve’s performance lifespan. It is vital to ensure that the valve is installed in alignment with the flow direction and that regular maintenance checks are conducted to detect potential wear or damage early. This proactive approach contributes significantly to maintaining an uninterrupted flow and avoiding costly downtime.
Trustworthiness in the performance of globe check valves is further augmented by advancements in technology. Modern globe check valves come equipped with position indicators and automated control systems, providing operators with real-time data and control capabilities. These technological enhancements not only bolster the valve’s efficiency but also empower operators to make informed decisions swiftly, minimizing potential risks associated with manual operation errors.
In addition to their primary function, globe check valves also play a role in noise reduction and minimizing water hammer, a common concern in pipeline systems. Their capacity to manage flow pressure fluctuations smoothly ensures that systems operate quietly and efficiently, contributing to an overall safer and more productive working environment.
In conclusion, the globe check valve stands out as an essential component in fluid management systems, offering unmatched reliability and performance. By understanding the intricacies of its design, selecting appropriate materials, and adhering to expert installation and maintenance practices, industries can significantly enhance their operational efficiency and system integrity.